Researchers propose new technology to produce composites with adjustable properties
MISIS University and Skoltech scientists develop a method to obtain carbon fiber-reinforced polyethersulfone composite materials for aviation with adjustable properties.
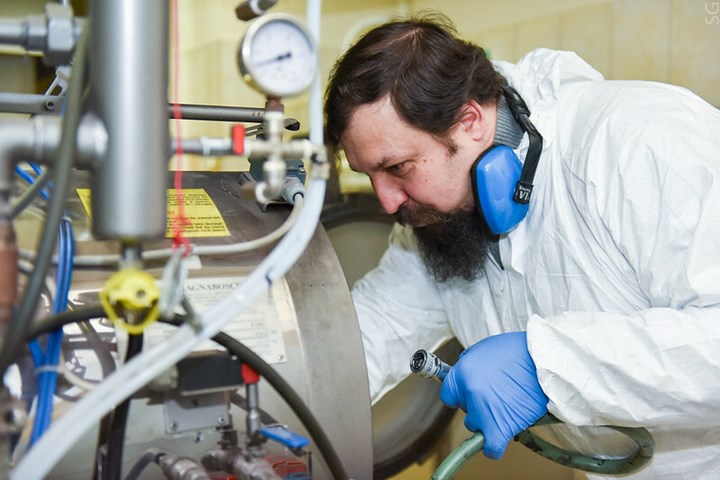
Photo Credit: MISIS University, Skoltech
Scientists at (Moscow, Russia) and the (Skoltech, Russia) have developed a new technology for the production of a new, durable composite material based on carbon fibers in a polyethersulfone matrix. Due to the combination of low density, high strength and chemical stability at elevated temperatures, researchers say it can be used in aggressive environments, such as fuel cells, super-capacitors and next-generation aircraft engine components. The composite can also be easily recycled or disposed of, making it environmentally friendly. The study has been published in .
Polyethersulfone powder, an amorphous thermoplastic polymer, is said to exhibit excellent mechanical properties and is resistant to high temperatures, steam and various chemicals. Unlike epoxy, it is recyclable.
During this research, the surface of the carbon fiber was modified by thermal oxidation, where a thin layer comprising a large number of oxygen-containing functional groups was formed on the surface of the carbon filaments. This was reported to facilitate better adhesion of the fiber to the polymer matrix. Moreover, in order to impregnate the carbon preform — which is traditionally performed via high-pressure impregnation of the polymer melt — researchers dissolved the polyethersulfone powder with an organic solvent at room temperature, after which the modified carbon fiber was impregnated with the resulting solution. Test samples were then dried at 100°C for four hours, and the preform was placed in a mold where the workpieces were being formed under pressure at 350°C for 30 minutes.
Researchers note that final property materials can be adjusted depending on the degree of filling the polymer matrix with fibers.
“Speaking about the possibilities of the material application, we need to look at the specific product in which will be used, since it affects working conditions in the structure, requirements for strength and maximum permissible deformations,” Ph.D. Andrey Stepashkin, senior researcher at the MISIS University Center for Composite Materials and a co-author of the work, explains. “Accordingly, the reinforcement pattern changes, and the degree of filling (fiber content) will also vary. But, if we talk, for example, about materials for aircraft construction, the optimal content of carbon fibers will be more likely in the range of 60-70% of the total weight of the structure.”
Read more about the project in .
Related Content
-
Bladder-assisted compression molding derivative produces complex, autoclave-quality automotive parts
HP Composites’ AirPower technology enables high-rate CFRP roof production with 50% energy savings for the Maserati MC20.
-
The lessons behind OceanGate
Carbon fiber composites faced much criticism in the wake of the OceanGate submersible accident. CW’s publisher Jeff Sloan explains that it’s not that simple.
-
Carbon fiber, bionic design achieve peak performance in race-ready production vehicle
Porsche worked with Action Composites to design and manufacture an innovative carbon fiber safety cage option to lightweight one of its series race vehicles, built in a one-shot compression molding process.