Swissplast Group to produce large-scale 3D-printed components via hybrid LFAM machine
Developed between CMS Advanced Materials Technology and the Fraunhofer Institute, the additive technology produces thermoplastic granulates reinforced with carbon or glass fiber.
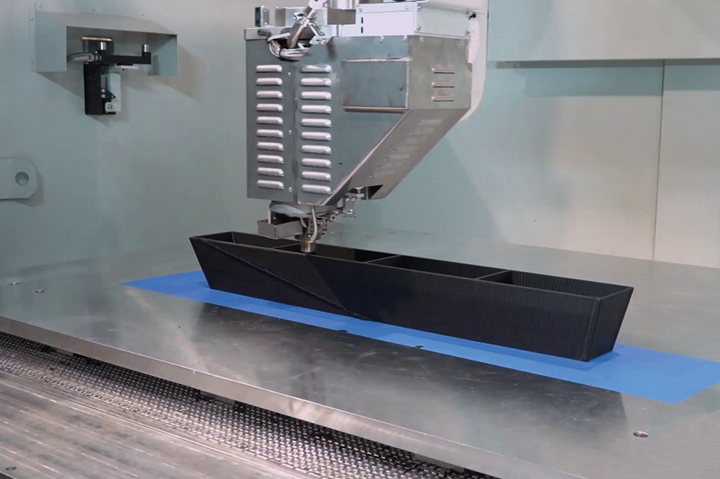
Photo Credit: CMS SpA
CMS Advanced Materials Technology, a division of CMS SpA (Zogno, Italy and Caledonia, Mich., U.S.) and part of the SCM Group (Rimini, Italy), has worked with the (Munich, Germany) to develop a hybrid large-format additive manufacturing (LFAM) machine, an integration of a tool machine and large-scale 3D printer.
The LFAM technology adopts what is known as screw extrusion additive manufacturing (SEAM), a 3D print extrusion unit developed by Fraunhofer IWU (Chemnitz, Germany) for the production of large components. The screw extruder is capable of producing standard thermoplastic polymer granulates reinforced with carbon or glass fiber. Materials that have been tested include PA, PP, PESU, PEI, PET, ABS and Airtech’s (Huntington Beach, Calif., U.S.) Dahltram resins.
According to CMS, the first hybrid machine will be delivered to plastic parts fabricator (Sargans, Switzerland) in April 2022, enabling the company to produce large-scale 3D pieces with maximum sizes of 1,800 x 2,200 x 800 millimeters under the future brand, .
“Innovation is our top priority,” says Barac S. Bieri, owner of Swissplast Group. “For years we have carefully followed everything happening on the market. With the hybrid machine, that can print large volume pieces up to 1,800 x 2,200 x 800 millimeters, we have finally achieved the long-awaited innovation.”
Related Content
-
The next evolution in AFP
Automated fiber placement develops into more compact, flexible, modular and digitized systems with multi-material and process capabilities.
-
Orbital Composites wins AFWERX award for Starfighter drone fleet
Under the TACFI contract, Orbital is implementing the AMCM process to build 3D printed composite multi-mission UAS aircraft, surpassing $10 million in government awards.
-
Large-format AM speeds plug production for manufacture of composite boat molds
Hungarian manufacturer Rapid Prototyping transitioned its conventional foam milling process to 3D printing to produce faster, higher quality, recyclable foam plugs and composite boat molds.