CAMX 2019 exhibit preview: MultiMechanics
MultiMechanics is showcasing its MultiMech 19.0 composite modeling and simulation software.
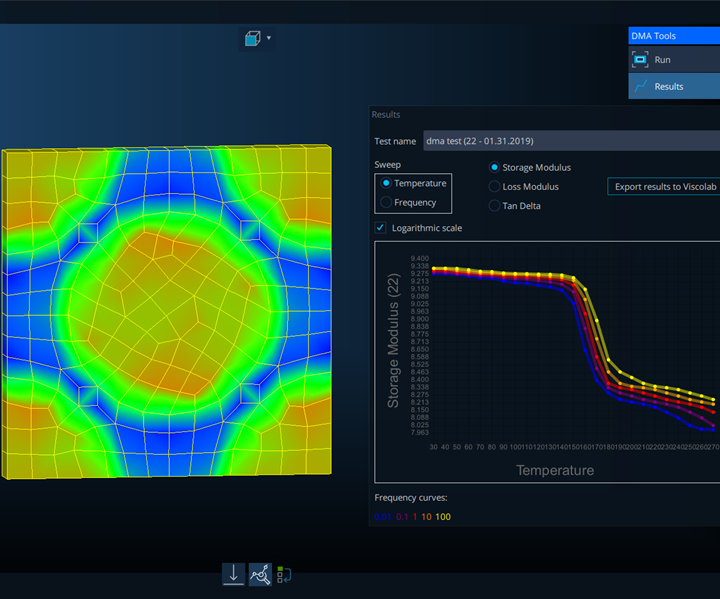
Source | MultiMechanics
MultiMechanics (Omaha, Neb., U.S.) is showcasing its MultiMech 19.0 composite modeling and simulation software. Released in March of this year, MultiMech 19.0 features include:
- a new bi-modulus elastic model to enable engineers to better capture the mechanical behavior of carbon fibers,
- virtual DMA to more easily characterize the viscoelastic behavior of complex microstructures,
- parallel runs in Optimizer mode to reduce the job runtime,
- new material and failure models, including continuum damage models for orthotropic materials and new damage laws enabling users to capture unique material behavior with higher accuracy,
- enhancements to linear solver, including improved automated time step and optional displacement convergence check, as well as the ability to check for large displacements in the nonlinear solver, and
- a redesign of the material database and enhancements to speed up the workflow.
Related Content
-
Proving thermoplastic composites match carbon fiber/epoxy performance in road bikes
CDCQ, LxSim, Addcomp and Argon 18 collaborate to optimize a carbon fiber/PA6 bike seat post, democratizing AFP and demonstrating materials and process for future designs and production.
-
Improving carbon fiber SMC simulation for aerospace parts
Simutence and Engenuity demonstrate a virtual process chain enabling evaluation of process-induced fiber orientations for improved structural simulation and failure load prediction of a composite wing rib.
-
Plant tour: BeSpline/Addcomp, Sherbrooke, QC, Canada
Composites automation specialist increases access to next-gen technologies, including novel AFP systems and unique 3D parts using adaptive molds.