Automated Tape Laying (ATP) / Automated Fiber Placement (AFP)
Automated Tape Placement (ATP) and Automated Fiber Placement (AFP) are advanced manufacturing techniques revolutionizing the production of composite structures. These robotic technologies precisely lay down continuous fibers or tape onto molds or mandrels to create intricate, high-performance composite components. ATP involves the automated placement of composite tape, while AFP handles the precise laying of individual tows of fibers.

Latest ATL/AFP Articles
VIEW ALLCygnet Texkimp relaunches customer slitting trials at UK Innovation Centre
A production-scale prepreg tape slitting system featuring SAHM winding technology is available for thermoset, thermoplastic and ceramic tape trialing following an Asia contract win.
Read MoreClean Aviation's regional aircraft technology testbed #2 demonstrates advances with composites
European project advances OOA outer wing box using resin infusion and thermoplastic composite technologies.
Read MoreSmart composites equipment advances aerocomposites innovation
CAMX 2025: From fiber to flight, Broetje-Automation innovates composites manufacturing with integrated AFP, drilling and sealing technologies.
Read MoreDLR study considers cast PA6 molds for in situ AFP composites
3D printed thermoplastic mold was analyzed as alternative to expensive, time-consuming metallic molds and for suitability in aerospace-grade composite structure fabrication.
Read MoreSensory consolidation roller for laser-based AFP enables innovative temperature measurement
Within the InSiTe project, IFW has demonstrated embedded fiber optic sensors for continuous measurement of temperature in the area of compaction with high spatial resolution up to 0.65 millimeter.
Read MoreCoriolis Composites heightens U.S. presence to empower AFP
With innovation, expertise and a deep commitment to its partners’ success, France-based Coriolis Composites is actively strengthening its strategic footprint across North American composites manufacturing.
Read MoreKnowledge Centers
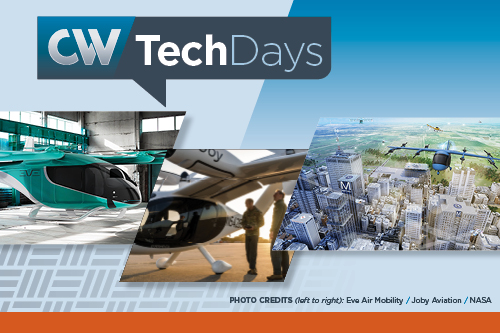
Explore the cutting-edge composites industry, as experts delve into the materials, tooling, and manufacturing hurdles of meeting the demands of the promising advanced air mobility (AAM) market. Join us at CW Tech Days to unlock the future of efficient composites fabrication operations.
LEARN MORELatest ATL/AFP News And Updates
Automated composites processing systems facilitate customization, productivity
CAMX 2025: Mikrosam’s filament winding, prepreg slitting and rewinding, towpreg, AFP/ATL and flexible double-belt press prepreg equipment meet precision and quality demands.
Read MoreCoriolis Composites introduces the C3 dockable AFP head
AFP solution for gantry and robot systems offers manufacturers enhanced flexibility, performance and ease of use for a wide range of composite parts.
WatchMikrosam AFP work cell to enhance Qarbon's TPC part development
Commission of a Libra-series robotic AFP system, paired with Toray’s Cetex thermoplastic composite materials, will accelerate Qarbon Aerospace’s development timelines and reduce risk in future aerospace qualification efforts.
WatchTPRC develops continuous optical reflection characterization setup for AFP
As part of the NXTGEN Hightech program, developer Joran Geschiere achieved a setup that can characterize entire spool lengths of UD tape meant for the AFP process.
WatchMcLaren develops aerospace-inspired ART method for volume composite super car engineering
Automated rapid tape (ART) technique, already deployed at the MCTC and to be used for future McLaren models, is capable of producing lighter, stiffer and stronger carbon fiber structures with less waste.
WatchConbility thermoplastics system installation supports TITK R&D
LATW and tape winding machine enhances TITK Rudolstadt’s ability to conduct advanced thermoplastic R&D projects, particularly for aerospace.
Read MoreFeatured Posts
Inside the MFFD — CW's coverage of the Clean Aviation multifunctional fuselage demonstrator
ÂÌñÏ×ÆÞ rounds up coverage of the MFFD project over the past decade. Now complete, the MFFD illustrates numerous processes and technologies for manufacturing primary aerospace structures using thermoplastic composites.
WatchASCEND program completion: Transforming the U.K.'s high-rate composites manufacturing capability
GKN Aerospace, McLaren Automotive and U.K. partners chart the final chapter of the 4-year, £39.6 million ASCEND program, which accomplished significant progress in high-rate production, Industry 4.0 and sustainable composites manufacturing.
Read MoreVIDEO: Flexible molding and machining for composites
Addcomp and bespline are sister companies that offer innovative solutions for composites. This video from CAMX 2024 offers an overview of Addcomp’s AFP solutions.
WatchComposites end markets: New space (2025)
Composite materials — with their unmatched strength-to-weight ratio, durability in extreme environments and design versatility — are at the heart of innovations in satellites, propulsion systems and lunar exploration vehicles, propelling the space economy toward a $1.8 trillion future.
Read MoreDesign for manufacturing, assembly and automation enables complex CFRP telescope supports
Airborne delivered two mirror support structures for the FYST and SOLAT telescopes, assembling 26,300 components while maintaining near-zero CTE, strict tolerances on 6.5 × 6.5 × 1.8-meter assemblies.
WatchProving thermoplastic composites match carbon fiber/epoxy performance in road bikes
CDCQ, LxSim, Addcomp and Argon 18 collaborate to optimize a carbon fiber/PA6 bike seat post, democratizing AFP and demonstrating materials and process for future designs and production.
Read MoreFAQ: ATL/AFP
What is the difference between AFP and ATL?
AFP involves the precise placement of continuous fibers onto a mold surface in a predetermined pattern, often in complex shapes, while ATL uses preimpregnated tape to lay down fiber strips onto a surface, typically in straight or curvilinear paths.
What materials can be used in AFP/ATL?
Both AFP and ATL commonly work with materials like carbon fibers, fiberglass, aramid, and thermoplastic or thermoset matrices tailored to specific application requirements.
What are the advantages of AFP/ATL over traditional manufacturing methods?
These technologies offer enhanced precision, reduced material waste, improved structural integrity, and the ability to create complex parts with optimized fiber orientations, resulting in lighter and stronger components.
Are there limitations to AFP/ATL?
Challenges can include high initial equipment costs, complexities in programming intricate designs, and the need for skilled operators to ensure precise placement and quality control.