France Relance award granted to Omega Systèmes for automated composite slitting solutions
Central to the OMEGA-WEB 2022 will be inline automated inspection, and large-scale production of composite parts via AFP, ATL to accelerate the aerospace sector.
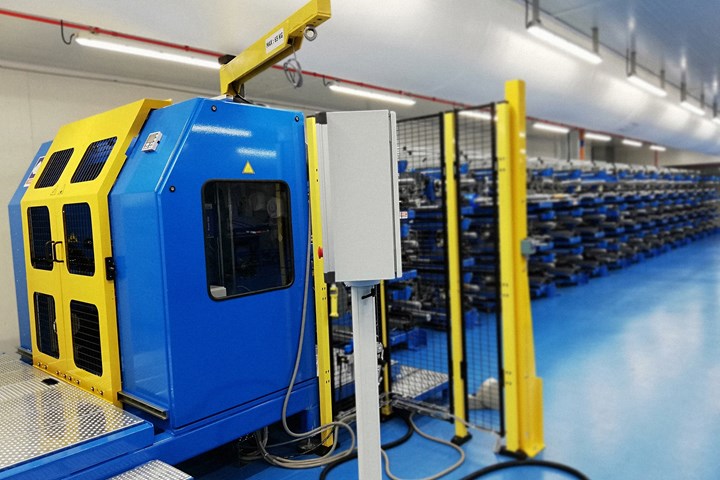
High-performance cutting system increases Omega Systèmes’ productivity by a factor of five for the supply of precision slit tape delivered in spooled form. Photo Credit: Omega Systèmes
Omega Systèmes, a Web Industries company (Marlborough, Mass., U.S. and Saint-Philbert-de-Grand-Lieu, France), reported on March 10 that it has been awarded a grant by the France Relance [Recovery] plan — a roadmap to mobilize and recover the country economically, socially and ecologically — for the design and development of aeronautic thermoset and thermoplastic slitting solutions. Funds from the grant will reportedly modernize and automate Omega Systèmes’ equipment at its Nantes plant, which will supply next-generation aircraft manufacturers and contribute to the industry's economic rebound from the consequences of the COVID-19 crisis.
Under the grant’s project, OMEGA-WEB 2022, Omega Systèmes says it will design and develop innovative solutions for slitting thermoplastics and thermoset composite materials in France. Central to the project will be inline automated inspection to support French and European R&D projects and the large-scale production of composite parts by automated fiber placement (AFP) and automated tape laying (ATL). The company adds that it will deliver higher value-added products to the market that meet the requirements of future aerospace programs.
According to Omega Systèmes’ General Manager Jim Sharkey, France Relance awarded the grant based largely on Omega’s strategic value chain expertise. “We can accelerate the time to market from material selection and management to the cutting, packaging and delivery of materials,” Sharkey says. “Plus, Web can deliver scale to its aerospace customers, and at a reduced cost, to accelerate composites materials’ speed to market.”
Omega Systèmes has manufacturing locations in Nantes and Bordeaux, the heart of France’s aircraft manufacturing region, and is supported by Web Industries in Stade, Germany, and its six North American plants. Further, Nantes is home to Omega Systèmes’ European Center of Excellence for Composite Development & Commercialization. It provides the European market with access to technical teams, material quality control and pilot lines for demonstration, rapid development, testing and qualification of composite material formats.
“We supply Tier 1 and Tier 2 aerospace equipment manufacturers,” Sharkey notes. “Having unique capabilities in France and Europe, and with a Center of Excellence for thermoplastic and thermosetting composites, allows us to offer the market increased production capacity and supply for new aircraft programs designed with primary and secondary composite structures. We will help OEMs reduce aircraft weight, improve their carbon footprint and offer price-competitive products. Our high-performance cutting capabilities, for example, increase productivity by a factor of five for the supply of precision slit tape delivered in spooled form.”
According to France Relance documentation, its funding is aimed at “accelerating the diversification, modernization and ecological transformation of the aeronautics… [sector].” Investment support and assistance for the aeronautics sector was announced on Sept. 3, 2020, by Bruno Le Maire, minister of Economics, Finance and Recovery.
“France Relance lists innovation and modernization as two primary goals,” Sharkey reports. “With our state-of-the-art solutions for the slitting of thermoplastic and thermosetting composite materials, Omega Systèmes is uniquely equipped to support France’s aeronautics sector in achieving these critical goals.”
Omega Systèmes is currently addressing three composite slitting objectives as specified by the grant:
- Optimizing the slitting of thermoplastics by creating new formats and parameters, and specifying exclusive blades system with improved cutting capabilities.
- Developing a new composites splicing system and test bench.
- Developing slit-width monitoring and foreign object debris (FOD) detection systems.
Related Content
Broetje-Automation demonstrates rCF placement via AFP
Through the ScrapSeRO project, the system integrator and machine builder successfully processed recycled composites, in addition to more traditional materials, via its highly flexible Staxx One system.
Read MoreAES explores robot vs. gantry for large-format additive manufacturing
Additive Engineering Solutions, specialist at 3D printing very large parts and tools on gantry machines, now also uses a robot for large-format AM. Here is how the robot compares.
Read MoreTAVieDA project team cuts aircraft door production time using thermoplastic composites, welding
Fraunhofer groups, Trelleborg and Airbus develop modular, fully automated assembly system concept to replace metals and time-consuming assembly that shows potential for scalability.
Read MoreJEC World 2025 highlights: Trends in aerospace, new space and defense
CW editor-in-chief Scott Francis discusses trends in aerospace on display at JEC World — as the composites industry awaits a new single aisle aircraft program, the industry puts continued focus on new space, defense, UAM.
Read MoreRead Next
Omega Systèmes extends contract with Airbus
The three-year contract covers the manufacture, supply and processing of high-precision composites for several Airbus programs.
Read MoreAssembling the Multifunctional Fuselage Demonstrator: The final welds
Building the all-thermoplastic composite fuselage demonstrator comes to an end with continuous ultrasonic welding of the RH longitudinal fuselage joint and resistance welding for coupling of the fuselage frames across the upper and lower halves.
Read MoreComposites end markets: New space (2025)
Composite materials — with their unmatched strength-to-weight ratio, durability in extreme environments and design versatility — are at the heart of innovations in satellites, propulsion systems and lunar exploration vehicles, propelling the space economy toward a $1.8 trillion future.
Read More