Schunk Carbon Technology to 3D-print tooling using Anisoprint technology
The carbon fiber and ceramic solutions developer has adopted Anisoprint’s Composer printer and materials to accelerate its custom tooling operations.
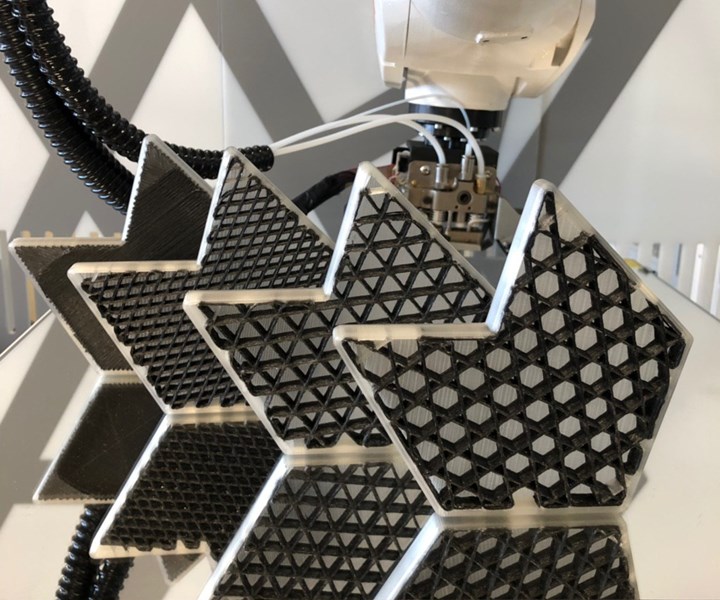
Source | Anisoprint LLC
Schunk Carbon Technology (Menomonee Falls, Wis., U.S.), a division of the Schunk Group involved in the development, manufacture and application of carbon and ceramic solutions, has announced that it applying 3D printers and materials from Anisoprint (Esch-sur-Alzette, Luxembourg) to accelerate its custom tools production.
“We are using the Anisoprint Composer for printing demonstrators and tools for our production. The Composer does a good job! It works precisely and reliably, and together with its slicing software ‘Aura,’ it forms a capable tool,” says Gotthard Nauditt, R&D engineer for composites.
Schunk Group produces construction components from carbon/graphite, carbon compounds, silicon carbide and quartz for high-temperature applications, automotive and small motor technology. Anisoprint offers hardware solutions for the manufacturing of end-use parts based on its patented composite fiber co-extrusion (CFC) technology. It enables customization of materials properties by controlling the direction and volume fraction of the reinforcing fibers. Parts printed with its technology are reportedly stronger, lighter and cheaper than metal or non-optimized fiber-reinforced composites.
Related Content
-
Sulapac introduces Sulapac Flow 1.7 to replace PLA, ABS and PP in FDM, FGF
Available as filament and granules for extrusion, new wood composite matches properties yet is compostable, eliminates microplastics and reduces carbon footprint.
-
Combining multifunctional thermoplastic composites, additive manufacturing for next-gen airframe structures
The DOMMINIO project combines AFP with 3D printed gyroid cores, embedded SHM sensors and smart materials for induction-driven disassembly of parts at end of life.
-
Hybrid process marries continuous, discontinuous composites design
9T Labs and Purdue applied Additive Fusion Technology to engineer a performance- and cost-competitive aircraft bin pin bracket made from compression-molded continuous and discontinuous CFRTP.