ESE carbon fiber wheels launch to aftermarket segment
The E2 wheels, built from a combination of tailored fiber placement preforming with resin transfer molding, are available for select vehicles after passing stringent lab and field testing.
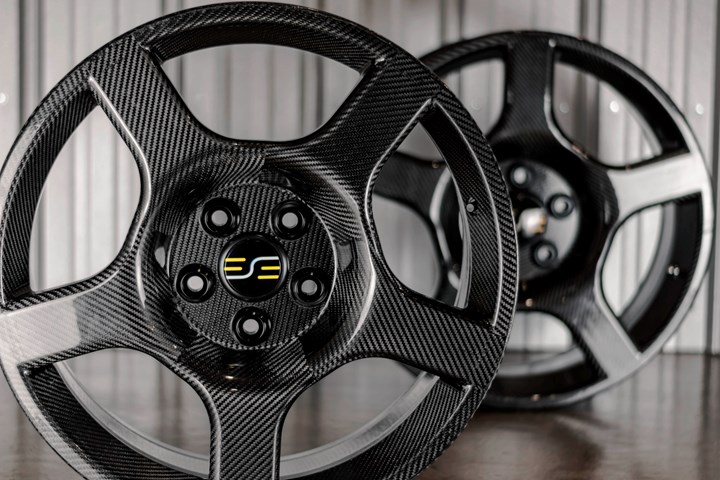
(ESE, Miami, Fla., U.S.) recently launched its E2 one-piece carbon fiber composite wheels into the market for the aftermarket segment. The initial E2 launch includes 19 x 8.5-inch wheels, servicing Tesla Model S, Tesla Model 3 and Subaru WRX STI vehicles.
The wheels, which CW wrote about in 2020, use tailored fiber placement (TFP) and high-pressure resin molding (RTM) to produce a lightweight, single-piece, high-performance wheel. Since CW last wrote about the wheels, ESE has completed its transition from initial autoclave processing to an improved RTM process using heated tooling. The resin and tooling are said to be preheated, with carefully controlled resin flow during infusion. Improvements have also been made to the TFP stitching process, to improve productivity as well as wheel mechanical properties. Small ply changes have been made to the E2s to ready them for market, to improve layup consistency, appearance and wheel test performance, and a clear coat solution has been finalized. The mounting hardware has also been refined to improve lug torque retention.
The wheels have been a four-year process to develop and test, ultimately passing stringent fatigue and impact tests set by the Society of Automotive Engineers’ (SAE) Recommended Practices for wheels.
According to ESE and , SAE recommended practices such as SAE J328 for vehicle wheels, SAE J2530 for aftermarket wheels, SAE J2562 for biaxial wheels, and SAE J175 for road vehicle wheels were originally designed to test traditional metal wheels. The E2s were able to pass all tests required of SAE, due to the wheels’ rigorous engineering analysis and testing during development, the company says.
Dr. Michael Hayes, ESE Carbon’s VP, head of engineering, served on an SAE committee in 2020 to develop new recommended practices specific to fiber-reinforced composite wheels.
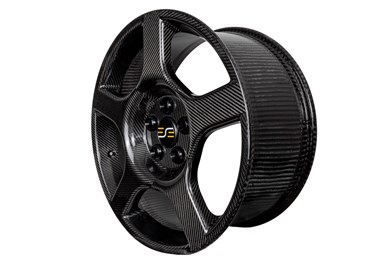
The resulting SAE J3204 adapts the Recommended Practices for metal wheels to composite wheels, imposing new requirements such as strength reduction factors (SRFs) to account for environmental effects, maximum operating temperature testing, and electricity conductivity testing.
ESE emphasizes that its E2 wheels have also been proven to withstand impact at very cold temperatures, above and beyond the requirements. The company conducted its own independent lab testing to test curb and pothole impact at -40°C. The company says its wheels were not affected by the cold temperatures at all, thanks to specially developed wheel flanges designed with a high percentage of circumferentially oriented carbon fiber to maximize hoop strength. This strength is said to be great enough to enable the circumferential plies to be “nearly insensitive” to cold temperatures. “We have taken great care to design very robust flanges in our wheels,” Dr. Hayes explains. “In addition, because of the superior strength-to-weight ratio of carbon fiber composites, we can increase the size of the flanges to further increase impact strength without a weight penalty.” The TFP process allows for production of circular plies at a high fiber volume fraction.
See for more information.
Related Content
Improving carbon fiber SMC simulation for aerospace parts
Simutence and Engenuity demonstrate a virtual process chain enabling evaluation of process-induced fiber orientations for improved structural simulation and failure load prediction of a composite wing rib.
Read MoreCo-molding SMC with braided glass fiber demonstrates truck bed potential
Prepreg co-molding compound by IDI Composites International and A&P Technology enables new geometries and levels of strength and resiliency for automotive, mobility.
Read MoreTPI manufactures all-composite Kenworth SuperTruck 2 cab
Class 8 diesel truck, now with a 20% lighter cab, achieves 136% freight efficiency improvement.
Read More“Structured air” TPS safeguards composite structures
Powered by an 85% air/15% pure polyimide aerogel, Blueshift’s novel material system protects structures during transient thermal events from -200°C to beyond 2400°C for rockets, battery boxes and more.
Read MoreRead Next
One-piece, one-cure, infused carbon fiber wheel is ready to roll
ESE Carbon Co.’s new carbon fiber wheel uses tailored fiber placement and custom presses to minimize waste and improve scalability.
Read MoreAssembling the Multifunctional Fuselage Demonstrator: The final welds
Building the all-thermoplastic composite fuselage demonstrator comes to an end with continuous ultrasonic welding of the RH longitudinal fuselage joint and resistance welding for coupling of the fuselage frames across the upper and lower halves.
Read More“Structured air” TPS safeguards composite structures
Powered by an 85% air/15% pure polyimide aerogel, Blueshift’s novel material system protects structures during transient thermal events from -200°C to beyond 2400°C for rockets, battery boxes and more.
Read More