EconCore, ThermHex Waben optimize honeycomb core production
An investment in additional MEAF 75-H34 extruders reduce energy consumption in honeycomb production by up to 65% and double capacity.
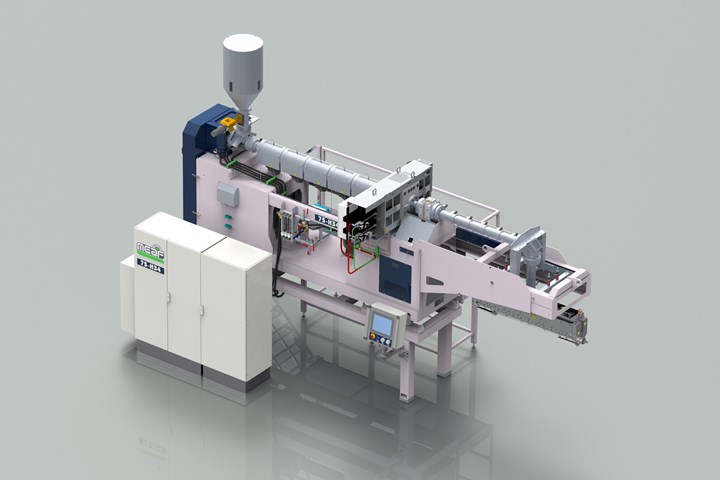
Photo Credit: ThermHex Waben, EconCore
Honeycomb sandwich producer EconCore (Leuven, Belgium) and polypropylene honeycomb core manufacturer ThermHex Waben GmbH (Halle, Germany) have doubled capacity in the production of honeycomb cores, with reduced energy consumption by up to 65% compared to alternative solutions.
The two companies recently installed MEAF (Yerseke, The Netherlands) H-Series extruders within their state-of-the-art production facilities, ThermHex its second one after its first installation in 2015. The new extruder, fitted with special features, can be connected with the first, combining both production streams for the most efficient energy use, the company notes. This has reportedly increased ThermHex’s theoretical capacity in production honeycomb cores from 500 kilograms (approx. 1,100 pounds) to 1,000 kilograms (approx. 2,200 pounds) per hour, which is equivalent to 3,000 tonnes per year in a two-shift production.
MEAF extruders are said to offer significant sheet extrusion line energy efficiency over its competition. In a direct comparison MEAF’s 75-H34 extruder, as used by ThermHex Waben, recorded 0.18-0.22 kilowatts per kilogram, versus a competitor’s 0.50 kilowatts per kilogram. Besides 10-65% less energy of produced kilogram of product required, the MEAF H-series extruders are suitable to extrude multiple materials with same screw and barrel, and reduces polymer degradation due to low friction extruder design as well as minimal flow and pressure fluctuations, even at higher outputs.
ThermHex Waben’s parent company EconCore introduced its first MEAF’s 50-customized 75-H34 extruder for its pilot line in 2017, which features the same screw ratio but a smaller barrel and customized features compared to the ThermHex MEAF lab extruder. In view of more profound industrial scale-up activities for the company’s rPET honeycomb core, EconCore needed an additional larger industrial scale extruder with a compact design. It also needed to efficiently handle RPET flakes and a range of engineered polymers used in the production of RPET and high-performance thermoplastic (HPT) honeycomb cores. The 75-H34 offered this, while also retaining the same screw ratio, barrel and customized features as the previous extruder.
One issue faced by EconCore when searching for the right extruder was their temperature ranges for high-performance polymers like polyethylenimine (PEI). For polypropylene, more conventional extruders typically offer a temperature range of 80-300°C. However, this was too low and MEAF’s extruder was capable of offering a higher temperature range from 200-400°C, fulfilling the requirements to extrude RPET and a certain range of engineered polymers.
“Our relationship with MEAF extends across not only ourselves at EconCore and ThermHex Waben but also our licensees,” Wouter Winant, technical manager at EconCore, says. “Our technologies for automated continuous production of thermoplastic honeycombs are available for licensing. The trust that we have built in MEAF’s extruders over the last couple of years is demonstrated by our willingness to recommend their products to all of our licensees.”
“The demand for more sustainable, lightweight, high-rigidity materials are constantly growing and to cope with the influx of demand it is important for ThermHex Waben to grow our production capabilities,” Dr. Jochen Pflug, CEO of both EconCore and ThermHex Waben, adds. “MEAF’s 75-H34 extruder has allowed us to expand production capacity significantly.”
EconCore were recently nominated for the Belgian Business Awards for the Environment in recognition of its rPET honeycomb technology. In August 2021, Econcore’s rPET honeycomb core technology was also accredited with the Solar impulse Label in recognition of material sustainability. ThermHex Waben recently announced a Top 100 most innovative company in Germany.
Both Econcore and Thermhex Waben will be co-exhibiting at JEC World 2022 in hall 6, booth Q85.
Related Content
Plant tour: Teijin Carbon America Inc., Greenwood, S.C., U.S.
In 2018, Teijin broke ground on a facility that is reportedly the largest capacity carbon fiber line currently in existence. The line has been fully functional for nearly two years and has plenty of room for expansion.
Read MorePlant tour: Airbus, Illescas, Spain
Airbus’ Illescas facility, featuring highly automated composites processes for the A350 lower wing cover and one-piece Section 19 fuselage barrels, works toward production ramp-ups and next-generation aircraft.
Read MoreHybrid process marries continuous, discontinuous composites design
9T Labs and Purdue applied Additive Fusion Technology to engineer a performance- and cost-competitive aircraft bin pin bracket made from compression-molded continuous and discontinuous CFRTP.
Read MoreOtto Aviation launches Phantom 3500 business jet with all-composite airframe from Leonardo
Promising 60% less fuel burn and 90% less emissions using SAF, the super-laminar flow design with windowless fuselage will be built using RTM in Florida facility with certification slated for 2030.
Read MoreRead Next
EconCore, Flaxco reveal flax fiber-reinforced thermoplastic honeycomb panels
Natural fiber sandwich panels are expected to replace those made from glass and carbon fiber, offering enhanced rigidity and sustainability for applications in automotive and sporting good markets.
Read MoreThermHex, Brixtone complete honeycomb core panel production for 400 commercial vans
Cargopan wall panels incorporate ThermHex polypropylene honeycomb core for increased robustness damage resistance, waterproofing and a tripled lifespan.
Read MoreComposites end markets: New space (2025)
Composite materials — with their unmatched strength-to-weight ratio, durability in extreme environments and design versatility — are at the heart of innovations in satellites, propulsion systems and lunar exploration vehicles, propelling the space economy toward a $1.8 trillion future.
Read More