Mikrosam celebrates commissioning of world's largest production line for CNG and hydrogen tanks
Turnkey project integrates four filament winding machines, two large ovens and multiple robotic lines and buffering stations to produce 60,000 tanks per year.
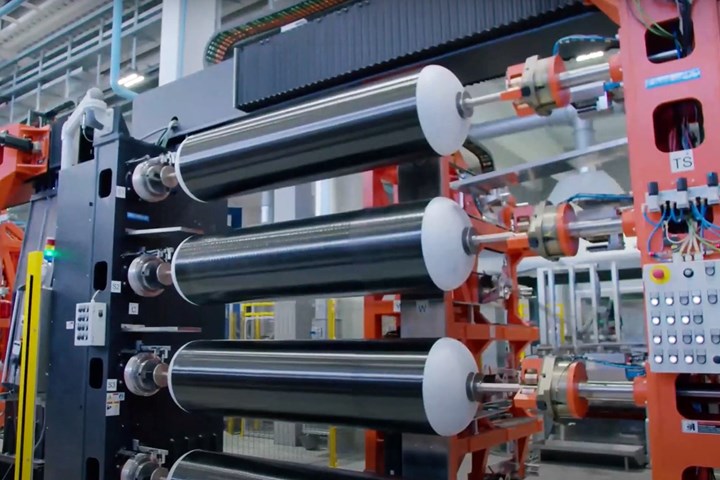
Photo Credit: Video produced by Mikrosam and JSC Plastic.
Mikrosam (Prilep, Macedonia) is proud to celebrate the commissioning of its latest automated production line by JSC DPO Plastik (Dzerzhinsk, Russia). The turnkey system features four multi-spindle filament winding machines, designed to build tanks between 40 and 350 liters in capacity for storing compressed natural gas (CNG) and hydrogen gas. The lines use glass and carbon fiber in towpreg or wet winding. Designed to produce more than 60,000 tanks annually, this production system is reportedly the largest in the automotive industry to date.
“Braving the pandemic and global supply issues, our engineers commissioned our most complex project yet,” says Dimitar Bogdanoski, sales manager at Mikrosam DOO. In addition to the filament winders, the automated system includes two large continuous curing (CC) ovens, multiple lines and buffer stations and an integrated handling system with two robots. For more details, see Mikrosam’s 2019 announcement of the project.
Related Content
-
Hybrid process marries continuous, discontinuous composites design
9T Labs and Purdue applied Additive Fusion Technology to engineer a performance- and cost-competitive aircraft bin pin bracket made from compression-molded continuous and discontinuous CFRTP.
-
Reinforcing hollow, 3D printed parts with continuous fiber composites
Spanish startup Reinforce3D’s continuous fiber injection process (CFIP) involves injection of fibers and liquid resin into hollow parts made from any material. Potential applications include sporting goods, aerospace and automotive components, and more.
-
Low-cost, efficient CFRP anisogrid lattice structures
CIRA uses patented parallel winding, dry fiber, silicone tooling and resin infusion to cut labor for lightweight, heavily loaded space applications.