Mini fiber-optic SHM system embedded into composites
Partners in the SMARTFIBER project have demonstrated continued and automatic structural health monitoring.
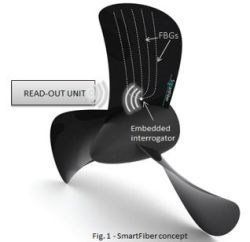
SMARTFIBER concept of SHM system using Fiber Bragg Grating sensors embedded into a composite tidal turbine blade. SOURCE: SMARTFIBER project.
Structural health monitoring (SHM) is an emerging widespread discipline in a variety of structures, including steel and concrete bridges and buildings. In composites, SHM has been pursued for decades with several goals:
-
Prevent failures from overload, manufacturing defect or damage;
-
Reduce the frequency and cost of inspection during service;
-
Provide real-time understanding of the fracture mechanics in composites and validation data for existing finite element models with a view also toward increasingly complex designs.
SMARTFIBER is a 42-month project (Sept 2010 to April 2014) funded by the European Union Seventh Framework Programme with the goal of embedding a miniaturized complete sensor system — including both sensor array and autonomous readout unit, or interrogator — into a composite structure, in this case, a tidal turbine. The seven partners claim they have demonstrated the world’s first miniaturized fiber-optical sensor system than can be fully embedded in a composite material. They assert that this achievement paves the way toward smart composites that enable continued and automatic monitoring of the structural health of composite material in structures such as tidal blades, wind turbine blades, airplane fuselage and wing components or marine structures (masts, antennas, hulls and propellers).
The SMARTFIBER partners include:
- (Leuven, Belgium)
- Ghent University (Gent, Belgium)
- Optocap Ltd (Livingtson, West Lothian, U.K.)
- (Leuven, Belgium)
- (Erlangen, Germany)
- (Geel, Belgium)
- (The Hague, The Netherlands).
As can be seen in Fig. 1 above from the project’s final white paper, the SMARTFIBER approach consists of embedding a system of Fiber Bragg Grating (FBG) sensors and low-cost, miniaturized interrogator into the composite structure, enabling wireless power and two-way communication with an external read-out unit (see Figure 2 below). Automated (vs. manual) placement of the sensors and interrogator unit during structure manufacturing was also demonstrated.
The key to the SMARTFIBER SHM system is a low-cost, miniaturized interrogator for the FBG sensors, embedded into the composite structure and enabling wireless power as well as two-way communication with an external read-out unit. SOURCE: SMARTFIBER
FBG sensors were used due to their ability to provide continuous monitoring coupled with their compactness, lightweight, immunity to electromagnetic interferences (EMI), high resistance to corrosion, high temperature capacity and multiplexing capabilities. The team believed them superior over other strain monitoring techniques (e.g. classical electrical strain gauges) especially when pursuing automated embedding during manufacture.
Silicon photonics technology enabled the high miniaturization and low cost sought for the FBG interrogator. The core of the interrogator is a photonic integrated circuit (PIC) that transmits a signal which, after being processed, is received by the external read-out unit. The latter also supplies wireless power to the interrogator. Another key component of the interrogator is a tailored Array Waveguide Grating (AWG) filter. The SMARTFIBER paper asserts that all of these devices can be manufactured using well-established industrial silicon-based microfabrication techniques and infrastructure.
The sensor system was assembled by Optocap on an electronic board designed by Xenics. The optical subsystem consisted of a silicon photonics integrated circuit developed by IMEC and photodiodes and read-out integrated circuits (ICs) provided by Xenics.
Fraunhofer Institute for Integrated Circuits IIS was responsible for the wireless interface which provides power to the embedded system and at the same time reads out the acquired data at high speed.
After being connected to an optical fiber sensor chain manufactured by FBGS International, the sensor system was cast into an epoxy shape specifically designed by Ghent University to minimize the impact on the composite material. Together with the attached fiber sensor chain, the sensor system was then embedded into the blade of a tidal turbine by Airborne International, which also conducted studies into automation of this process during blade fabrication.
The complete system was integrated within the tidal turbine blade, a sandwich construction with a foam core and non-crimp fabric faceskins. Light resin transfer molding (LRTM) was used to mold the blade. Extra layers of glass fabric were placed to minimize resin build-up around the embedded system and to reduce the abrupt change in stiffness from laminate to embedded elements. The optical fiber was placed along the longitudinal length of the blade in loops from tip to root and held in position by small dots of glue. A strategy for automated placement was also developed.
The embedded system was tested and compared to a commercial interrogator. Its performance was on target with the project goals. “We are investigating steps to be taken towards commercialization of the device,” says project leader Dries Van Thourhout, “Input from potential partners is welcome.”
Related Content
Composites reinvent infrastructure
Celebrating National Composites Week, CW shares ways in which composites continue to evolve the way we approach infrastructure projects.
Read MoreCSub delivers one-piece composite truss bridge in Norway
EPC supplier has fabricated, transported and delivered a 42-meter composite bridge intended for pedestrians and bicyclists.
Read MoreComposites end markets: Infrastructure and construction (2024)
Composites are increasingly used in applications like building facades, bridges, utility poles, wastewater treatment pipes, repair solutions and more.
Read MoreRe-Wind Network completes first U.S. BladeBridge in Georgia
Beaverbrook Park now exhibits a 50-foot pedestrian bridge design consisting of a decommissioned wind blade flanked by two wooden decks.
Read MoreRead Next
“Structured air” TPS safeguards composite structures
Powered by an 85% air/15% pure polyimide aerogel, Blueshift’s novel material system protects structures during transient thermal events from -200°C to beyond 2400°C for rockets, battery boxes and more.
Read MoreAssembling the Multifunctional Fuselage Demonstrator: The final welds
Building the all-thermoplastic composite fuselage demonstrator comes to an end with continuous ultrasonic welding of the RH longitudinal fuselage joint and resistance welding for coupling of the fuselage frames across the upper and lower halves.
Read MoreComposites end markets: New space (2025)
Composite materials — with their unmatched strength-to-weight ratio, durability in extreme environments and design versatility — are at the heart of innovations in satellites, propulsion systems and lunar exploration vehicles, propelling the space economy toward a $1.8 trillion future.
Read More