Plataine's new Practicum-Optimum AI algorithm optimizes production scheduling
Self-learning algorithm achieves reportedly unprecedented levels of optimized KPIs and schedule practicalization.
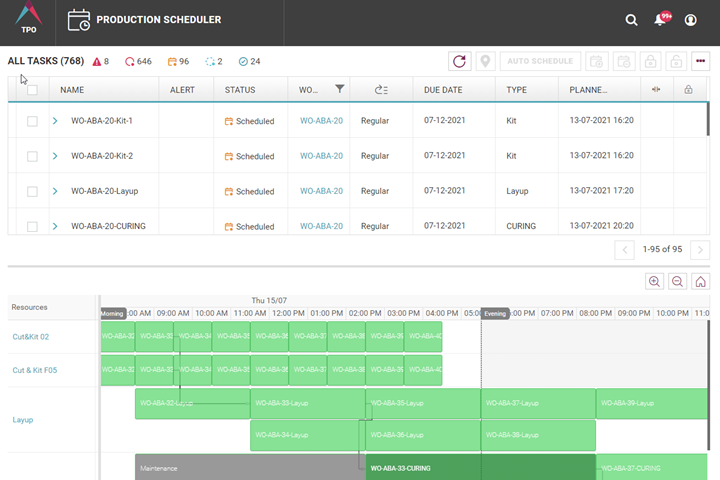
Photo Credit: Plataine
Plataine (Waltham, Mass., U.S.), a leading provider of Industrial IoT (IIoT) and AI-based software for manufacturing optimization, has released its new Practimum-Optimum, said to be a breakthrough AI algorithm for optimizing manufacturing planning and scheduling by combining unprecedented levels of optimized KPIs (key performance indicators) with a practical, robust planning application. Plataine’s Production Scheduler is part of Plataine’s TPO (Total Production Optimization), cloud-based suite of interconnected applications, which integrate production scheduling with shop-floor operations management, while optimizing all production resources such as materials, equipment and tools.
Most existing software solutions for scheduling use a search algorithm to optimize top level KPI goals of the overall schedule such as due-date compliance, production throughput or machine utilization. However, once such a schedule is generated, the planner is often required to make countless changes to address specific customer priorities, executability considerations or other practical matters. These are often not fully addressed by the software. These changes would make perfect business sense even if they led to lower KPI scores but require constant human involvement in the process. Plataine’s patent-pending Practimum-Optimum algorithm drives the production scheduler to build optimal schedules that already integrate practical considerations and support the user in further integrating subjective judgment changes.
With its built-in machine learning algorithms, the Practimum-Optimum Scheduler teaches itself deep insights in the schedules’ universe including the trade-offs between competing goals, clusters of similar schedules, patterns of demand sets and best attainable values for each individual KPI score. Historical schedules are not mandatory, though they are very useful when available. These insights are used by the Practimum-Optimum algorithm to produce schedules that are both optimal and practical to execute. Production planners can set target values for any mix of business goals such as on-time delivery, overall equipment efficiency (OEE) or make-span, and the Practimum-Optimum Scheduler algorithm will produce the best practical schedule that is the closest to these targets, including a visual interactive Gantt chart and graphic indicators.
Plataine’s intelligent Digital Assistants accompany users throughout schedule execution, alerting them to deviations in the planned schedule — such as a task that is taking longer than planned — and offering recommendations and insights before a crisis occurs. Over time, as the algorithm is being used and real-life schedules are generated, the learning algorithm adapts its planning capabilities and improves its performance.
Related Content
-
ST Engineering MRAS presents initiatives to drive autoclave efficiency, automation
During a JEC World 2024 panel discussion, the company revealed ways in which it is maximizing throughput and efficiency of its autoclaves and enhancing composites production processes.
-
Plant tour: Sekisui Aerospace, Orange City, Iowa, Renton and Sumner, Wash., U.S.
Veteran composites sites use kaizen and innovation culture to expand thermoplastic serial production, 4.0 digitization and new technology for diversified new markets.
-
Modular, robotic cells enable high-rate RTM using any material format
Airborne’s automated ply placement systems at Airbus, GKN Aerospace and Teijin Automotive Technologies aim to maximize flexibility and intelligent automation.