Harper International received order for pitch carbon fiber oxidation oven system
The oven is critical for the University of Kentucky’s Center for Applied Energy Research procurement of coal-derived carbon fiber precursor material.
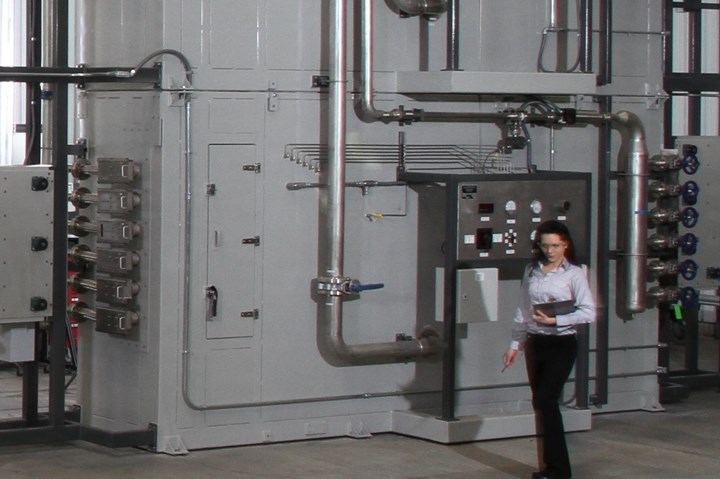
Photo Credit: Harper International
Harper International (Buffalo, N.Y., U.S.), a company offering complete thermal processing solutions for advanced materials, has been awarded a contract to engineer and manufacture a Pitch Carbon Fiber Stabilization Mesh Belt Oven system to be installed at the University of Kentucky’s Center for Applied Energy Research (CAER) located in Lexington, Ken., U.S. The equipment delivery and startup services are scheduled within 2022.
“The Oxidation Oven system is a critical piece of our fiber development facility at CAER,” says Matt Weisenberger, associate director of the Carbon Materials Technologies Group at the University of Kentucky.
This scientific-scale equipment will be used by researchers at the university to convert mesophase pitch, a liquid crystal derived from coal tar, into an oxidized carbon fiber precursor material. CAER’s research and investigation into coal-derived precursor material processes aims to lower the cost of producing high-quality carbon fibers by more than 50%, enabling application into widespread use such as automotive composite materials.
“Harper is pleased to support the University of Kentucky’s research into alternative carbon fiber precursor materials with our advanced thermal processing solutions,” says Paul Elwell, Harper VP of sales and marketing. “We expect the research conducted using the Harper oxidation oven system will help validate the advantages of lower raw material cost and higher yields offered by coal-pitch based carbon fibers.”
Related Content
-
Low-cost, efficient CFRP anisogrid lattice structures
CIRA uses patented parallel winding, dry fiber, silicone tooling and resin infusion to cut labor for lightweight, heavily loaded space applications.
-
Welding is not bonding
Discussion of the issues in our understanding of thermoplastic composite welded structures and certification of the latest materials and welding technologies for future airframes.
-
Composites manufacturing for general aviation aircraft
General aviation, certified and experimental, has increasingly embraced composites over the decades, a path further driven by leveraged innovation in materials and processes and the evolving AAM market.