From most popular articles to most popular news items, the CW editorial team has taken it upon themselves to round up the most popular content items of 2022 for our readers. In this list, we have collected the top ten most-viewed products of 2022, based on Google Analytics.
10. Cygnet Texkimp introduces zero-degree filament winding solution
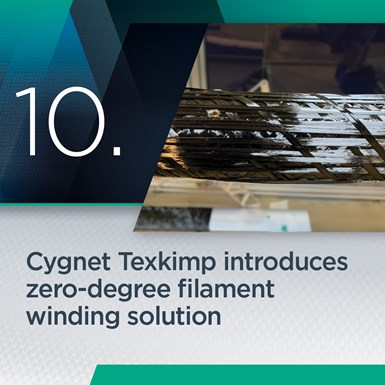
Fiber handling and converting technology company Cygnet Texkimp (Northwich, U.K.) has developed a way of winding composite fibers at a zero-degree angle to create curved and straight structural parts with enhanced mechanical strength using the minimum amount of fiber.
9. Conagen develops high-performing debondable adhesives
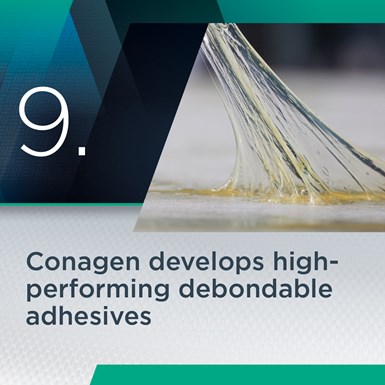
(Bedford, Mass., U.S.), a synthetic biology R&D company, announces the development of patented, debondable hot melt adhesives made by high-performance materials from sustainable and natural bio-molecules.
8. Evident wind blade inspection system automates nondestructive ultrasonic testing
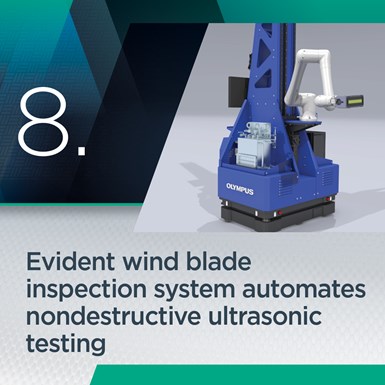
(Tokyo, Japan), a wholly owned subsidiary of Olympus comprising its former Scientific Solutions Division as of , developed its Wind Blade Inspection System (WBIS) using Industry 4.0 technologies to automate and digitize the time-consuming, labor-intensive process of manual nondestructive testing (NDT) for large components like composite wind blades.
7. PRF Composite Materials launches Q.tool prepreg tooling system
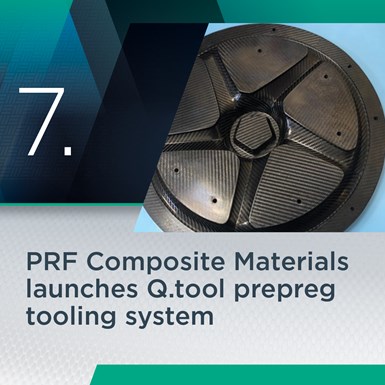
PRF Composite Materials (Poole, Dorset, U.K.) is launching its new prepreg tooling system, Q.tool. Designed, developed and manufactured by PRF, Q.tool is reported to significantly reduces the time and costs of tool manufacture, while also providing an improved surface finish, all with sustainability in mind.
6. Swancor launches recyclable thermosetting epoxy resin

(Nantou, Taiwan) has launched two new products, EzCiclo and CleaVER, to offer a new solution to recycle and reuse wind turbine blades. EzCiclo is a recyclable and reusable thermosetting epoxy resin, which, when used with carbon or glass fiber reinforcement, can be recycled and degraded via the company’s CleaVER technology.
5. Hexcel introduces G-Vent technology for thick, OOA marine structures
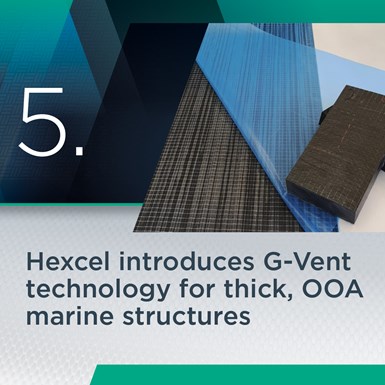
Hexcel Corp. (Stamford, Conn., U.S.) has leveraged its experience in aerospace and wind energy to develop a novel technology for out-of-autoclave (OOA) processing. It is reported to deliver significant reduction in process time and cost for marine manufacturers without compromising mechanical performance.
4. Intelligence-based design, advanced simulation capabilities added to Siemens NX software
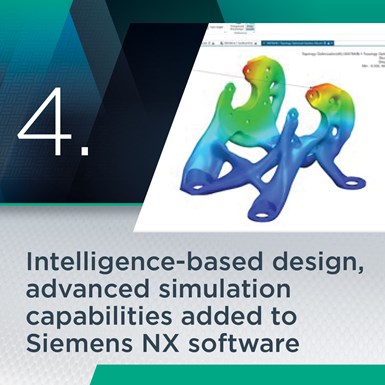
Siemens Digital Industries Software (Plano, Texas, U.S.) has launched the latest release of its CAD/CAM/CAE software, part of the Xcelerator portfolio of software and services. The latest release of NX software adds in advanced technologies, such as artificial intelligence (AI) and advanced simulation capabilities, while continuing to invest in productivity and capability enhancements.
3. Teijin unveils novel spread-tow carbon fiber woven fabric

Teijin (Tokyo, Japan) has launched a lightweight, strong and cost-effective carbon fiber woven fabric developed with the company’s proprietary tow-spreading technology. The new woven fabric is made with 3K (3,000) carbon fiber filament yarn for applications requiring low weight and design flexibility, such as automotive interior materials and sporting goods. Teijin, using its in-house tow-spreading technology, succeeded in thinning the 3K fabric from a molding thickness of 0.2 mm to approximately 0.15 mm, the same as that of 1K woven fabric, when molded into carbon fiber-reinforced plastic (CFRP).
2. Porcher Industries launches new range of flax fiber-based thermoplastic composites for automotive
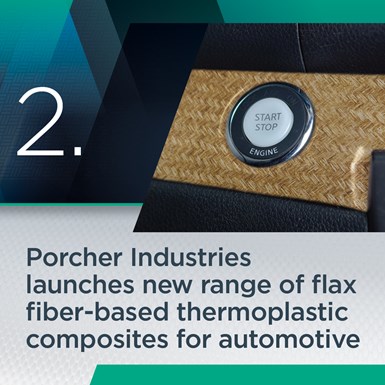
Porcher Industries (Eclose-Badinières, France) has announced the launch of a new range of automotive industry-grade thermoplastic composite stiffeners made primarily of flax fibers grown, selected, mixed and woven in France. These products will be sold as textiles that can be thermocompressed and injection molded. Recyclable PP, and biosourced PLA and PA11 are three available thermoplastic filament options.
1. Patent-pending welder rapidly melts thermoplastics
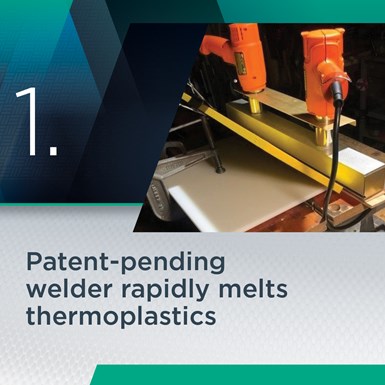
The FlatJet Welder is a patent-pending design that provides rapid surface melt to thermoplastic components, enabling quick, complete welds. Currently this is said to be a limitation to the use of thermoplastic materials, whose optimized mechanical properties but low surface energy precludes adhesive bonding. Current welding is also often limited to small areas and is a slow process.
Related Content
University of Bristol launches composite materials to space for ISS testing
Next-gen carbon fiber materials will be tested under extreme conditions for 12-18 months to determine their viability in space for use in future space bases, interplanetary travel.
Read MoreSchrödinger advances materials informatics for faster development of next-gen composites
Cutting time to market by multiple orders of magnitude, machine learning and physics-based approaches are combined to open new possibilities for innovations in biomaterials, fire-resistant composites, space applications, hydrogen tanks and more.
Read MorePhotothermal tomography for locating, quantifying defects in composites
Years of infrared testing development result in thermography technology that is no longer just qualitative, but can define defect size and depth, making additional UT scans obsolete.
Read MoreEmbraer conducts composite structural wing testing for PDNT
New technologies demonstration platform (PDNT), validating innovative processes, methodologies and new materials, exceeded more than 200% of expected progressive load limit.
Read MoreRead Next
Top 10 ÂÌñÏ×ÆÞ news items of 2022
The year 2022 was a big year for composites. Take a look at ÂÌñÏ×ÆÞ’s top 10 most popular news pieces based on Google Analytics and check out what you might have missed.
Read MoreFrom plant tours to EV battery enclosures: The top 10 ÂÌñÏ×ÆÞ articles of 2022
Through a variety of editorial content, CW explored the trends and topics that are rapidly flourishing in the industry. Based on Google Analytics, these top 10 articles were considered the most popular.
Read MorePlant tour: Daher Shap’in TechCenter and composites production plant, Saint-Aignan-de-Grandlieu, France
Co-located R&D and production advance OOA thermosets, thermoplastics, welding, recycling and digital technologies for faster processing and certification of lighter, more sustainable composites.
Read More