Converting carbon fiber for UHTCMC to 3500°C
Advanced Ceramic Fibers LLC demonstrates ultra-high temperature ceramic matrix composites using SiC and other metallic carbides for applications in aerospace, defense, energy and more.
Source (All Images) | Advanced Ceramic Fibers LLC
(ACF, Idaho Falls, Idaho, U.S.) has developed patented processes and materials that enable ultra-high temperature (UHT) ceramic matrix composites (CMC) and metal matrix composites (MMC) for use in aerospace and defense, turbine engines, battery and power applications, as well as space vehicles and nuclear thermal propulsion.
Silicon carbide (SiC) coated carbon fiber filaments from ACF’s Direct Conversion Process (DCP). The base carbon fiber can be seen as the black center of each filament with a uniform white SiC outer layer (left). The scanning electron micrograph (SEM) taken by NASA Glenn at right shows a 0.03-micrometer-thick SiC coating on a carbon fiber. Source | ACF, NASA Glenn
The company was founded by Dr. John Garnier in 2012 after retiring from the Idaho National Laboratory (Idaho Falls), one of the U.S. Department of Energy’s national labs known for its nuclear research. ACF’s Direct Conversion Process (DCP) claims to convert individual carbon fiber filaments with 50-300 nanometers of silicon carbide (SiC) or other metallic carbide (MC) to enable high performance in CMC up to 3500°C and beyond.
DCP carbon fiber to Fi-Bar
DCP was one of the company’s first patents, explains Ken Koller, CEO of ACF. “It takes carbon fiber and forms a very thin layer of SiC or MC on each individual filament in that carbon fiber tow.” The result is a product called FiBar that has integrated thermal protection enabling the carbon fiber to withstand temperatures up to 3940°C in vacuum. “If you had pure carbon fiber at 3500°C in a vacuum,” says Koller, “an inch of that material would vaporize in less than 3 seconds. But the SiC or MC that we integrate into the filaments now protects the fiber and suppresses that vaporization for tens of minutes.”
ACF can use 34 metallic carbides to produce Fi-Bar products using DCP.
Koller explains that DCP is a continuous process that is completed in seconds. “The resulting fiber tows are called Fi-Bar because they act like rebar to reinforce metal and ceramic matrix materials,” he adds. “Depending on the application requirements, we can use 34 of the metallic carbides in the periodic table, including tantalum [Ta], hafnium [Hf], zirconium [Zr], titanium [Ti] and others, to tailor the Fi-Bar for its intended use.” Note, carbides, borides and nitrides made with these elements are currently the most popular for achieving UHTCMC.
ACF reports another advantage of using DCP is that the integrated SiC or MC in the fiber tow also acts as the interfacial debond layer for the CMC. Though not required for CMC using oxide fibers and matrices, CMC using carbides do need it to ensure the good/not great adhesion between fiber and matrix that enables fiber pullout to reduce crack growth. This interfacial debond layer can also help non-oxide fibers resist oxidation. Traditionally, such coatings were achieved using a chemical vapor deposition/infiltration (CVD/CVI) process that is lengthy and expensive (see “A new era for CMC: Continuous fiber coating”). Supplanting this step by using a fiber already treated via DCP could thus reduce manufacturing time and cost.
Koller also points out that DCP enables highly tailored CMC, with different MC elements or recipes modified to meet specific applications and requirements. “For example, each one of these MC elements can apply unique properties to the fiber, such as conductive, catalytic or electromagnetic properties,” he says.
Any kind of carbon, PIP with 2-3 cycles
ACF can convert anything that’s carbon — tow, chopped fiber, braid or tape, says Koller. “We can also do PAN or pitch carbon fiber, as well as CNT [carbon nanotubes], graphene, graphene flakes or particles, which are basically additives that we put into the matrix to achieve some beneficial properties. He explains that DCP works well with so many different formats, because the MC follows the contour of the structures being coated, whether that’s a kidney-shape carbon tow filament or a graphene flake.
Spools of carbon fiber and woven fabric converted to Fi-Bar using DCP.
Fi-Bar maintains the high tensile strength of intermediate modulus or high modulus carbon fiber (800 ksi/5.5 gigapascals). “We can also design the fiber preform and fabricate the CMC with a strain-to-failure as high as 8%, while most other carbide CMC shows 2% or less,” notes Koller. “That’s a game-changer for higher toughness and more robust parts. This was validated by Naval Air Systems Command [NAVAIR] in a combined shaft bend test and FOD [foreign object damage] test where Mach 1 steel projectiles were fired at these materials followed by four-point bending tests per ASTM C1684.”
ACF uses Fi-Bar to make CMC through a standard polymer impregnation and pyrolysis (PIP) process, where reinforcements are infiltrated with pre-ceramic resin at room temperature and then pyrolized at temperatures ≥900°C to form CMC. “We infiltrate the carbon fiber with the UHTCMC matrix as a slurry and then make the composite using hand or press layup, pressure casting, winding or additive manufacturing,” says Koller. “We then pyrolyze the composite to form the CMC. The solids loading in the green CMC can be formed to as high as 60-70% solids level with the SiC/C filaments, then the number of PIP cycles required to achieve a dense CMC can be reduced from eight to nine cycles to as low as two to three cycles, depending on the part. This again reduces manufacturing time and cost.
”Another benefit is the volume percentage of carbon fiber can be as high as 70%, which enables higher composite load-carrying and thermal shock capacity for all the flavors of the carbide CMC — including C/C, C/SiC, C/C-SiC and UHTCMC.” He adds that UHTCMC would typically be a type of diboride with a lower volume percentage of fiber. “Some of the CMC we are producing using tantalum carbide [TaC] and other high melting point carbides can withstand even higher temperatures than diborides in oxidizing environments.” He explains this is because the carbides do not contain boron, which readily oxidizes in oxygen at elevated temperature if not protected.
Applications, commercialization
ACF has been awarded seven Phase I and three Phase II . These include a 2014-FY SBIR with the U.S. Navy, which included a Phase I to fabricate carbon fiber/MC test coupons for use in CMC matrices to be used in Phase II to develop new turbine engine designs using CMC parts with capability above 1480°C. Another project, was with the U.S. Navy Strategic Systems Programs (SSP) to develop advanced high-temperature ceramic fibers with high strength, low dielectric constant, low loss tangent, high thermal stability and high oxidation resistance for missile and projectile system applications.
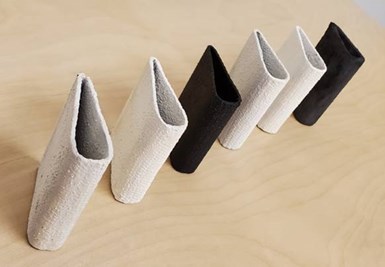
In 2020, five turbine engine vane designs made with different Fi-Bar CMC were tested to 1371°C, with one version reaching 1716°C.
In 2021, CW’s Hannah Mason reported on ACF’s continued work with the U.S. Office of Naval Research (ONR) toward CMC components for turbine engines and also with Johns Hopkins Applied Physics Lab (APL) to explore use of CMC for the concept being developed with NASA (see “Researchers work to develop UHTCMC …”). This vehicle could be the first to approach the speed of light for space travel.
In its work with ONR, five NASA-designed turbine engine vanes made with different iterations of ACF’s Fi-Bar CMC were tested up to 1371°C. One version was able to reach 1716°C with no significant damage.
ACF has produced and tested (left, clockwise) UHTCMC fasteners, nose tips, C/TaHf samples and cross-sections of turbine engine vanes.
ACF also worked with ONR to explore UHTCMC fasteners. The image at left shows a demonstrator fastener that withstood 600 pounds of load in testing at 2000°C as well as projectile testing at Navy facilities. “The ONR chief scientific officer that performed the FOD testing was amazed at how well it performed,” says Koller. “We made these using PIP with five cycles. They have no environmental barrier coating [EBC] or thermal barrier coating [TBC] because the CMC made with Fi-Bar is also self-repairing. When impact damage occurs at elevated temperature, the composite will reform a thin external oxide layer, once again protecting the underlying composite.
“We recently responded to a request from a customer,” he continues, “and made carbon/TaHf nose tips sized roughly 1-inch in diameter and 1.4 and 1.7 inches long. These are the highest temperature materials known. We made each nose tip in a day from green bodies casted as blocks containing short fibers and matrix, but these were just in-house R&D and not optimized. We have also made turbine engine vanes for military aircraft turbine engines which were tested successfully.”
As explained in the 2021 CW article, for the Interstellar Probe project, ACF worked with Johns Hopkins APL to produce CMC samples that were tested using vacuum heating and plasma torches. “They demonstrated the ability to survive at least up to 2900°C,” says Koller, “with potential for even higher temperatures.” Hannah Mason noted that APL’s initial report concluded:
“The results of this Phase I project have demonstrated the potential for development of an entirely new class of materials with UHT capability.”
“We are enabling materials and parts that show much higher temperature capability than metals or other CMC,” says Koller, “as well as greater resistance to corrosion, fatigue and oxidation. And we can tailor dielectric and electromagnetic properties, which is key for many aerospace, defense, energy and consumer electronic applications.”
While many other CMC producers are focused only on SiC or oxides, notes Koller, “ACF’s use of DCP enables a palette of unique metal carbide ‘enabled’ reinforcements to be made using much lower cost carbon fiber from many existing high-volume suppliers. We are now installing individual direct conversion processing systems each capable of producing larger daily quantities of Fi-Bar product specific to individual client applications and needs for affordable, lower-cost and higher-performance continuous and chopped fibers.”
Related Content
A new era for ceramic matrix composites
CMC is expanding, with new fiber production in Europe, faster processes and higher temperature materials enabling applications for industry, hypersonics and New Space.
Read MoreDITF Denkendorf advances sustainable carbon fibers, oxide fibers for CMC and more
The German Institutes of Textile and Fiber Research are targeting more sustainable carbon fiber via low-pressure stabilization and bio-based precursors, and working with Saint-Gobain to commercialize oxide ceramic fibers for CMC.
Read MoreSRI develops scalable, infiltration-free ceramic matrix composites
Work in two DOE projects is demonstrating C/C-SiC produced in 3-5 days with <5% shrinkage, <10% porosity and 50% the cost of conventional C/C and C/C-SiC.
Read MoreFirefly Aerospace to develop CMC rocket engine nozzle extension
Contracted by the AFRL, Firefly will use its expertise to design, build and test a composite-based nozzle extension to reduce costs, improve performance and accelerate rocket engine production.
Read MoreRead Next
Near-zero erosion ultra-high temperature CMC
K3RX commercializes UHTCMC for a wide range of markets, demonstrating performance in prototypes, assemblies and advancing manufacturing to reduce cost.
Read MoreA new era for ceramic matrix composites
CMC is expanding, with new fiber production in Europe, faster processes and higher temperature materials enabling applications for industry, hypersonics and New Space.
Read MoreCarbeon C/C-SiC ceramic matrix composites without fiber coating
Dutch startup Arceon is working with leaders in space, hypersonics and industry to test its Carbeon CMC, validating near-net-shape parts with <3% porosity and performance at 1600ºC, targeting UHTCMC and a presence in the U.S. in 2025.
Read More