Thermwood adds angle layer printing feature to LSAM large-scale AM systems
The ability to print at a 45º angle adds to the system’s current horizontal and vertical orientation capabilities, enhancing the flexibility of producing large-scale composite thermoplastic parts.
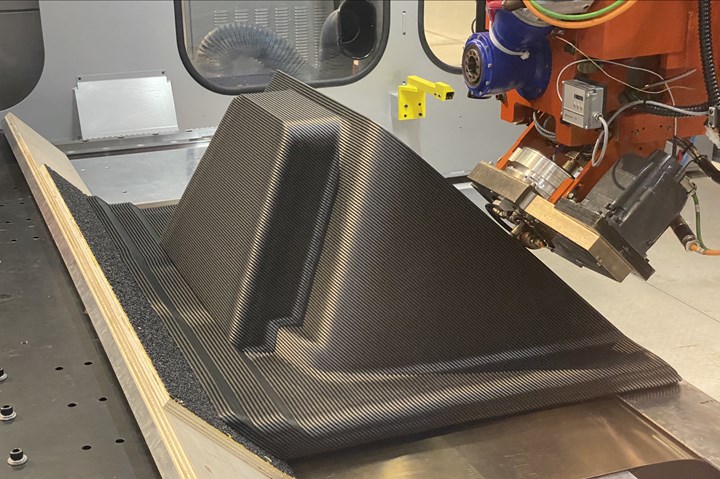
Photo Credit: Thermwood Corp.
Thermwood Corp. (Dale, Ind., U.S.) has added a third print orientation to its LSAM large-scale additive manufacturing systems. LSAM systems can currently print both horizontal and vertical layers if equipped with the vertical layer print (VLP) option, available on most Thermwood LSAM machines. This new addition adds angle layer printing (ALP), the ability to print at a 45º angle, to the VLP option, enabling maximum print flexibility.
All print orientations use the complete LSAM print head including exclusive LSAM print features such as the patented, temperature-controlled compression wheel and thermal sensor layer automation. The latter automatically helps maintain an even layer temperature throughout the print for complete and precise layer fusion.
While most existing systems are already equipped with VLP, Thermwood has replaced this capability with a VLP/ALP option on new machines which offers both vertical and angle layer print capability, in addition to the standard horizontal layer print. Machines operating in the field that already have VLP can have ALP added. Alternately, if a machine was purchased without VLP, Thermwood says the entire new VLP/ALP print option can be added to most machines already in operation.
Thermwood’s LSAM large-scale additive systems are claimed to be the most widely used large-scale composite thermoplastic additive equipment in industrial production today. Processing a variety of reinforced composite polymers from room temperature ABS and PC to high-temperature material such as PSU, PESU and PEI, they are used to produce molds and tools for the aerospace industry, patterns for the foundry industry and for a variety of other applications.
LSAM systems are available in sizes from 5' x 10' to 15' x 60' in a variety of configurations including print-only and full print and trim. Print heads are available that can print thermoplastic composite material at rates from 200 Ibs/hour to more than 500 Ibs/hour (see “Thermwood expands LSAM product line availability”).
Related Content
-
Thermoplastic composites: Cracking the horizontal body panel nut
Versatile sandwich panel technology solves decades-long exterior automotive challenge.
-
Assembling the Multifunctional Fuselage Demonstrator: The final welds
Building the all-thermoplastic composite fuselage demonstrator comes to an end with continuous ultrasonic welding of the RH longitudinal fuselage joint and resistance welding for coupling of the fuselage frames across the upper and lower halves.
-
“Structured air” TPS safeguards composite structures
Powered by an 85% air/15% pure polyimide aerogel, Blueshift’s novel material system protects structures during transient thermal events from -200°C to beyond 2400°C for rockets, battery boxes and more.