Successful tower extension test for James Webb space telescope
The test ensured the tower extensions on NASA’s composites-intensive telescope would keep the structure cool enough to detect infrared light.
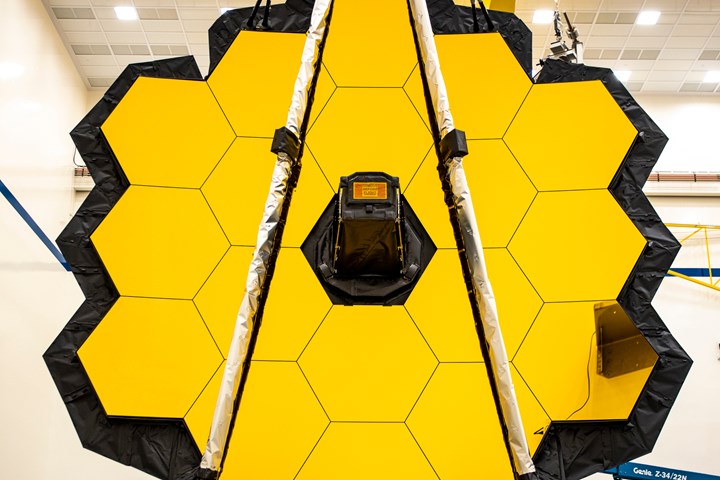
Technicians inspect a critical part of the James Webb Space Telescope known as the Deployable Tower Assembly after fully extending it in the same maneuver it will perform once in space. Source | Northrop Grumman
(Washington, D.C., U.S.) announced on June 9 that it has successfully deployed and extended the Deployable Tower Assembly as part of the testing regime of the James Webb Space Telescope (JWST). NASA’s most complex, composites-intensive space telescope, JWST is designed to look for faint traces of infrared light coming from astronomical objects.
NASA says the Deployable Tower Assembly’s primary purpose is to create a large gap between the upper part of the observatory that houses its gold mirrors and scientific instruments, and the lower section known as the spacecraft bus, which holds its comparatively warm electronics and propulsion systems. By creating a space between the two, it allows for Webb’s active and passive cooling systems to bring its mirrors and sensors down to the cold temperatures required to perform properly.
During the test, the tower was slowly extended 48 inches (1.2 meters) upward over the course of several hours. Simulating the zero-gravity environment in which Webb will operate, engineers employed a series of pulleys, counterbalances and a gravity-negation system that offloaded the effects of Earth’s gravity on the structure.
“It performed as predicted, and from our expectations from previous tests before the full observatory was assembled,” says Alphonso Stewart the Webb deployment systems lead for NASA’s Goddard Space Flight Center in Greenbelt, Md., U.S. “This was the first time this part of Webb was tested in its flight-like configuration to the highest level of fidelity we possibly could. This test provides the opportunity to assess all interfaces and interactions between the instrument and bus sections of the observatory."
As the largest space science observatory built, NASA says engineers had to design JWST to fold into a much smaller configuration to fit inside an Ariane 5 rocket for launch. The Deployable Tower Assembly — in addition to helping the observatory cool down — allows Webb to just barely fit inside a 17.8-foot (5.4-meter) payload fairing. Once in space, the tower will extend to give the rest of Webb’s deployable parts, such as the sunshield and mirrors, the amount of room needed to unpack and unfold into a fully functional infrared space observatory.
“We need to know that Webb will work the way we expect it to before we send it to space,” notes Stewart. “This is why we test, and when we do, we test as flight-like as possible. The way we send the commands to the spacecraft, the sequence, the individual sitting at the console, the communication that we use. We replicate all of these things to see if we are missing something, to see if there is something that needs to be changed, and to make sure that all of our planning to date has been correct.”
Following augmented personal safety procedures due to COVID-19, JWST’s team in California continued integration and testing work with significantly reduced on-site personnel and shifts. The NASA/Northrop Grumman team recently resumed near-full operations. NASA is evaluating potential impacts on the March 2021 launch date and will assess the schedule and adjust decisions as the situation unfolds.
Related Content
Plant tour: Collins Aerospace, Riverside, Calif., U.S. and Almere, Netherlands
Composite Tier 1’s long history, acquisition of stamped parts pioneer Dutch Thermoplastic Components, advances roadmap for growth in thermoplastic composite parts.
Read MoreHybrid process marries continuous, discontinuous composites design
9T Labs and Purdue applied Additive Fusion Technology to engineer a performance- and cost-competitive aircraft bin pin bracket made from compression-molded continuous and discontinuous CFRTP.
Read MoreJEC World 2024 highlights: Thermoplastic composites, CMC and novel processes
CW senior technical editor Ginger Gardiner discusses some of the developments and demonstrators shown at the industry’s largest composites exhibition and conference.
Read MoreThe potential for thermoplastic composite nacelles
Collins Aerospace draws on global team, decades of experience to demonstrate large, curved AFP and welded structures for the next generation of aircraft.
Read MoreRead Next
NASA assembles James Webb Telescope
NASA has successfully connected the two halves — the Optical Telescope Element (OTE) and the Space Craft Element (SCE) — of the composites intensive James Webb Telescope for the first time, marking a major milestone for the program.
Read MorePlant tour: Daher Shap’in TechCenter and composites production plant, Saint-Aignan-de-Grandlieu, France
Co-located R&D and production advance OOA thermosets, thermoplastics, welding, recycling and digital technologies for faster processing and certification of lighter, more sustainable composites.
Read MoreAll-recycled, needle-punched nonwoven CFRP slashes carbon footprint of Formula 2 seat
Dallara and Tenowo collaborate to produce a race-ready Formula 2 seat using recycled carbon fiber, reducing CO2 emissions by 97.5% compared to virgin materials.
Read More