VETERIA21 project seeks to optimize thermoplastics for adoption in EV battery casings
Aimplas and the Valencian Regional Government’s Ministry of Innovation, Universities, Science will develop more efficient transformation processes for thermoplastics, and reduce battery weight, energy consumption.
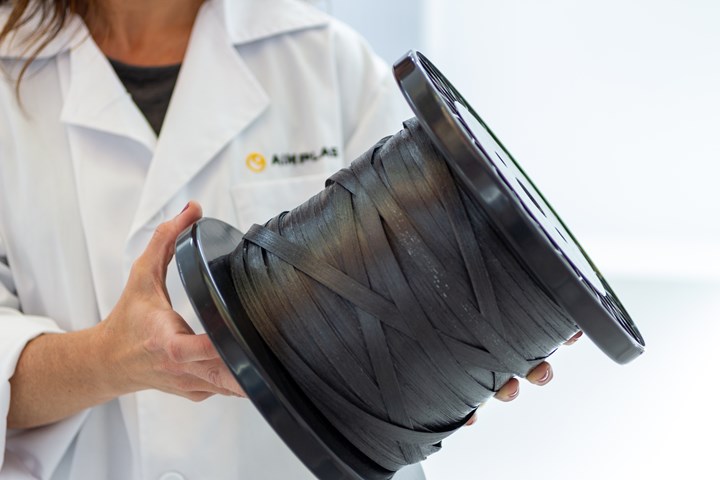
Photo Credit: Aimplas
It was announced on Jan. 3 that the VETERIA21 project, funded by the Valencian Regional Government’s Ministry of Innovation, Universities, Science and implemented by , the Plastics Technology Centre (Valencia, Spain), will develop new, more efficient transformation processes for thermoplastic composites in order to improve their properties so they can replace metals in electric vehicle (EV) battery casings. The project identifies the government’s goal to carry out innovation projects in 2021 in collaboration with companies within the framework of smart specialization.
The results of this project, says Aimplas, will reduce battery weight and, therefore, battery consumption while providing a sustainable solution based on circular economy criteria, such as recyclability. Currently made of stainless steel and aluminum, lithium-ion battery modules account for 20-30% of vehicle weight.
“In general, 73% of vehicle weight corresponds to the metal components. Thermoset composites are therefore a lightweight alternative for battery casings. However, their recyclability and production rate work against them. For this reason, thermoplastic composites represent a good alternative,” explains Begoña Galindo, Aimplas Sustainable and Future Mobility Group Leader.
Thermoplastic composites have also become a trend in vehicle weight reduction for several reasons other than their reduced weight including mechanical resistance, adaptability to different manufacturing processes, short manufacturing cycles, the ability to be combined with other materials, weldability, easy recyclability and adaptability to the circular economy.
Related Content
-
Thermoplastic composites: Cracking the horizontal body panel nut
Versatile sandwich panel technology solves decades-long exterior automotive challenge.
-
Plant tour: Daher Shap’in TechCenter and composites production plant, Saint-Aignan-de-Grandlieu, France
Co-located R&D and production advance OOA thermosets, thermoplastics, welding, recycling and digital technologies for faster processing and certification of lighter, more sustainable composites.
-
Plant tour: Collins Aerospace, Riverside, Calif., U.S. and Almere, Netherlands
Composite Tier 1’s long history, acquisition of stamped parts pioneer Dutch Thermoplastic Components, advances roadmap for growth in thermoplastic composite parts.