Composites Design & Simulation
Designers of composite parts can choose from a huge variety of fiber reinforcements and resin systems, a situation that gives infinite design freedom but adds to composites’ complexity. Along with cost factors, knowledge of material properties is a prerequisite to satisfactory product design. The mechanical properties, orientation, and type of fibers; the properties of the resin; the fiber-to-resin ratio and behavior of the combined materials; and the intended fabrication process are all factors to consider in the design of a composite part.

Latest Design/Simulation Articles
VIEW ALLTroubleshooting thermoplastic composite stamp forming
Understand the basic science of TPC stamp forming, a manufacturing process steadily gaining momentum in aerospace and mobility applications thanks to its rapid forming, short cycle times and automated methods.
Read MoreCutting 100 pounds, certification time for the X-59 nose cone
Swift Engineering used HyperX software to remove 100 pounds from 38-foot graphite/epoxy cored nose cone for X-59 supersonic aircraft.
Read MoreSeoul National University VABS to design UAM, rotorcraft blades
University conducts research to establish conceptual and detailed design methodologies applicable to composite UAM systems and to develop digital twin technologies that can be used in aerospace.
Read MoreEngineering simulation software, technical expertise supports composite, metallic systems
CAMX 2025: SDA Software presents its composite structures, materials consulting and engineering solutions leadership, delivering mission-critical designs for UAVs, manned vehicles and spacecraft.
Read MoreFlorida International University leverages VABs software to optimize composite aerospace structures
AnalySwift high-fidelity modeling software enabled the university to identify optimal configurations for structures including wings and antennas, maximizing longevity, enhancing safety and expanding function.
Read MoreUsing multidisciplinary simulation, real-time process monitoring to improve composite pressure vessels
Multi-pronged approach closes the loop between design and production of Type 3, 4 and 5 pressure vessels, enabling simulation of as-built composite tanks to improve performance and storage capacity while reducing weight and cost.
WatchKnowledge Centers
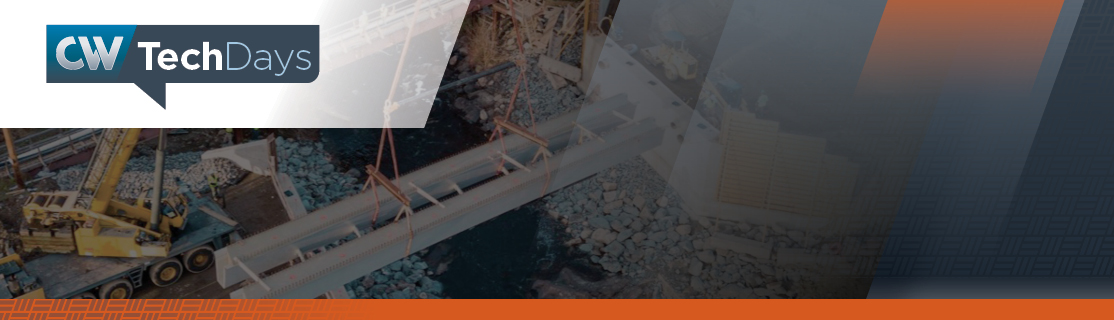
ÂÌñÏ×ÆÞ’s CW Tech Days: Infrastructure event offers a series of expert presentations on composite materials, processes and applications that should and will be considered for use in the infrastructure and construction markets.
LEARN MORELatest Design/Simulation News And Updates
Wichita State, Dassault Systèmes open Manufacturing Innovation Center
Aviation companies of all sizes will be able to improve their resilience and efficiency via the center’s virtual design, automation and additive manufacturing capabilities.
Read MoreCactuX in-situ BOX simulates real-life conditions of composite samples during CT analysis
The autonomous in-situ BOX combines the environment temperature control function and power supply function, enabling new possibilities for material and internal structure research.
Read MoreArtist Studio software update streamlines FPP design, programming
Cevotec releases enhancement for the design, robot programming and system performance of its composites software, helping users work more efficiently with fiber patch placement.
Read MoreGenerative Orthoses project to reshape orthopedic care
CRP Technology, MHOX and Istituto Ortopedico Rizzoli, one of the winners of the WORTH Partnership Project II, have developed bespoke orthoses using generative design, Windform GT fiberglass materials and PBF.
Read MorePAIramid project drives digital approach to streamline composite aerostructures development, deployment
Multidisciplinary global team will leverage Al and data-driven simulations to make the aerostructure design, development and certification process faster, less costly and more reliable.
Read MorePolaron AI materials design tool wins inaugural Manchester Prize
Generative AI model is capable of exploring thousands of material designs in under a day, providing an opportunity to more rapidly characterize and design advanced materials including alloys, composites and catalysts.
Read MoreFeatured Posts
ASCEND program completion: Transforming the U.K.'s high-rate composites manufacturing capability
GKN Aerospace, McLaren Automotive and U.K. partners chart the final chapter of the 4-year, £39.6 million ASCEND program, which accomplished significant progress in high-rate production, Industry 4.0 and sustainable composites manufacturing.
Read MoreCrashworthiness testing of composites: A building block approach, Part 2
Following the previously discussed coupon-level testing element, subcomponent and component testing are the next steps in designing crashworthy composite structures.
Read MoreCarbon fiber/flax landing gear achieves 54% weight reduction via tailored layup optimization
Fuko’s Biogear showcases how strategic composite material distribution and natural fiber damping properties can lightweight and enhance critical aerospace structure performance.
Read MoreSchrödinger advances materials informatics for faster development of next-gen composites
Cutting time to market by multiple orders of magnitude, machine learning and physics-based approaches are combined to open new possibilities for innovations in biomaterials, fire-resistant composites, space applications, hydrogen tanks and more.
Read MoreProving thermoplastic composites match carbon fiber/epoxy performance in road bikes
CDCQ, LxSim, Addcomp and Argon 18 collaborate to optimize a carbon fiber/PA6 bike seat post, democratizing AFP and demonstrating materials and process for future designs and production.
Read MoreModeling and characterization of crushable composite structures
How the predictive tool “CZone” is applied to simulate the axial crushing response of composites, providing valuable insights into their use for motorsport applications.
Read More