Solvay expands Solvalite portfolio into automotive, invest in Xencor LFT production facilities
New fast curing carbon fiber and woven fabric prepregs target high-volume automotive applications such as body panels with optimized structural part performance.
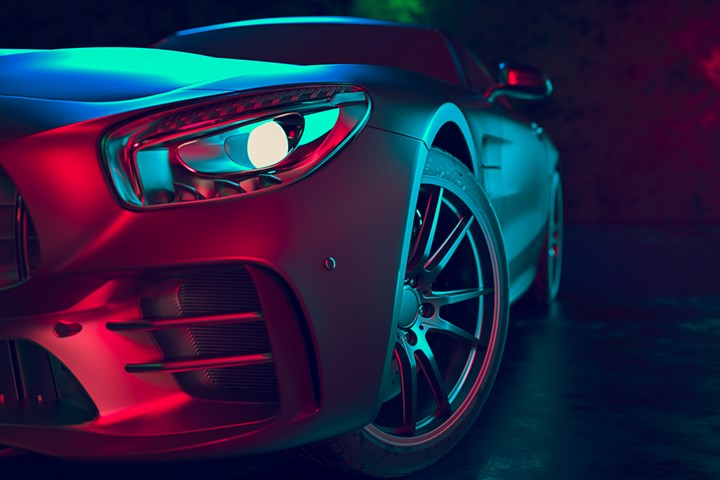
Photo Credit: Solvay
Specialty materials supplier Solvay (Alpharetta, Ga., U.S.) has announced an important addition to complement its broad portfolio of composite materials for the : , said to be a new generation of unidirectional (UD) carbon fiber and woven fabric products pre-impregnated with SolvaLite 714 epoxy resin. Solvay says these prepregs offer fast cure cycles, long outlife and have been optimized for manufacturing automotive components, such as body panels, at short compression molding cycle times in serial production runs.
“Our new SolvaLite 714 prepregs have been specially developed to ensure strong product robustness in large-scale industrial compression molding processes and deliver high structural part performance,” Greg Kelly, product manager prepregs, Solvay Composites, says. “They are available in a wide range of UD carbon fiber reinforced and woven fabric formats.”
SolvaLite 714 prepregs are currently manufactured in Europe, and will be commercially available worldwide beginning in the second quarter of 2022. Solvay will officially launch and introduce the new product family to the automotive market during international composites trade show this week in hall 5, booth M41.
In addition, Solvay recently invested in its production capability enhancements for (long fiber technology). The investment includes new manufacturing assets and additional capabilities in Solvay’s Oudenaarde facility (Belgium) as well as an expansion of research and development (R&D) resources at one of Solvay’s technical centers in Alpharetta, Ga. Xencor LFT is one of the key pillars in Solvay’s lightweighting portfolio, which also includes short-fiber compounds and continuous carbon fiber composites.
According to the company, Xencor LFT opens up new lightweighting potential for aluminum die cast replacement in next-generation electric vehicles (EVs). This includes several areas of metal replacement, such as those in braking and steering, electric drive units, inverters and battery module protection, among others.
Related Content
-
Revisiting the OceanGate Titan disaster
A year has passed since the tragic loss of the Titan submersible that claimed the lives of five people. What lessons have been learned from the disaster?
-
Plant tour: Airbus, Illescas, Spain
Airbus’ Illescas facility, featuring highly automated composites processes for the A350 lower wing cover and one-piece Section 19 fuselage barrels, works toward production ramp-ups and next-generation aircraft.
-
The potential for thermoplastic composite nacelles
Collins Aerospace draws on global team, decades of experience to demonstrate large, curved AFP and welded structures for the next generation of aircraft.