Park Aerospace adds RadarWave RW-HS-300 prepreg to lineup for radome systems
The prepreg fabric’s purpose is to optimize the design, structural integrity and manufacturability of challenging radome structures.
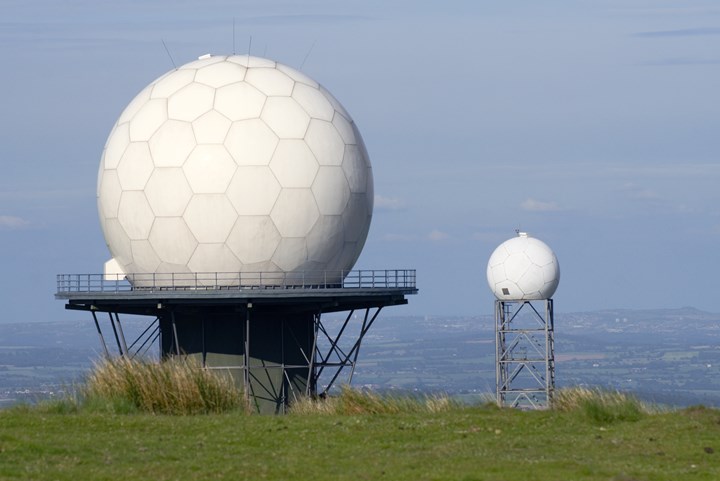
Radome structures used to protect a radar antenna. Photo Credit: Getty Images
Park Aerospace Corp. (Newton, Kan., U.S.) announces the addition of its novel RadarWave RW-HS-300 product to the company’s RadarWave product line. Originally introduced in Oct. 2018, RadarWave is a family of prepreg materials used to manufacture advanced radome systems principally for aerospace and defense applications. Park’s says these materials provide cost-effective alternatives to the esoteric and higher cost materials traditionally used to manufacture these systems.
RadarWave RW-HS-300 uses an innovative type of 300 gsm 8HS fabric and is intended to provide engineers with additional tools for the purpose of optimizing the design, structural integrity and manufacturability of advanced radome systems. In addition to exhibiting transmissivity properties, RadarWave RW-HS-300 provides optimized layup flexibility and enhanced drapability properties for challenging radome structure contours.
Radomes are structural enclosures which protect RF/microwave and other antennas that transmit and receive electromagnetic signals from air-, space-, marine- and ground-based platforms. Park Aerospace says they are constructed with composite materials designed and engineered to optimize dielectric performance and minimize electromagnetic signal transmission loss while protecting the antenna and maintaining the structural integrity of the radome assembly.
Related Content
-
Automated robotic NDT enhances capabilities for composites
Kineco Kaman Composites India uses a bespoke Fill Accubot ultrasonic testing system to boost inspection efficiency and productivity.
-
Plant tour: Aernnova Composites, Toledo and Illescas, Spain
RTM and ATL/AFP high-rate production sites feature this composites and engineering leader’s continued push for excellence and innovation for future airframes.
-
Plant tour: Collins Aerospace, Riverside, Calif., U.S. and Almere, Netherlands
Composite Tier 1’s long history, acquisition of stamped parts pioneer Dutch Thermoplastic Components, advances roadmap for growth in thermoplastic composite parts.