NASA X-59 supersonic research aircraft cleared for final assembly
Lockheed Martin is scheduled to complete construction of the X-59 Quiet SuperSonic Technology (QueSST) aircraft’s systems in late 2020, with first flights in 2021.
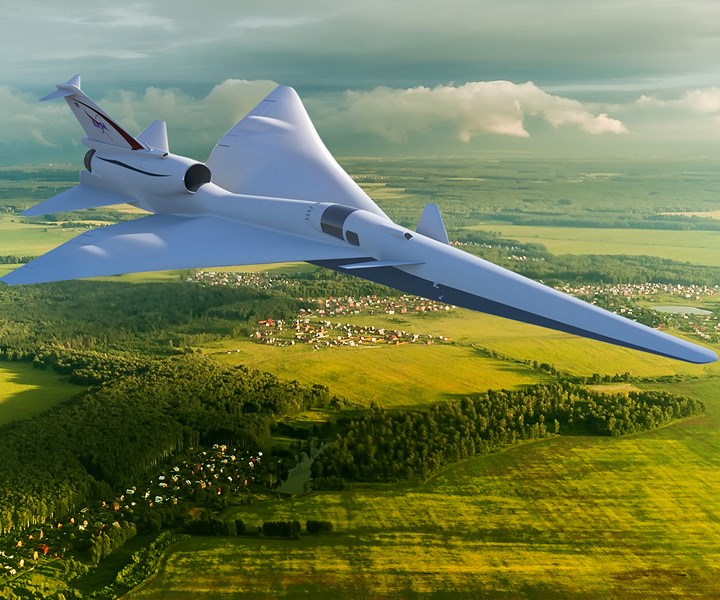
Source | NASA
The X-59 Quiet SuperSonic Technology (QueSST) aircraft — NASA’s first large-scale, piloted X-plane in more than three decades — has recently been cleared for final assembly and integration of its systems, following a major project review by senior managers at NASA headquarters in Washington, D.C., U.S.
According to NASA, the management review, known as Key Decision Point-D (KDP-D), was the last programmatic hurdle for the X-59 aircraft to clear before officials meet again in late 2020 to approve the airplane’s first flight in 2021.
The X-59 is shaped to reduce the loudness of a sonic boom reaching the ground — NASA says all that will be heard is a gentle thump, if it is heard at all.
Construction of the X-59, under a $247.5 million cost-plus-incentive-fee contract, is continuing at Lockheed Martin Aeronautics Co.’s Skunk Works factory in Palmdale, Calif., U.S.
Three major work areas are actively set up for building the airplane’s main fuselage, wing and empennage. Final assembly and integration of the airplane’s systems, including the cockpit eXternal Visibility System, is targeted for late 2020.
The aircraft will be flown above select U.S. communities to generate data from sensors and people on the ground in order to gauge public perception, and that data will reportedly help regulators establish new rules to enable commercial supersonic air travel over land.
“With the completion of KDP-D, we’ve shown the project is on schedule, it’s well planned and on track. We have everything in place to continue this historic research mission for the nation’s air-traveling public,” says Bob Pearce, NASA’s associate administrator for aeronautics.
Management of the X-59 QueSST development and construction falls under the project, which is part of NASA’s .
Related Content
-
Plant tour: Airbus, Illescas, Spain
Airbus’ Illescas facility, featuring highly automated composites processes for the A350 lower wing cover and one-piece Section 19 fuselage barrels, works toward production ramp-ups and next-generation aircraft.
-
Welding is not bonding
Discussion of the issues in our understanding of thermoplastic composite welded structures and certification of the latest materials and welding technologies for future airframes.
-
Automated robotic NDT enhances capabilities for composites
Kineco Kaman Composites India uses a bespoke Fill Accubot ultrasonic testing system to boost inspection efficiency and productivity.