Arkema's partnership with ZEBRA project commits to circular economy
Arkema’s Elium thermoplastic resins might be key to the project’s goal to design and produce the first 100% recyclable wind turbine blade.
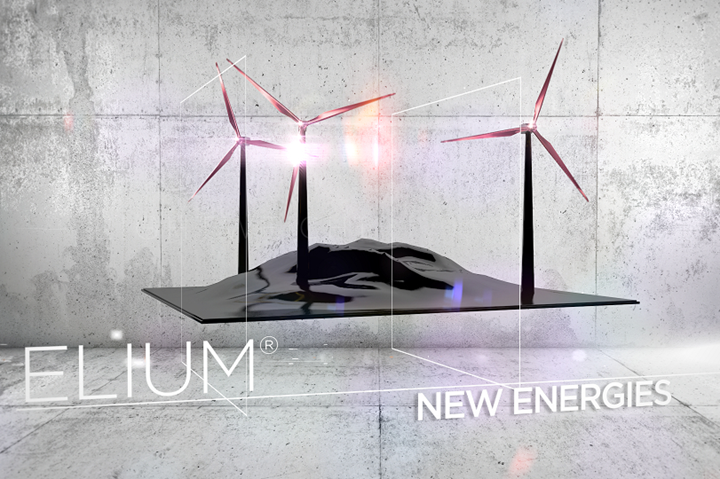
Photo Credit: Arkema
It was recently reported by (Colombes, France) that on Sept. 22 the ZEBRA (Zero wastE Blade ReseArch) consortium was launched, a project aiming to create the first 100% recyclable wind turbine. Arkema says it is at the heart of this consortium — alongside Canoe, Engie, LM Wind Power, Owens Corning and Suez — and will contribute to the development of environmentally friendly and sustainable solutions for wind power with its high-performance materials.
With its Elium thermoplastic liquid resin and its structural adhesives, Arkema says it offers a breakthrough innovation in the composites market, opening up new perspectives in many sectors, including the production of wind turbine blades. The company notes that Elium resin-based composite parts can be used on the same production lines as those currently used for thermoset resin-based composite parts, have exceptional physical-mechanical properties and are 100% recyclable, making this product key to this project, says Arkema.
Furthermore, the ability to chemically recycle the resin enables it to be used “ad infinitum,” preserving the same properties as a virgin resin, making this technology what Arkema deems as a good fit for the circular economy.
“Recycling end-of-life [EoL] wind turbines is a major industrial and environmental challenge for the wind power industry, due to the considerable volumes involved. Being at the heart of the ZEBRA project, thanks to our expertise and our wide range of polymers for composites, we are contributing to the performance of the wind energy sector by aligning it with an operational circularity approach,” states Guillaume Clédat, Global Sales and Development director for Elium resin.
According to the company, Arkema’s position in this consortium demonstrates the Group’s commitment and its strong will to be part of a product design model with a circular economy approach. Arkema points to its other sustainability initiatives including contributing to the United Nations’ Sustainable Development Goals (SDGs), and more specifically, to SDG 7 which aims to “ensure access to affordable, reliable, sustainable and modern energy for all.”
Related Content
-
Watch: A practical view of sustainability in composites product development
Markus Beer of Forward Engineering addresses definitions of sustainability, how to approach sustainability goals, the role of life cycle analysis (LCA) and social, environmental and governmental driving forces. Watch his “CW Tech Days: Sustainability” presentation.
-
Bioabsorbable and degradable glass fibers, compostable composite parts
ABM Composite offers sustainable options and up to a 60% reduction in carbon footprint for glass fiber-reinforced composites.
-
Plant tour: Arris Composites, Berkeley, Calif., U.S.
The creator of Additive Molding is leveraging automation and thermoplastics to provide high-volume, high-quality, sustainable composites manufacturing services.