AON3D debuts AON M2+ printer to fabricate high performance end-use parts
Printer aimed to exceed aluminum parts using chopped carbon fiber and high-performance polymers (e.g., PEEK, PEKK, ULTEM) via widely available, off-the-shelf filaments.
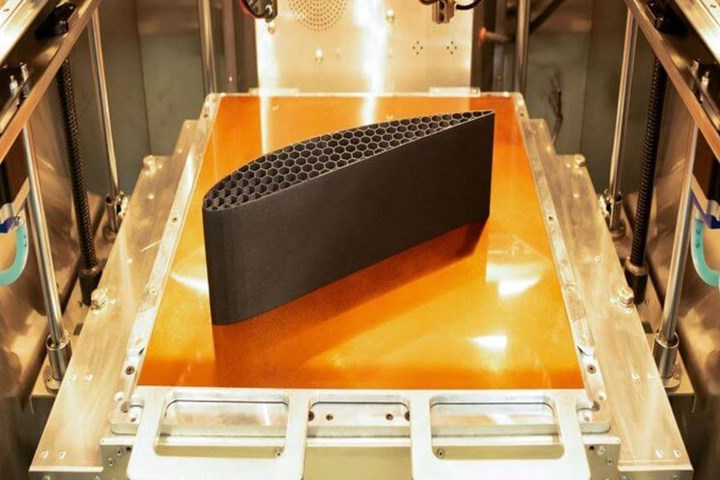
AON-M2 build chamber with chopped carbon fiber/PEEK part made with Solvay KetaSpire AM filament CF10 LS1. Photo Credit: AON3D
AON3D (Montreal, Canada) has announced its new AON M2+ high-temperature industrial 3D printer. Featuring what it claims is the industry’s largest sub-$100,000 actively heated build volume and open material ecosystem, AON3D aims to make full-scale and functional 3D printing accessible to businesses of all sizes. According to AON3D CEO Kevin Han, the AON M2+ was designed by the company’s team of material scientists to take full advantage of current and future economical thermoplastics, carbon fiber composites, and high-performance polymers like PEEK, PEKK and ULTEM.
AON3D explains it manufactures 3D printers to counter the limited build volume, high price and/or lack of material options that exemplify most industrial 3D printer configurations. The AON M2+ reportedly offers high-end features and advanced material capabilities to the mid-market customer without sacrificing hardware quality. Dual independent extruders (500°C), a large, actively heated build chamber (450 x 450 x 640 mm), configurable process parameters and ungated access to thousands of material options are said to provide unlimited end-use printing opportunities. The AON M2+ can print materials that possess a higher strength-to-weight ratio than aluminum, as well as chemical/hydrocarbon resistance, biocompatible/sterilizable properties, thermal resistance above 250°C and more.
Related Content
-
Multi-material, self-sensing, 3D-printed scoliosis braces
Startup Fited and Brightlands Materials Center have developed a lighter weight, thinner CFRP corrective brace, including pressure sensors made from continuous carbon fibers.
-
Large-format AM speeds plug production for manufacture of composite boat molds
Hungarian manufacturer Rapid Prototyping transitioned its conventional foam milling process to 3D printing to produce faster, higher quality, recyclable foam plugs and composite boat molds.
-
The next evolution in AFP
Automated fiber placement develops into more compact, flexible, modular and digitized systems with multi-material and process capabilities.