Harper International expands product offering with lab-scale rotary furnace
The furnace delivers temperature uniformity for batch or continuous processing of advanced materials at at operating temperatures up to 1,200°C.
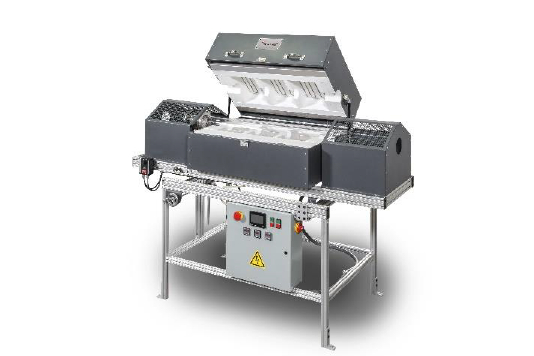
Photo Credit: Harper International
Harper International (Buffalo, N.Y., U.S.) a company offering thermal processing solutions for advanced materials, announces the launch of its . The lab-scale rotary furnace enables those who develop and manufacture advanced materials to optimize their process parameters on a small scale to ensure capability and quality requirements are achieved prior to investment in production-scale thermal process equipment.
Full featured with short delivery times, the lab-scale rotary furnace reportedly provides clients with the opportunity to get to market faster and more efficiently. The furnace delivers temperature uniformity for batch or continuous processing of advanced materials including granular, powder or particulate aggregates at operating temperatures up to 1,200°C (2,192ºF). Harper also offers add-on options for controlled atmospheres and material handling.
In addition, Harper applies this furnace to the Ignite program at its Technology Research Center. Ignite allows clients to run feasibility demonstrations and experimental campaigns while leveraging Harper’s expertise in process development and process optimization.
Related Content
-
Carbon fiber, bionic design achieve peak performance in race-ready production vehicle
Porsche worked with Action Composites to design and manufacture an innovative carbon fiber safety cage option to lightweight one of its series race vehicles, built in a one-shot compression molding process.
-
Bladder-assisted compression molding derivative produces complex, autoclave-quality automotive parts
HP Composites’ AirPower technology enables high-rate CFRP roof production with 50% energy savings for the Maserati MC20.
-
Active core molding: A new way to make composite parts
Koridion expandable material is combined with induction-heated molds to make high-quality, complex-shaped parts in minutes with 40% less material and 90% less energy, unlocking new possibilities in design and production.