FAURECIA to supply hydrogen storage systems for 1,600 Hyundai heavy-duty trucks
Delivery of 10,000 composite tanks proves industrialization strategy of 20% lower weight, 50% lower cost components

Faurecia (Nanterre, France) was recently awarded a significant contract for fuel cell electric vehicle storage systems from Hyundai Motor Company (Seoul, South Korea). Faurecia will supply the entire hydrogen storage system, which will result in delivery of 10,000 composite hydrogen tanks. These will be produced in its global center of expertise dedicated to hydrogen storage systems in Bavans, France.
Faurecia deliveries will begin in 2021, and over a four-year period, will equip roughly 1,600 Hyundai heavy duty trucks that will be delivered to Hyundai Hydrogen Mobility (Zurich, Switzerland), a newly created joint venture between Hyundai and H2 Energy to spearhead hydrogen mobility in Europe.
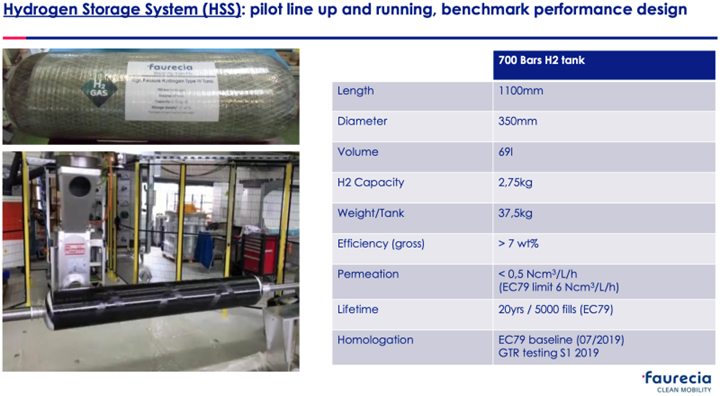
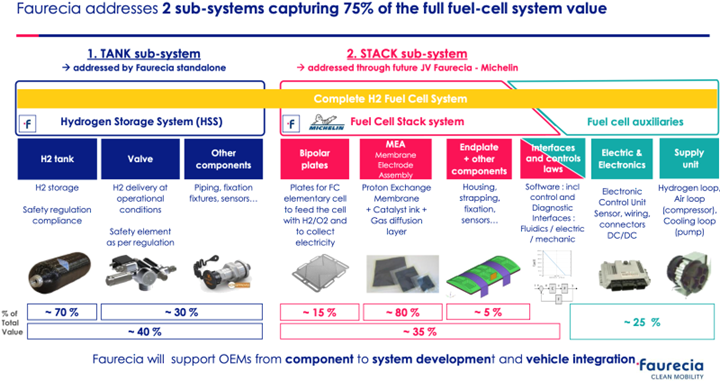
Source | , June 2019
“Fuel cell electric vehicle technology will become significant in the powertrain mix in the next ten to fifteen years, in particular for commercial vehicles,” says Faurecia CEO Patrick Koller. “Faurecia is investing significant resources in optimizing the potential of this technology and creating the best-in class ecosystem to accelerate its deployment. This award, along with the joint venture we have created with Michelin to offer a unique range of hydrogen fuel cell systems, is a major step in our commitment to become the leader in fuel cell systems.”
Lighter, less-costly composite tanks
Faurecia announced in 2017 that it had acquired an exclusive access to the intellectual property and process know-how of composite hydrogen tanks from STELIA Aerospace Composites (Toulouse, France). With this support, Faurecia has been able to design, industrialize and commercialize high pressure hydrogen tanks made of carbon fiber composites for fuel cell electric vehicles (FCEVs).
According to a March 2018 press release by STELIA Aerospace Composites, it has specifically helped Faurecia develop a lightweight and cost-effective 700 bar hydrogen storage tank. In the video below, Nils Walther, global program manager for Faurecia’s zero-emissions fuel cell division, shows this tank as well as Faurecia’s 350 bar composite tank at CES 2020 (Consumer Electronics Show, Las Vegas, Nev., U.S). He explains that pilot lines in France are already in production and notes Faurecia’s pride in achieving 15-20% weight reduction, which allows it to use less carbon fiber, for less raw material cost, plus less filament winding time, while providing more interior volume for higher driving range.
These weight and cost achievements are fulfilling the strategy explained by Faurecia chief technical officer Christophe Aufrère:
“We want to accelerate the development of hydrogen through different ways. The first one is massive investment of 15-20 million euros in R&D and pilot lines. The second one is that we want to halve the price of the main components and we are providing 80% of the value chain. The third one is, of course, we want to also massive deploy this technology in terms of industrialization.”
Global center of excellence
In June 2019, Faurecia announced the creation of a global center of expertise for hydrogen storage systems at its R&D center in Bavans, France. The center, scheduled to start operations in the second-quarter 2020, represents a total investment of approximatively €25 million. Faurecia plans to add 50 jobs to the nearly 750 employees at the site, which is dedicated to Faurecia’s Clean Mobility activity.
Fuel-cell electric vehicles offer an attractive and complementary alternative to battery-electric vehicles. The range and refueling time of fuel-cell trucks should be equivalent to diesel ones while being completely emissions-free. By 2030, it is estimated that at least 2 million new vehicles, and more than 350,000 commercial vehicles, will be equipped with fuel cell technology, according to Faurecia.
Related Content
Plant tour: Hexagon Purus, Kassel, Germany
Fully automated, Industry 4.0 line for hydrogen pressure vessels advances efficiency and versatility in small footprint for next-gen, sustainable composites production.
Read MoreHigh-tension, vertical filament winding enables affordable flywheel energy storage system
French startup Energiestro’s prototype solar energy flywheel-based storage system aims to reduce costs with glass fiber composites and prestressed concrete.
Read MoreComposites end markets: Batteries and fuel cells (2024)
As the number of battery and fuel cell electric vehicles (EVs) grows, so do the opportunities for composites in battery enclosures and components for fuel cells.
Read MoreRTM, dry braided fabric enable faster, cost-effective manufacture for hydrokinetic turbine components
Switching from prepreg to RTM led to significant time and cost savings for the manufacture of fiberglass struts and complex carbon fiber composite foils that power ORPC’s RivGen systems.
Read MoreRead Next
Assembling the Multifunctional Fuselage Demonstrator: The final welds
Building the all-thermoplastic composite fuselage demonstrator comes to an end with continuous ultrasonic welding of the RH longitudinal fuselage joint and resistance welding for coupling of the fuselage frames across the upper and lower halves.
Read MoreAll-recycled, needle-punched nonwoven CFRP slashes carbon footprint of Formula 2 seat
Dallara and Tenowo collaborate to produce a race-ready Formula 2 seat using recycled carbon fiber, reducing CO2 emissions by 97.5% compared to virgin materials.
Read More“Structured air” TPS safeguards composite structures
Powered by an 85% air/15% pure polyimide aerogel, Blueshift’s novel material system protects structures during transient thermal events from -200°C to beyond 2400°C for rockets, battery boxes and more.
Read More