MS-21-300 debuts first flight with carbon fiber wing
Certification of the MS-21-300 aircraft is nearing completion, with plans to start delivering it to customers in 2022.
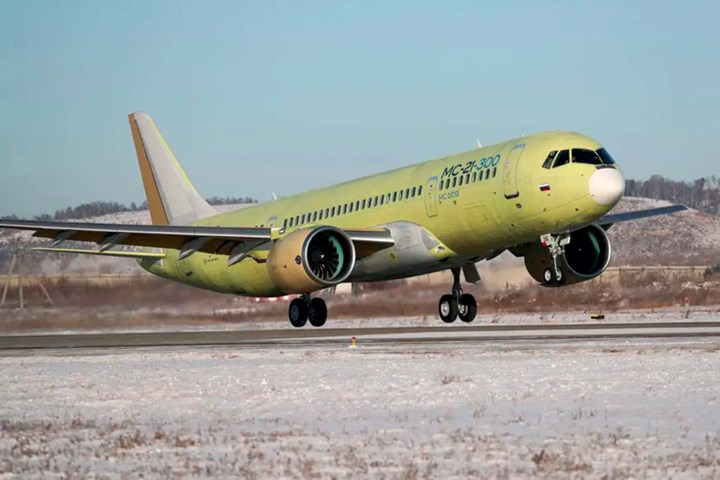
The MS-21-300 aircraft makes its first flight with its new composite infused wing. Photo Credit: UAC
On Dec. 25, ’s (Moscow, Russia) MS-21-300 aircraft, the wing of which is made of Russian-sourced carbon fiber, made its first flight from the airfield of the Irkutsk Aviation Plant.
The aircraft was piloted by a crew consisting of test pilot Roman Taskaev and test pilot Oleg Kononenko. “The flight mission has been completed in full,” says Taskaev. “The aircraft systems were operating normally.”
“In addition to the three aircraft in the final assembly shop, three more MS-21-300 are at different stages of production. All of them will receive a wing made of Russian composites,” notes United Aircraft Corp. (UAC) General Director Yuri Slyusar. “Within the framework of the MS-21 program, a big step has been taken in the development of cooperation between aircraft manufacturing plants in Russia.”
Slyusar says UAC has developed centers of competence within Russia specializing in the production of individual units. Aviastar produces the MS-21 fuselage panels and tail unit, Voronezh VASO the engine pylons and landing gear fairings. AeroComposite-Ulyanovsk manufactures the wing box, wing consoles and the center section of the MS-21-300 aircraft and KAPO-Composite the wing mechanization. Each center is involved in promising projects in the Russian aircraft industry, Slyusar contends.
“The first flight of an aircraft with a wing made of Russian composites proves that we did everything right. The MS-21 program is consistently and steadily moving forward, despite sanctions and unfair competition,” says Denis Manturov, Minister of Industry and Trade of the Russian Federation. “This is the result of the development of the competencies of the aviation industry and related industries and unprecedented government support. The total amount of funds allocated by the Ministry of Industry and Trade of Russia for the creation of domestic materials for the composite wing amounted to 4.4 billion rubles [~$58 million]. The technology introduced for the production of the MS-21 wing has a number of advantages. It, in comparison with traditional autoclave technology, allows you to increase productivity, reduce labor costs and cost and provide the ability to form large parts. To date, a composite wing has been manufactured for two aircraft, [with] the third set [still] being manufactured. We plan to receive changes to the Type Certificate regarding the composite wing in the second half of 2022.”
Domestic materials for the composite wing structures were developed with the participation of scientists from Moscow State University and aviation industry specialists from Rosatom. Qualification tests indicated the materials’ compliance with MS-21 aircraft design requirements. The composite wing was manufacturing using vacuum infusion technologies patented in Russia.
“The share of composites in the MS-21 design is about 40%, which is a record figure for medium-haul aircraft. The use of strong and lightweight composite materials has made it possible to create a wing with unique aerodynamic characteristics unattainable for a metal wing,” says the head of Rostec, Sergey Chemezov. “Improved aerodynamics have made it possible to increase the width of the MS-21 fuselage and expand the cabin, which brings new advantages in terms of passenger comfort. This is the first medium-haul aircraft in the world where such solutions have been applied.”
MS-21-300/310 is a new-generation, medium-range aircraft with a capacity of 163-211 passengers, aiming for the passenger transportation market in Russia and globally. According to Andrey Boginsky, general director of PJSC Irkut Corp., there are plans to start supplying MS-21-300 aircraft to Rossiya Airlines, part of the Aeroflot Group, this year. All production aircraft will be equipped with a composite wing. The aircraft will be delivered in a two-class layout — 16 business class seats and 153 economy class seats.
Related Content
Numerical tool with mean stress correction demonstrated for fatigue life estimation of thermoplastic composites
To aid design of fatigue-resistant structures, Econ Engineering has developed an algorithm to evaluate ply-based cyclic stiffness degradation combined with an FE failure check, validated for a CF/PAEK pressure vessel.
Read MoreCarbon fiber, bionic design achieve peak performance in race-ready production vehicle
Porsche worked with Action Composites to design and manufacture an innovative carbon fiber safety cage option to lightweight one of its series race vehicles, built in a one-shot compression molding process.
Read MoreDamage tolerance testing of sandwich composites: The sandwich CAI test
A new ASTM-standardized test method established in 2022 assesses the compression-loaded damage tolerance of sandwich composites.
Read MoreBladder-assisted compression molding derivative produces complex, autoclave-quality automotive parts
HP Composites’ AirPower technology enables high-rate CFRP roof production with 50% energy savings for the Maserati MC20.
Read MoreRead Next
Plant tour: Daher Shap’in TechCenter and composites production plant, Saint-Aignan-de-Grandlieu, France
Co-located R&D and production advance OOA thermosets, thermoplastics, welding, recycling and digital technologies for faster processing and certification of lighter, more sustainable composites.
Read More“Structured air” TPS safeguards composite structures
Powered by an 85% air/15% pure polyimide aerogel, Blueshift’s novel material system protects structures during transient thermal events from -200°C to beyond 2400°C for rockets, battery boxes and more.
Read MoreVIDEO: High-volume processing for fiberglass components
Cannon Ergos, a company specializing in high-ton presses and equipment for composites fabrication and plastics processing, displayed automotive and industrial components at CAMX 2024.
Read More