Anisoprint, Polymaker collaborate to enable flexibility in composite 3D printing
The combination of Anisoprint’s 3D printing systems and Polymaker’s plastics offers a range of mechanical and chemical properties for composite part production.

Anisoprint (Esch-sur-Alzette, Luxembourg) and Polymaker (Shanghai, China) have announced a collaboration to provide composite 3D printing solutions that combine the properties and benefits of Anisoprint’s 3D printing systems and Polymaker’s materials.
Anisoprint’s Composite Fiber Co-extrusion (CFC) CFC technology reinforces plastics — enabling processing temperatures up to 270&»å±ð²µ;С — with continuous composite fibers directly during the printing process. Polymaker produces plastics for 3D printing, including PETG, ABS, PC, PLA and PA, covering a range of possible properties such as heat, chemical, weather and impact resistance. Polymaker designs these materials specifically for 3D printing so they are easy to work with and print with reliable results.
The companies say that the combination of Anisoprint’s CFC technology with Polymaker materials enables users to achieve a composite part that is lightweight with high strength and tailored to specific industrial applications.
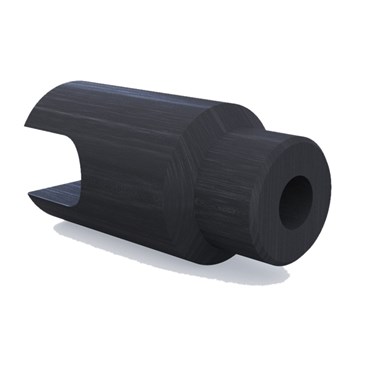
This part for a dairy bottle production line was produced on an Anisoprint 3D printer from carbon fiber-reinforced plastic. Source | Anisoprint
A recent example of the combination of Anisoprint printing and Polymaker materials in use was the creation of an additively manufactured, carbon fiber-reinforced PETG plastic clevis for use in a yogurt bottle production line, which is used to catch the bottles after production to move them through an area where they are washed with hydrogen peroxide. The companies say the combination of Polymaker’s hydrogen peroxide-resistant PETG plastic, Anisoprint’s Composer 3D printer, and carbon fiber reinforcement for toughness and rigidity boosted the lifespan of the part and reduced production time in the facility.
Learn more about Anisoprint’s continuous fiber composite 3D printing process in CW’s blog “Advancing additive manufacturing to exploit anisotropy.”
Related Content
-
Al Seer Marine, Abu Dhabi Maritime unveil world’s largest 3D-printed boat
Holding the new Guinness World Record at 11.98 meters, the 3D-printed composite water taxi used a CEAD Flexbot to print two hulls in less than 12 days.
-
Urban furniture project demonstrates green potential for composite 3D printing and recycled materials
Large-format AM specialist Caracol and partners designed custom, 3D-printed outdoor furniture with glass fiber-reinforced recycled polypropylene, and conducted an LCA to evaluate and improve the process.
-
The next evolution in AFP
Automated fiber placement develops into more compact, flexible, modular and digitized systems with multi-material and process capabilities.