The T.33 Spider: Another carbon fiber masterpiece from Gordon Murray
The legendary performance designer-engineer believes in purity of execution, and the T.33 Spider shows that the approach still drives him.
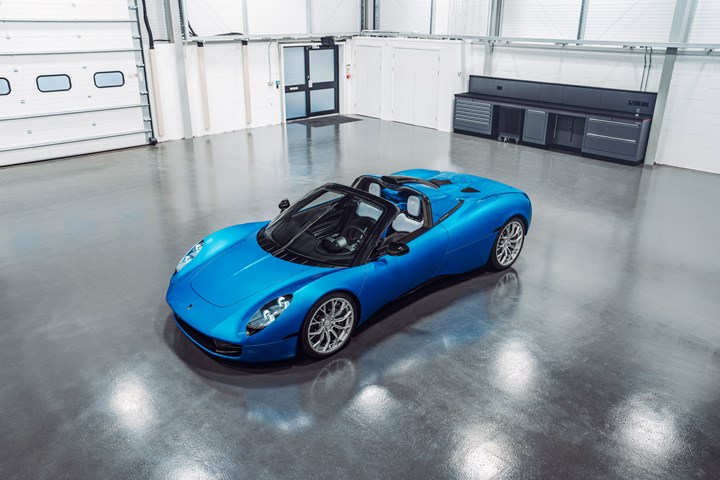
The composite-intensive, V12-powered Gordon Murray Automotive T.33 Spider. One hundred will be hand-built. Photo Credit, all images:
Gordon Murray, who has been involved in the design and engineering of some of the highest-performance cars in the world for the track and the motorway (he was, after all, awarded a CBE by Elizabeth II, so “road” or “expressway” just doesn’t work), operates with seven principles:
- Premium brand: hand-built British cars that are characterized by innovation and quality
- Beautiful and purposeful: Timeless balanced design; every part has a purpose
- Engineering art: Each component is both functional and a work of art
- Driving perfection: Assuring the experience behind the wheel is as good as it can be from the gauges to the throttle response
- Lightweight: Designing with minimal mass in mind helps deliver superior dynamics
- Exclusivity: Only 100 of any model or variant will be built
- Customer journey: The purchaser of any Gordon Murray Automotive vehicle will have complete involvement in the experience
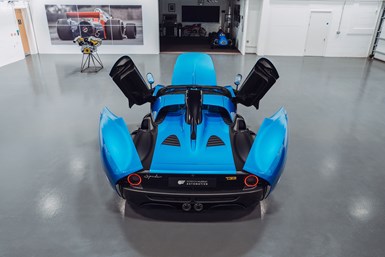
The two removable roof panels are stored in the front 115-liter compartment (a.k.a., “frunk”), then there are two additional 90-liter storage compartments on either side of the T.33, under the rear composite fenders.
Earlier versions of those seven principles included
- Sustainable mobility
- Disruptive technologies
- Low energy solutions
Which undoubtedly had to give way, in part, when the subject is a vehicle that costs $2.35-million or more.*
A car like the just-revealed T.33 Spider. Which ticks the first seven boxes. It will be hand-built at the new Murray Highams Park facility in Windlesham, U.K., later this year so that each vehicle will be hand-tailored to customer requirements.
The vehicle has a dry weight (i.e., no fluids are in the vehicle) of 1,108 kilograms (2,437.6 pounds), so it is comparatively light.
The Structure
Like the T.33 coupe, the Spider has a carbon fiber composite monocoque construction. Carbon fiber composite panels are adhesively bonded to extruded aluminum tubing, with the tubing fitted to precision die-cast aluminum nodes.
Composites are also used in the interior: the leather wrapped steering wheel is produced with carbon fiber, as are the seat structures. The attention to weight reduction results in a vehicle with a dry weight of 1,108 kilograms (2,437.6 pounds).
Unlike the T.33 the Spider has removal carbon fiber composite roof panels that can be fitted in the 115-liter front luggage compartment when not in use. (Yes, there is what is now referred to as a “frunk” because the 608-hp 3.9-liter Cosworth GMA.2 V12 engine is located behind the cabin. The powertrain, incidentally, is a semi-structural component, with the rear suspension attached directly to the aluminum transmission case (the transmission is a six-speed manual).)
Although the T.33 Spider resembles the T.33 coupe, all surfaces behind the A-pillars are different on the two cars.
One of the issues of a spider (or a more ordinary convertible) is torsional rigidity. Once the roof panels are removed and the backlight lowered, the torsional rigidity could be reduced — but Gordon Murray said that the monocoque structure that is used provides exceptional stiffness in the rocker sections on either side of the vehicle, therefore removing any compromises.
In addition to which, spiders tend to be heavier — by even a couple hundred pounds — than their coupe variants mainly because of the need to provide additional components for enhancing stiffness. The T.33 Spider is just 18 kilograms (39.6 pounds) heavier than the coupe.
Which certainly ticks the “Lightweight” box.
* Supercars aren’t particularly examples of sustainability; the extensive use of carbon fiber construction for consumer cars is somewhat disruptive, but as Murray’s car company has been around since 2017, it isn’t particularly novel; and although mass reduction is a focus, one wouldn’t call a car powered by a V12 “low energy.”
Related Content
Revisiting the OceanGate Titan disaster
A year has passed since the tragic loss of the Titan submersible that claimed the lives of five people. What lessons have been learned from the disaster?
Read MoreHybrid process marries continuous, discontinuous composites design
9T Labs and Purdue applied Additive Fusion Technology to engineer a performance- and cost-competitive aircraft bin pin bracket made from compression-molded continuous and discontinuous CFRTP.
Read MoreFilament winding increases access to high-performance composite prostheses
Steptics industrializes production of CFRP prostheses, enabling hundreds of parts/day and 50% lower cost.
Read MoreLow-cost, efficient CFRP anisogrid lattice structures
CIRA uses patented parallel winding, dry fiber, silicone tooling and resin infusion to cut labor for lightweight, heavily loaded space applications.
Read MoreRead Next
Plant tour: Daher Shap’in TechCenter and composites production plant, Saint-Aignan-de-Grandlieu, France
Co-located R&D and production advance OOA thermosets, thermoplastics, welding, recycling and digital technologies for faster processing and certification of lighter, more sustainable composites.
Read MoreComposites end markets: New space (2025)
Composite materials — with their unmatched strength-to-weight ratio, durability in extreme environments and design versatility — are at the heart of innovations in satellites, propulsion systems and lunar exploration vehicles, propelling the space economy toward a $1.8 trillion future.
Read MoreVIDEO: High-volume processing for fiberglass components
Cannon Ergos, a company specializing in high-ton presses and equipment for composites fabrication and plastics processing, displayed automotive and industrial components at CAMX 2024.
Read More