Covestro and ParaMatters develop anisotropic optimization software for composites
Designers and engineers can use the new optimization tool to obtain the most optimal part design based on material deposition and fiber orientation.
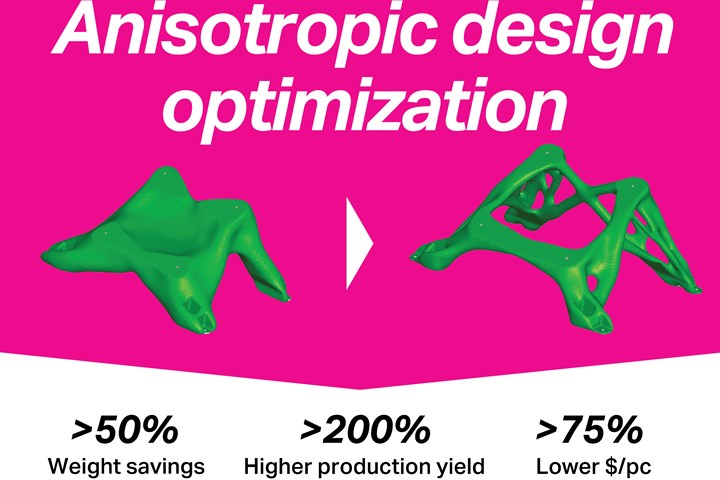
Photo Credit: Covestro
Materials company Covestro (Leverkusen, Germany) and (Ventura, Calif., U.S.), a multi-threaded generative design and manufacturing optimization software company, announced a jointly developed optimization software for anisotropic materials.
By combining ParaMatters’ expertise in design and manufacturing optimization technology and Covestro’s knowledge in engineered materials, the two companies are delivering a complete anisotropic design and workflow of filament extrusion 3D printing with fiber-reinforced materials.
According to the companies, by using the new optimization tool, designers and engineers can quickly obtain the most optimal part design based on material deposition and fiber orientation, and generate the most efficient printer toolpath. The result is materials, weight and cost savings — while maintaining part performance.
Following successful initial evaluation by leading aerospace users, including (Stade, Germany), on multiple filament extrusion printers, Covestro and ParaMatters are introducing the beta version so more users can try anisotropic materials. Users who want to join the expanding beta program, as well as providers of filament-based extrusion 3D printers that want to qualify and certify their systems, can contact ParaMatters to
Avi Reichental, ParaMatters’ co-founder and chairman, says, “We are proud to partner with Covestro and be the first to market with such a powerful design and manufacturing optimizer.”
Related Content
-
Bladder-assisted compression molding derivative produces complex, autoclave-quality automotive parts
HP Composites’ AirPower technology enables high-rate CFRP roof production with 50% energy savings for the Maserati MC20.
-
ASCEND program completion: Transforming the U.K.'s high-rate composites manufacturing capability
GKN Aerospace, McLaren Automotive and U.K. partners chart the final chapter of the 4-year, £39.6 million ASCEND program, which accomplished significant progress in high-rate production, Industry 4.0 and sustainable composites manufacturing.
-
Optimized rib-reinforced hollow composites via printed molds
Addyx topology optimization and water-soluble mandrel enables simultaneous rib and skin layup for one-shot, high-strength, lightweight structures.