Trelleborg unveils high-temperature castable epoxy tooling material
Low-density TC350 epoxy board supports the creation of tooling in a range of sizes and complexities for carbon fiber, PP and GFRP parts.
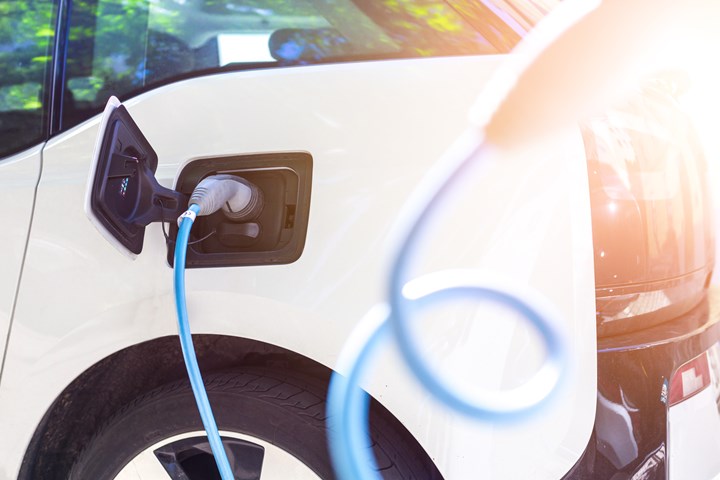
Trelleborg’s (Rochdale, U.K.) applied technologies operation unveils its new TC350 castable epoxy tooling solution. This material is engineered to be dimensionally stable in an autoclave up to +180ºC for repeated direct-to-part manufacturing.
TC350 is a specialized high-temperature, low-density syntactic epoxy tooling board, supporting the creation of parts for use in a range of industries, such as aerospace, automotive and marine. The tooling board is compatible with carbon fiber, polypropylene (PP) and glass fiber-reinforced plastics (GFRP) used in the manufacturing of electric vehicles (EVs).
Kerry Lyons, Trelleborg business development manager notes that users can create multiple finished parts directly from TC350, removing the requirement for costly carbon fiber prepregs and improving operational efficiencies. Further, TC350, available as a castable or board solution, is said to enable the development of tooling in a range of sizes and design complexity without the need for machining, reducing excess material wastage. TC350 is available globally.
As part of its value-added services, Trelleborg says it can also provide cast tools from 3D CAD drawings, for customers that do not have access to CNC machines or with limited capacity.
Related Content
-
CirculinQ: Glass fiber, recycled plastic turn paving into climate solutions
Durable, modular paving system from recycled composite filters, collects, infiltrates stormwater to reduce flooding and recharge local aquifers.
-
Plant tour: Collins Aerospace, Riverside, Calif., U.S. and Almere, Netherlands
Composite Tier 1’s long history, acquisition of stamped parts pioneer Dutch Thermoplastic Components, advances roadmap for growth in thermoplastic composite parts.
-
Plant tour: Teijin Carbon America Inc., Greenwood, S.C., U.S.
In 2018, Teijin broke ground on a facility that is reportedly the largest capacity carbon fiber line currently in existence. The line has been fully functional for nearly two years and has plenty of room for expansion.