Keyland Polymer, polySpectra combine photopolymers, powder coatings to advance 3D printing
UVMax powder coatings provide a spectrum of surface color and texture possibilities, while COR Alpha photopolymers have been refined for durability.
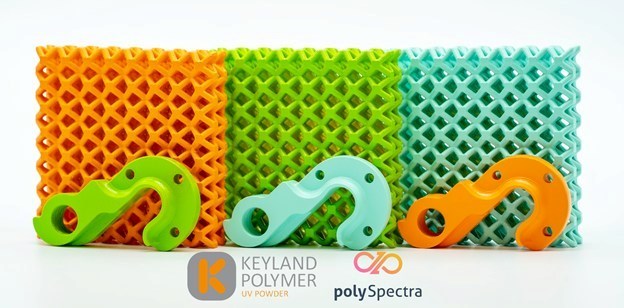
COR Alpha 3D-printed parts using UVMax powder coatings. Photo Credit: Keyland Polymers, polySpectra
Keyland Polymer (Cleveland, Ohio, U.S.) and (Berkeley, Calif., U.S.), a producer of functional photopolymer resins for additive manufacturing (AM), have formed a strategic partnership to provide UVMax powder coatings — targeted at a composites fabrication environment — to COR Alpha 3D-printed parts. COR Alpha is a photopolymer that is rugged under pressure and stands up to solvents. This collaboration is said to unlock a new modular approach to AM, enabling the direct digital fabrication of end-use polymer components for a wide variety of applications.
According to both companies, the surface color and texture of the UVMax coating can be tailored to make COR Alpha 3D-printed parts indistinguishable from traditionally manufactured polymer products. engineering-grade photopolymers have been refined to offer best-in-class thermomechanical performance and durability, whether for consumer products, to medical devices to satellite parts. COR Alpha’s high thermal stability of COR Alpha also enables thorough and complete coating without the concern of warping or degrading the material.
Alternately, coating provides a spectrum of color possibilities, providing an excellent finish for lightweighting applications, transportation, building materials, consumer and industrial products. Keyland says it can develop a wide range of powders to match any supplied color standard. UV powder is an environmentally friendly coating, containing no solvents, VOCs or HAPs. It is safe to use and can be reclaimed and recycled.
Related Content
-
Orbital Composites wins AFWERX award for Starfighter drone fleet
Under the TACFI contract, Orbital is implementing the AMCM process to build 3D printed composite multi-mission UAS aircraft, surpassing $10 million in government awards.
-
Reinforcing hollow, 3D printed parts with continuous fiber composites
Spanish startup Reinforce3D’s continuous fiber injection process (CFIP) involves injection of fibers and liquid resin into hollow parts made from any material. Potential applications include sporting goods, aerospace and automotive components, and more.
-
Plant tour: Airtech International, Springfield, Tenn., U.S.
Fifty years of supplying materials for composites manufacturing includes custom fabrication and now aims to advance 3D-printed tooling, parts and new resins.