Composite 3D printing allows damage detection in aerospace and construction
Using Anisoprint 3D printers, a materials research center in the Netherlands has developed 3D-printed composite parts with self-sensing functionality.
Brightlands Materials Center (Geleen, Netherlands) has developed 3D-printed composite parts with self-sensing functionality. Self-sensing creates opportunities to monitor critical structures in fields such as aerospace, construction and healthcare.
What is self-sensing?
Self-sensing is the ability of a material to act as a sensor and collect information about its own condition. Carbon fiber-reinforced polymer-matrix composites are already established as providing self-sensing capabilities based on measurable changes in the electrical resistance of the continuous fibers. Such materials are being developed and demonstrated for structural health monitoring (SHM) in aircraft and construction applications including bridges and buildings.
Traditionally, such self-sensing composite materials have been manufactured using techniques that involve multiple stages, more complex operations and special equipment. Brightlands Materials Center is combining the self-sensing of continuous carbon fiber with fabrication using additive manufacturing to make SHM applications more cost-effective, enabling wider use and expansion to new applications.
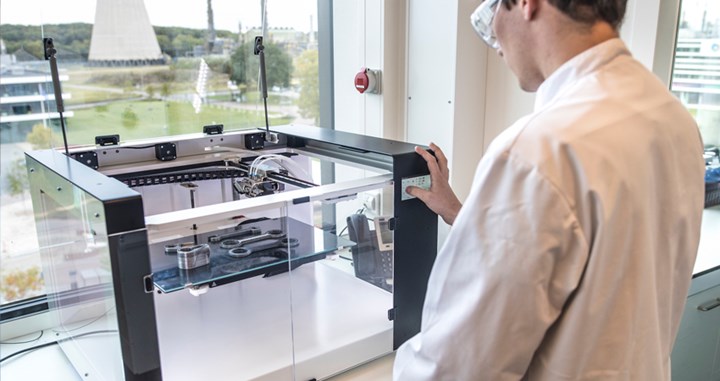
Brightlands Materials Center uses an Anisoprint Composer A3 composite 3D printer to fabricate self-sensing parts for its additive manufacturing and structural health monitoring and structural sensing research. Source | Brightlands Materials Center
Continuous fiber 3D printing opens new horizons
Additive manufacturing enables very precise positioning and orientation of continuous carbon fibers. Thus, it is possible to place the fibers at chosen locations inside the product to provide the required strength and stiffness along specified load paths, and forming an integral part of the structure. This means that the carbon fibers are located where they are needed to act as “sensors” for monitoring the structure and multiple fibers can form a range of sensors throughout the part.
Brightlands Materials Center has demonstrated this concept by monitoring deformation in a scale model of a pedestrian composite bridge and in a simple bending beam. Both were printed with the Anisoprint (Esch-sur-Alzette, Luxembourg) Composer A4 composite 3D printer. “We are particularly happy with our new Anisoprint systems, because they offer such a high freedom in the choice of printing materials as well as the complete control of fiber deposition,” says Guy Bex, research engineer at Brightlands Materials Center. Freedom in fiber positioning is also crucial for sensing because the continuous carbon fibers must protrude from the part to make connections to the electronic hardware used for monitoring.
More precise 3D printing results
Because 3D printing does not require tools or molds, it offers a one-step process to produce continuous fiber-reinforced composites of any shape, replacing traditional multi-step techniques which are more complex, time-consuming and expensive. However, optimizing the manufacturing process for 3D printed structures may require several iterations. 3D printed composites that are self-sensing can collect information about their real use circumstances, important for the design and prototype phase of new products.
During such testing, the self-sensing 3D printed part registers the real conditions and forces experienced in service, which gives designers and engineers a more precise understanding of the actual requirements printed parts must withstand.
Such sensing may also enable parts to act as a diagnosis tool. For example, 3D printed self-sensing orthosis or prosthesis parts might guide patients and provide valuable information to doctors regarding stress distribution and movement patterns.
Research partners
Brightlands Materials Center is an independent research center founded by the Netherlands Organisation for applied scientific research TNO (The Hague) and the province of Limburg. It supports innovation in industry with a strong application focus and offers dedicated contract research and participation, including a research roadmap on 3D printed self-sensing composites.
Anisoprint is an inventor of anisoprinting — the technology for design and production of optimal composite structures through continuous fiber 3D deposition. The company manufactures 3D printers, materials (based on carbon and basalt fibers) and software for producing anisoprinted composite parts to help scientists solve research problems in new, more effective ways and to enable manufacturing companies to reduce their costs.
Related Content
Revisiting the OceanGate Titan disaster
A year has passed since the tragic loss of the Titan submersible that claimed the lives of five people. What lessons have been learned from the disaster?
Read MoreCarbon fiber, bionic design achieve peak performance in race-ready production vehicle
Porsche worked with Action Composites to design and manufacture an innovative carbon fiber safety cage option to lightweight one of its series race vehicles, built in a one-shot compression molding process.
Read MorePlant tour: Airbus, Illescas, Spain
Airbus’ Illescas facility, featuring highly automated composites processes for the A350 lower wing cover and one-piece Section 19 fuselage barrels, works toward production ramp-ups and next-generation aircraft.
Read MoreInfinite Composites: Type V tanks for space, hydrogen, automotive and more
After a decade of proving its linerless, weight-saving composite tanks with NASA and more than 30 aerospace companies, this CryoSphere pioneer is scaling for growth in commercial space and sustainable transportation on Earth.
Read MoreRead Next
Plant tour: Daher Shap’in TechCenter and composites production plant, Saint-Aignan-de-Grandlieu, France
Co-located R&D and production advance OOA thermosets, thermoplastics, welding, recycling and digital technologies for faster processing and certification of lighter, more sustainable composites.
Read More“Structured air” TPS safeguards composite structures
Powered by an 85% air/15% pure polyimide aerogel, Blueshift’s novel material system protects structures during transient thermal events from -200°C to beyond 2400°C for rockets, battery boxes and more.
Read MoreVIDEO: High-volume processing for fiberglass components
Cannon Ergos, a company specializing in high-ton presses and equipment for composites fabrication and plastics processing, displayed automotive and industrial components at CAMX 2024.
Read More