Pultrusion Process for Composites
Pultrusion is a manufacturing process integral to composite production, involving the continuous pulling of reinforcing fibers through a resin bath and then through a shaping die, where they are cured and formed into a constant cross-sectional profile. This method, known for its efficiency and precision, is commonly used for producing continuous profiles with consistent dimensions and exceptional strength.

Latest Pultrusion Articles
VIEW ALLExel GFRP tubes improve QHeat geothermal energy storage
Installation of pultruded composite underground collector pipes have greatly enhanced the energy efficiency of Qheat’s geothermal wells.
Read MoreCannon introduces in-line resin degassing unit for infusion, RTM and pultrusion processes
Fully automatic system for processing large composite structural parts reduces overall degassing time in a single compact unit.
Read MoreExel, Flying Whales advance airship R&D collaboration
This time, Exel has signed a contract to deliver 75 kilometers of pull-wound carbon fiber tubes for the LCA60T VTOL aircraft.
Read MoreFiber composite technologies target construction, industrial 3D printing markets
JEC World 2025: KraussMaffei presents innovations for lightweight composite construction and surface technologies, from HP-RTM, LFI and ColorForm to the printCore extruder.
Read MorePulFlex introduces pultruded Flex Connect
Fiberglass T-slot, primarily used for automation, framing and other quick setup systems, competes with aluminum alternatives.
Read MoreExel secures design patent extension for pultruded fiberglass radomes
Technique for antenna radomes forms “functional zones” inside composite material, enhancing existing 5G technology performance, application potential.
Read MoreKnowledge Centers

Join us for insights into advanced bonding techniques and welding processes for composite materials to ensure durability and structural integrity.
LEARN MORE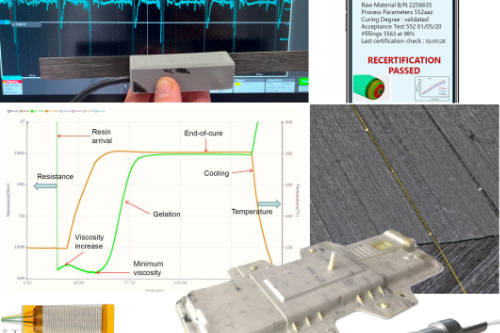
Discover the types of sensors being used in composites, the physics on which they�re based, their installation, promised benefits and challenges, as well as the potential they offer for even further developments in smart structures.
LEARN MORELatest Pultrusion News And Updates
Exel Composites supplies fiberglass profiles for Foton electric buses
Partnership with Chinese automotive manufacturer will see the implementation of pultruded profiles in various bus models, backed by weight savings, complex geometries and long life.
Read MorePultrusion, pull-winding showcase high-volume composites production
JEC World 2024: Exel Composites offers attendees a chance to engage with company experts and learn more about continuous composite manufacturing processes across various industries.
Read MoreServo-based pultrusion machines for composite profile production
CAMX 2023: Kent Pultrusion is displaying its turnkey ServoPul servo-driven pultrusion lines and secondary equipment for handling composite profiles.
Read MoreComposite profiles bring consistent quality to Ant-X drones
Italian drone solutions provider enlists Exel Composites to deliver pultruded and pull-wound profiles that support prototype drone structure designs.
Read MoreFST-rated thermoset resin with rapid, tunable cure is designed for infusion
CAMX 2023: The nonhalogenated Harp Rapid resin system presented by Trimer Technologies achieves a low-temperature, tunable cure while attaining high mechanical properties, demonstrating its effectiveness in aerospace applications.
Read MoreBiocomposite for mobile architecture, low load-bearing applications
The German Institutes of Textile and Fiber Research and partners have developed a biocomposite well suited for support profiles and connecting nodes in construction applications.
Read MoreFeatured Posts
Pull-wound carbon fiber poles enable lightweight, compact, rigid emergency stretcher
Based on military feedback, Epsilon Composite developed an optimized, foldable stretcher that combines telescopic pull-wound carbon fiber tubes.
WatchIndustrial equipment manufacturer expands global footprint, reaches into new markets
India-based CW Top Shops honoree EPP Composites reflects on a recently successful vertical filament winding application and new pultruded FRP rebar capabilities, as well as future opportunities.
WatchRobotized system makes overmolding mobile, flexible
Anybrid’s ROBIN demonstrates inline/offline functionalization of profiles, 3D-printed panels and bio-based materials for more efficient, sustainable composite parts.
Read MoreSeat frame demonstrates next-generation autocomposites design
Light weight, simplified/cost-effective manufacturing, passenger comfort and safety informed materials and process innovations and won awards for the 2022 Toyota Tundra‘s second-row seat frame.
Read MoreNovel processes for hybrid thermoset-thermoplastic pultruded parts
CFRP pultrusion and pullwinding specialist Epsilon Composite combines thermoplastic overmolding with traditional thermoset processes, demonstrated through aircraft struts and industrial applications.
Read MorePultrusion: The basics
A primer describing what pultrusion is, its advantages and disadvantages, and typical applications.
Read MoreFAQ: Pultrusion
What is pultrusion?
Pultrusion is a manufacturing process integral to composite production, involving the continuous pulling of reinforcing fibers through a resin bath and then through a shaping die, where they are cured and formed into a constant cross-sectional profile.
What is the pultrusion process?
In a pultrusion process, fibers are pulled from a creel through a resin bath and then on through a heated die. The die completes the impregnation of the fiber, controls the resin content and cures the material into its final shape as it passes through the die. This cured profile is then automatically cut to length. Fabrics may also be introduced into the die to provide fiber direction other than at 0 degrees. Although pultrusion is a continuous process, producing a profile of constant cross-section, a variant known as “pulforming” allows for some variation to be introduced into the cross-section. The process pulls the materials through the die for impregnation, and then clamps them in a mold for curing. This makes the process non-continuous, but accommodating of small changes in cross-section.
Source: Pultrusion: The basics
What are some advantages to pultrusion?
Advantages to pultrusion include:
- This can be a very fast, and therefore economic, way of impregnating and curing materials.
- Resin content can be accurately controlled.
- Fiber cost is minimized since the majority is taken from a creel.
- Structural properties of laminates can be very good since the profiles have very straight fibers and high fiber volume fractions can be obtained.
- Resin impregnation area can be enclosed thus limiting volatile emissions.
The disadvantages include that the process is limited to constant or near constant cross-section components, and costs for heated dies can be high.
Source: Pultrusion: The basics