Plastic Omnium develops type IV hydrogen storage vessels for Hopium high-end sedan
Aiming to be the first French hydrogen-powered sedan to hit the market in 2026, the Hopium Mト…hina will be equipped with a 700-bar hydrogen vessel integrated into the vehicle chassis.
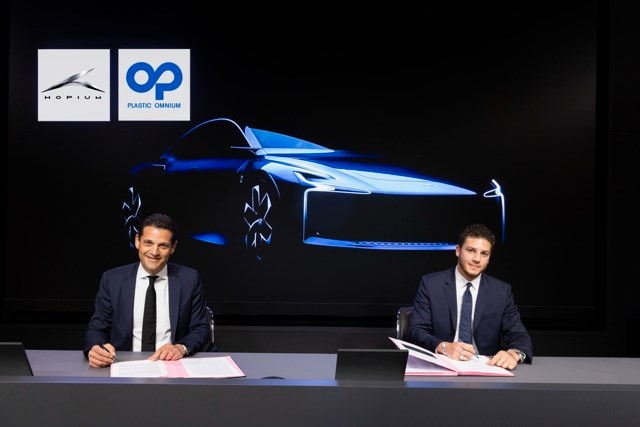
Laurent Favre, CEO of Plastic Omnium and Olivier Lombard, chairman and CEO of Hopium signing the agreement. Photo Credit: Plastic Omnium
(Île-de-France, France) partners with (Paris), a French manufacturer of high-end hydrogen cars, to develop the hydrogen storage system for the future Hopium Mト…hina. This high-end vehicle, first announced in October 2020, aims to be the first French hydrogen-powered sedan to hit the market in 2026. The Mト…hina prototype is due to be unveiled to the press in June 2021. It will be equipped with a 700-bar Type IV vessel — which comprises a thermoplastic liner reinforced with a filament-wound carbon fiber shell — made by Plastic Omnium at its Herentals, Belgium plant, which has been operational since fall 2020.
“With Hopium, we are convinced of hydrogen’s major role in tomorrow’s sustainable mobility,” says Laurent Favre, CEO of Plastic Omnium. “Plastic Omnium is proud to provide its expertise in hydrogen technologies and help develop the Hopium Mト…hina storage system, an innovative project for low-carbon mobility.”
Building on this initial collaboration, Hopium and Plastic Omnium have established a partnership to develop the Hopium Mト…hina hydrogen storage system for the production series. Based on almost 40 patents and a range of in-house developed, certified hydrogen storage vessels, Plastic Omnium will provide Hopium with a prototype high-pressure Type IV hydrogen vessel for testing. This new generation will be optimally integrated into the vehicle chassis, enabling Hopium to maximize the quantity of hydrogen stored and achieve its ambitious 1,000-kilometer target range.
Olivier Lombard, chairman and CEO of Hopium, adds: “As the first 100% hydrogen car manufacturer, Hopium stands at the forefront of green technologies. This partnership with Plastic Omnium shows our desire to collaborate with a key hydrogen mobility player to develop the Mト…hina, a new generation of zero-emission vehicle.”
Related Content
-
ZEBRA project demonstrates closed-loop wind recycling system
Consortium partners have proven the complete recycling of thermoplastic wind turbines via two manufactured wind blades, featuring reduced operating cost, CO2 emissions.
-
RTM, dry braided fabric enable faster, cost-effective manufacture for hydrokinetic turbine components
Switching from prepreg to RTM led to significant time and cost savings for the manufacture of fiberglass struts and complex carbon fiber composite foils that power ORPC’s RivGen systems.
-
Plant tour: Hexagon Purus, Kassel, Germany
Fully automated, Industry 4.0 line for hydrogen pressure vessels advances efficiency and versatility in small footprint for next-gen, sustainable composites production.