Evident wind blade inspection system automates nondestructive ultrasonic testing
An autonomous, cobot-mounted inspection system combines Industry 4.0 with established ultrasonic technology to rapidly provide repeatable, accurate data and improve overall efficiency.
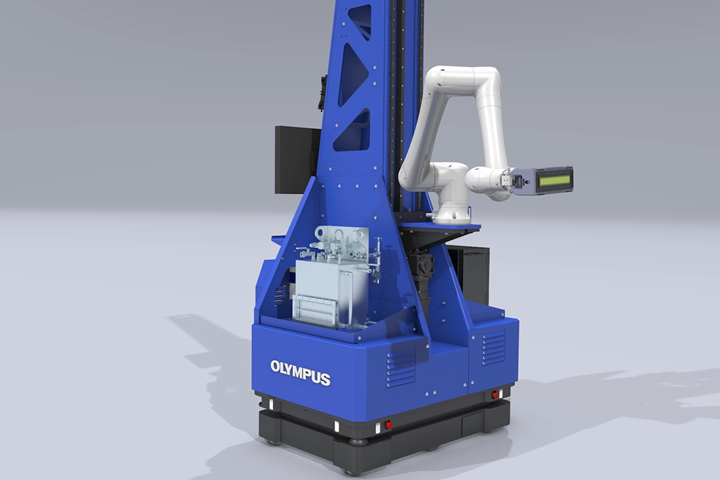
Photo Credit: Evident
(Tokyo, Japan), a wholly owned subsidiary of Olympus comprising its former Scientific Solutions Division as of , developed its Wind Blade Inspection System (WBIS) using Industry 4.0 technologies to automate and digitize the time-consuming, labor-intensive process of manual nondestructive testing (NDT) for large components like composite wind blades.
The concept for the technology originated as a development led by Vestas (Aarhus, Denmark) with partners Evident, Eckhart Automation (Lansing, Mich., U.S.) and In-Position Technologies (Chandler, Ariz., U.S.). The system was developed over a two-year collaboration involving shared investments between Vestas’ Wind Systems Manufacturing Automation division and Evident’s Systems & Integration division. The concept was ultimately transferred entirely to Evident for commercialization of the complete solution. Vestas owns the original system and multiple additional series systems.
The integrity of a wind blade is highly dependent on the quality of the adhesive bonding between its shear webs and spar caps, Evident says. As the shear web and the spar cap are bonded together by a layer of adhesive of varying thickness, there are two interfaces that must be examined: (1) between the spar cap and the adhesive and (2) between the adhesive and the shear web. The areas to be inspected represent several dozens of square meters that require a fast and reliable inspection solution.
In Evident’s WBIS, a collaborative robot (cobot) is mounted on an autonomous guided vehicle (AGV). The system’s global architecture allows each component to communicate with each other, synchronizing and driving the AGV, the cobot, a vertical axis to move the cobot up and down, a water system (for UT probe couplant) and a phased array ultrasonic acquisition unit for the completion of fully automated and autonomous inspection of the blade.
The AGV can map the workshop where the blade is inspected, enabling it to learn its working environment and move autonomously within it. At least two physical targets are used to define the start and end positions of the inspection, one at the root and one at the tip of the blade. The targets have a specific V shape to allow the AGV to accurately and repeatedly dock with it.
Once the operator launches the inspection sequence, the system moves from its parking position to the starting target, autonomously defining the best path to reach it based on the map and taking into account unexpected obstacles. Normally, the AGV uses the shortest path to go to the defined target, but if something is blocking this path the AGV will try to go around. If that’s not possible, it will define a new path using the learned map.
Once docked to the target, the system aligns itself to the blade span using the cobot arm to sense the blade surface and calculate the correct angle to get the AGV aligned with the blade. Then the AGV and cobot arm coordinate their movements to perform a raster scan of the region of interest, typically the lower and upper spar caps and webs of the blade. The cobot arm’s six joints provide precise positioning of the UT phased array probe on the surface and help ensure the constant pressure required for high-resolution, high-quality C-scan inspection data.
While each region of interest is being scanned, the system uses real-time positioning information from the cobot to guide the AGV. Based on the extension of the cobot arm, the system can sense which direction the AGV should move and then correct its trajectory to follow the blade curvature along the span. This allows the system to move parallel to the complex shape of the blade without the need to teach the system by, for example, programming it with a CAD drawing of the blade. These features enable the system to be self-adapting and self-learning, eliminating the need for time-consuming programming.
The system also simultaneously manages safety during the inspection sequence thanks to a series of programmable cameras located on the AGV. It is also cloud-enabled, enabling users to upload and store data for analysis, and is said to be easily adaptable to other large components.
Related Content
Robotic NDT inspection solutions, services enhance multitasking capabilities
CAMX 2024: Matec Instrument Companies Inc. presents its range of nondestructive ultrasonic testing technologies, including robotic inspection systems for increased efficiency and reduced physical strain.
Read MoreAutomated robotic NDT enhances capabilities for composites
Kineco Kaman Composites India uses a bespoke Fill Accubot ultrasonic testing system to boost inspection efficiency and productivity.
Read MoreShearography equipment well suited to composites NDT
CAMX 2025: Laser Technology Inc. features analysis tools like the LTI-2100 and LTI 5200, which are optimal for detecting subsurface composite flaws.
Read MoreInnovation in ultrasonic inspection and nondestructive testing
With increasingly complex structural components working their way into aerospace programs, the need for versatility in inspection and testing capabilities is growing.
Read MoreRead Next
Plant tour: Daher Shap’in TechCenter and composites production plant, Saint-Aignan-de-Grandlieu, France
Co-located R&D and production advance OOA thermosets, thermoplastics, welding, recycling and digital technologies for faster processing and certification of lighter, more sustainable composites.
Read MoreAssembling the Multifunctional Fuselage Demonstrator: The final welds
Building the all-thermoplastic composite fuselage demonstrator comes to an end with continuous ultrasonic welding of the RH longitudinal fuselage joint and resistance welding for coupling of the fuselage frames across the upper and lower halves.
Read More“Structured air” TPS safeguards composite structures
Powered by an 85% air/15% pure polyimide aerogel, Blueshift’s novel material system protects structures during transient thermal events from -200°C to beyond 2400°C for rockets, battery boxes and more.
Read More