Composites Use in Automotive
Composites are used frequently in motorsports and lower volume, high-end/luxury vehicles, which typically favor continuous carbon fiber materials. They are also often used to fabricate exterior structures in racing vehicles, where their relative light weight provides speed and performance advantages over metals. Within mid- and high-volume production vehicles, common composite applications include glass fiber-reinforced polymer (GFRP) leaf springs, suspension components, and drive shafts, sheet molding compound (SMC) body panels and frames; bulk molding compound (BMC) housings and support structures; and injection-molded thermoplastics for bumper frames, lift gates and seat structures.

Latest Automotive Articles
VIEW ALLISCC Plus validates Teijin Aramid’s use of alternative feedstocks in Twaron fiber production
The certification ensures that Twaron-based tire components can be produced with bio-based and recycled feedstocks while maintaining high performance standards.
Read MoreHexagon Agility lands major CNG orders in Mexico and Jordan to advance clean energy transition
Deployments will supply onboard CNG fuel systems for 100 Cummins X15N-powered trucks in Mexico’s largest fleet and deliver ADR X-Store Mobile Pipeline modules to Jordan’s Watani in deals set to begin delivery in Q3 2025.
Read MorePolestar 3 sets World Record for longest electric SUV journey on single charge
Unmodified Polestar 3, which uses natural fiber composites in its interiors, achieves 935.44 kilometers on a single charge on U.K. public roads.
Read MoreAmanda Nummy gives fourth keynote at SPE ACCE 2025
Senior polymer engineer at Hyundai Automotive Technical Center Inc. will analyze strategies for balancing objectives in automotive composites design.
Read MoreIACMI’s Chad Duty presents SPE ACCE 2025 third keynote
Duty will share the ways in which IACMI, over its 10-year history, has led to successful and commercialized composites technologies in the automotive industry.
Read MoreKautex Textron wins BEV battery housing contract with automotive OEM
Order for full BEV lower battery housing unit will incorporate Kautex’s thermoplastic composite (TPC) Pentatonic battery enclosure product, which enhances thermal management and reduces vehicle weight.
Read MoreKnowledge Centers
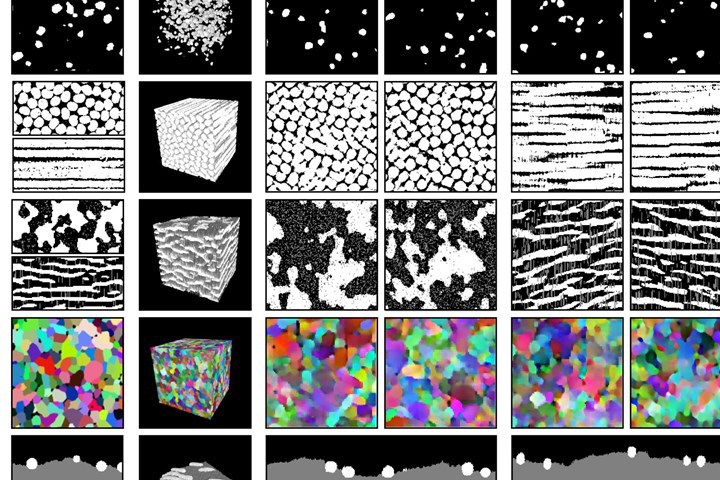
Review the state of the art in design, simulation, failure analysis, digital twins, virtual testing and virtual inspection.
LEARN MORE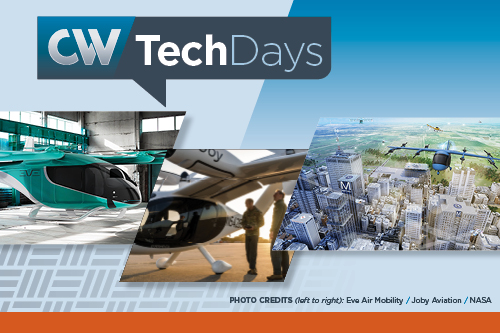
Explore the cutting-edge composites industry, as experts delve into the materials, tooling, and manufacturing hurdles of meeting the demands of the promising advanced air mobility (AAM) market. Join us at CW Tech Days to unlock the future of efficient composites fabrication operations.
LEARN MORELatest Automotive News And Updates
Consumer goods manufacturer orders Hexagon Agility CNG fuel systems
Following successful piloting of X15N engine natural gas trucks, this new fleet of 60 day cab and sleeper trucks will benefit from Hexagon’s CNG systems with Type 4 tanks.
Read MoreHTMS joins Mobilise accelerator program to advance its CMC materials
High Temperature Material Systems has developed low-temperature cure prepregs for ceramic matrix composite (CMC) parts offering lightweight and thermal/fire protection up to 1000°C.
Read MorePUR sandwich panels enable 3D composite parts
CAMX 2025: Ascorium Industries is highlighting CompoLite technologies for the production of lightweight, dimensionally stable automotive components and structures.
Read MoreDurability, precision and intelligent automation in composites processing
CAMX 2025: Precision and power is part of Langzauner’s engineering-driven philosophy, characterized through its high-performance press systems and turnkey automation solutions for aerospace and automotive.
Read MoreCompPair advances HealTech composites in real-world solutions
New projects, collaborations and sustainability efforts highlight the prospect of healable materials for automotive, AAM, space and beyond.
Read MoreGraphmatech secures €2.5 million EU grant for Uppsala pilot facility
Funding will scale the Swedish startup’s polymer-graphene hydrogen storage lining, made for Type 4 tanks and pipelines, with plans to deploy in commercial vehicles by 2027.
Read MoreFeatured Posts
Composites end markets: Automotive (2025)
Composites manufacturing intelligence drives circular economy solutions as automotive industry balances technical demands with sustainability mandates.
Read MoreInfused sandwich window frame components help double-decker buses meet weight targets
Prototype GFRP parts were evaluated by Spanish bus manufacturer Carrocerías Ayats as an initial move toward lighter, more efficient, more automated parts and processes.
Read MoreBucci Composites expands automotive production capabilities with facility addition, new high-ton presses
CW Top Shops recipient Bucci Composites shares an update on its facility expansion, automotive composites applications, sustainability, education initiatives and more.
Read MoreSpanish startup to ramp up production of “recyclable” EV prototype
Liux’s BIG electric vehicle features multiple structural components manufactured via RTM from flax fabric and a thermoset resin said to enable the entire component to be recycled and reused again.
WatchPlasma moves beyond improved bonding to coatings, multifunctional composites
Plasmatreat cold plasma systems clean, activate surfaces and apply nanocoatings for dielectric barriers and more.
WatchASCEND program completion: Transforming the U.K.'s high-rate composites manufacturing capability
GKN Aerospace, McLaren Automotive and U.K. partners chart the final chapter of the 4-year, £39.6 million ASCEND program, which accomplished significant progress in high-rate production, Industry 4.0 and sustainable composites manufacturing.
Read MoreFAQ: Automotive
How are composites used in automotive structures?
Within mid- and high-volume production vehicles, common composite applications include glass fiber-reinforced polymer (GFRP) leaf springs, suspension components, and drive shafts, sheet molding compound (SMC) body panels and frames; bulk molding compound (BMC) housings and support structures; and injection-molded thermoplastics for bumper frames, lift gates and seat structures.
As electric vehicles (EV) become more prevalent on the road and in development by automotive manufacturers, new opportunities exist for composites and composite materials development. For example, a lighter-weight, composites-intensive vehicle is likely capable of driving for a longer range between charges. Battery enclosures present one large market opportunity in the EV market.
Why use composites for electric vehicle (EV) battery enclosures?
As the automotive industry rapidly electrifies its fleets, interest is growing among OEMs and battery module producers in using composite materials for battery enclosures — covers and trays that hold and protect the frames and battery cells themselves.
There are many reasons for this, including the ability to reduce mass and stack tolerances, the fact that battery enclosures are multicomponent assemblies and poor impact performance of metals. In each of these areas, composite battery enclosures offer quantifiable benefits versus metals: lower mass, higher design freedom with greater space efficiency, faster assembly, no corrosion, greater durability and — with specific formulations — better flame resistance/fire containment.
Source: Price, performance, protection: EV battery enclosures, Part 1