SGL Carbon, Koller Kunststofftechnik manufacture composite windshield
Injection molded carbon fiber profiles for future BMW Group models cut 40% of weight compared to conventional steel construction and offer potential use in other automotive projects.
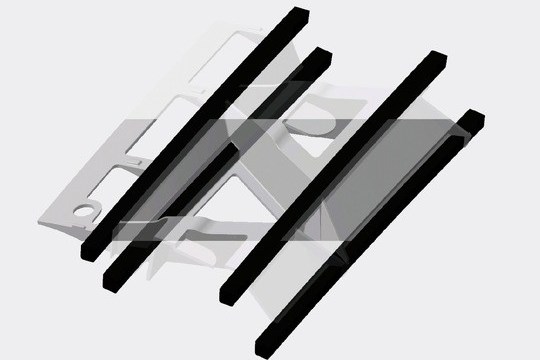
Skeletal windshield design. Photo Credit: SGL Carbon
In August 2020, SGL Carbon (Wiesbaden, Germany) received a multi-year order from (Lupburg, Germany) for the production of novel carbon fiber profiles for serial use in windshields, which will be applied in a high-volume model of BMW Group (Munich, Germany) within the next few years.
According to SGL Carbon, the profiles are composed from flexible fiber tows, pre-impregnated with thermoplastic resin in various dimensions. They will be compiled by SGL Carbon on the basis of its own 50K carbon fiber at its site in Innkreis, Austria, and subsequently processed by the injection molding experts at Koller to form a skeletal plastic component (More on this design with “Skeleton design enables more competitive composite autostructures” and “More details on MAI Skelett design process”). The composite component will reportedly replace the previous steel-based windshield. Production of the carbon fiber profiles will start in the remainder of 2020 and will then be ramped up gradually over the next few years for the BMW Group model launch.
As a vehicle’s windshield typically has an important stabilizing function, says SGL Carbon, the carbon fiber profiles add the required stiffness and crash safety to the component. At the same time, they are said to significantly reduce the weight of the roof and also support the driving dynamics. The injection molding process also enables particularly complex and material-efficient structures. In the BMW Group model, this innovative component concept will cut weight by 40% compared to conventional steel designs of the component, while creating important space for cable ducts and sensors.
SGL Carbon adds that the production of the carbon fiber profiles themselves is also particularly geared to material and process efficiency in large-scale production. The profiles consist of several smaller fiber strands — called “rods” — and are manufactured using the modern continuous pultrusion process. During product and process development it was one key objective to ensure that material loss during production was almost completely avoided.
"At SGL Carbon, we have been working on the development of thermoplastic carbon fiber profiles for use in injection molding for some time already. This developmental work is now beginning to pay off. Due to the many advantages and competitive costs, we see a great potential for the technology to be used in other automotive projects too," explains Sebastian Grasser, head of the Automotive Segment in the Business Unit Composites – Fibers and Materials at SGL Carbon.
"Innovative lightweight construction with hybrid designs has developed into a strategically conclusive concept for Koller Group's OEM customers," confirms Max Koller, CEO of Koller Group. "SGL Carbon's high level of material expertise, combined with the process know-how of Koller Kunststofftechnik and Koller Formenbau, create the basis for a promising future in innovative lightweight construction technologies. With this order, the BMW Group has confirmed its confidence in the successful cooperation between SGL and Koller; we are particularly pleased about this,” he adds.
The Koller Group is a globally operating technology company with plants in Europe and China, as well as NAFTA. The Koller Group develops and manufactures lightweight construction, tools and serial components, primarily for the automotive industry.
Related Content
Hybrid process marries continuous, discontinuous composites design
9T Labs and Purdue applied Additive Fusion Technology to engineer a performance- and cost-competitive aircraft bin pin bracket made from compression-molded continuous and discontinuous CFRTP.
Read MoreSulapac introduces Sulapac Flow 1.7 to replace PLA, ABS and PP in FDM, FGF
Available as filament and granules for extrusion, new wood composite matches properties yet is compostable, eliminates microplastics and reduces carbon footprint.
Read MorePlant tour: Airbus, Illescas, Spain
Airbus’ Illescas facility, featuring highly automated composites processes for the A350 lower wing cover and one-piece Section 19 fuselage barrels, works toward production ramp-ups and next-generation aircraft.
Read MoreOtto Aviation launches Phantom 3500 business jet with all-composite airframe from Leonardo
Promising 60% less fuel burn and 90% less emissions using SAF, the super-laminar flow design with windowless fuselage will be built using RTM in Florida facility with certification slated for 2030.
Read MoreRead Next
All-recycled, needle-punched nonwoven CFRP slashes carbon footprint of Formula 2 seat
Dallara and Tenowo collaborate to produce a race-ready Formula 2 seat using recycled carbon fiber, reducing CO2 emissions by 97.5% compared to virgin materials.
Read MoreAssembling the Multifunctional Fuselage Demonstrator: The final welds
Building the all-thermoplastic composite fuselage demonstrator comes to an end with continuous ultrasonic welding of the RH longitudinal fuselage joint and resistance welding for coupling of the fuselage frames across the upper and lower halves.
Read More“Structured air” TPS safeguards composite structures
Powered by an 85% air/15% pure polyimide aerogel, Blueshift’s novel material system protects structures during transient thermal events from -200°C to beyond 2400°C for rockets, battery boxes and more.
Read More