Engel launches forming and functionalization of organic sheets
Production cell demonstrates the forming and functionalization of organic sheets and unidirectional tapes in one injection molding step.
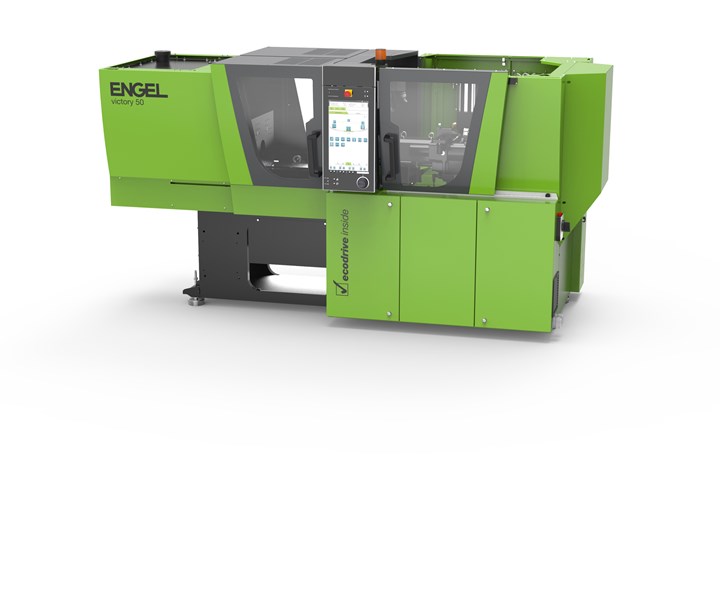
Engel victory injection molding machine. Source | Engel
Editor’s note: ÂÌñÏ×ÆÞ received several new product and technology announcements ahead of JEC World 2020, which had been scheduled for March 3-5. Although that exhibition was postponed to May, CW is now publishing the announcements we received. This is one of them.
Engel (Schwertberg, Austria) is demonstrating the forming and functionalization of organic sheets and unidirectional tapes in one injection molding step. The main component of the production cell, which is producing demonstration components made of continuous fiber-reinforced polyamide (PA), is a tiebarless Engel victory 200/50 injection molding machine equipped with an Engel viper 12 linear robot for handling preforms and finished parts, and a double-sided, vertical Engel IR oven.
The composite blanks are heated in the IR oven, placed in the mold, formed in the mold, and overmolded with PA. Heating the prepregs is one of the process steps that drive the cycle time and quality in the processing of fiber-reinforced preforms with a thermoplastic matrix. The thickness defines the heat-up and cool-down time. Heating the material quickly without damaging it is important, as are short paths for transporting the heated preforms to the mold (hot handling). Engel offers IR ovens from in-house development and production in various designs – both horizontal and vertical – and places them in the production cell in the immediate vicinity of the mold. The ovens and the robots are fully integrated with the machine’s CC300 control unit and can be centrally controlled via the machine’s display.
Engel says the victory machine's biggest advantage in this application is its very fast hot handling. Barrier-free access to the mold area makes it possible to position the IR oven even closer to the mold than is possible for injection molding machines with tiebars. In this way, even very thin preforms can be processed without them cooling too much during transport between the IR oven and the mold.
The thermoplastic composite preforms that Engel is processing live at the show are prepared in the Engel Center for Lightweight Composite Technologies in Austria. In practice, the production of thermoplastic composite blanks can be placed immediately upstream of the manufacturing process and directly next to the processing machine. Engel offers fully integrated systems solutions from a single source, including the processing machine, robots and IR ovens as well as pick-and-place tape stacking units with optical image processing and consolidation units.
Composite parts created using the Engel organomelt process combine light weight with excellent crash safety capabilities. This technology, which is already in series production in the automotive industry, is suitable for organic sheets and unidirectional (UD) glass and/or carbon fiber-reinforced tapes with a thermoplastic matrix. Engel says using a purely thermoplastic material base enables particularly efficient and fully automated manufacturing processes, because reinforcement ribs or assembly elements, for example, can be injected directly after forming in the same process step. At the same time, the organomelt process makes a contribution towards sustainability. "The consistent thermoplastic approach is the precondition for developing recycling strategies for composite parts," says Christian Wolfsberger, Business Development Manager Composite Technologies at ENGEL's headquarters in Schwertberg, Austria. "Tapes make it possible to reinforce individual areas in the part in order to adapt them even more specifically to the load," Wolfsberger continues. "In the future, we will be able to combine organic sheets of different thicknesses, and also organic sheets and tapes, in order to leverage the potential for lightweight design in an even better way."
Related Content
Fraunhofer IGCV develops helicopter door shell using SMV composite
SMC-replacement material subjected to vario-thermal pressing cycle achieved a 1.2-millimeter-thick, complex-shaped door shell, demonstrating feasibility for future aerospace components.
Read MoreKraussMaffei and partners develop sustainable, safe and stylish children’s bike
The Lion Bike is a German-made, injection molded bicycle with 40% recycled carbon fibers with zero scrap and enabling 67% lower CO2 emissions during production.
Read MoreBraided thermoplastic composite H2 tanks with co-consolidated molded boss areas to fit EV battery space
BRYSON project demonstrates possible designs, automated manufacturing and low permeability concepts, including EVOH liner and novel PPA matrix.
Read MoreReinforce 3D forms alliance with 3D printing company Spring Srl
Integration of CFIP technology with additive manufacturing will facilitate optimized composites manufacturing and build up CFIP’s scale.
Read MoreRead Next
Composites end markets: New space (2025)
Composite materials — with their unmatched strength-to-weight ratio, durability in extreme environments and design versatility — are at the heart of innovations in satellites, propulsion systems and lunar exploration vehicles, propelling the space economy toward a $1.8 trillion future.
Read MorePlant tour: Daher Shap’in TechCenter and composites production plant, Saint-Aignan-de-Grandlieu, France
Co-located R&D and production advance OOA thermosets, thermoplastics, welding, recycling and digital technologies for faster processing and certification of lighter, more sustainable composites.
Read More“Structured air” TPS safeguards composite structures
Powered by an 85% air/15% pure polyimide aerogel, Blueshift’s novel material system protects structures during transient thermal events from -200°C to beyond 2400°C for rockets, battery boxes and more.
Read More