Carbon Rivers to commercialize fiberglass composites upcycling project
Novel pyrolysis method recovers fiberglass reinforcement into new, high-value discontinuous composites with minimized input energy requirements for a true circular economy.
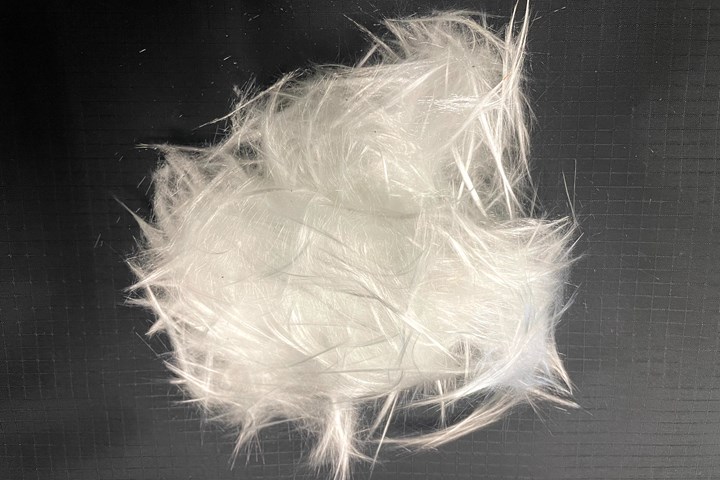
Clean glass fiber. Photo Credit: Carbon River LLC
(Knoxville, Tenn., U.S.) reports that it was selected by the U.S. Department of Energy (DOE) via a Small Business Innovation Research (SBIR)/Small Business Technology Transfer (STTR) project to commercialize new technology for the upcycling of glass fiber-reinforced polymer (GFRP) composites from retired wind turbine blades.
According to the company, this novel pyrolysis, or thermal decomposition, method separates polymers and other organic materials from fiberglass reinforcement, allowing the fibers to be recovered mechanically intact and then reused for manufacturing. Then, these resins/organics are captured as energy to power the recovery process, reportedly minimizing input energy requirements.
Overall, this process is said to enable glass fiber composite waste to be recovered back into new, high-value composites for a true circular materials economy.
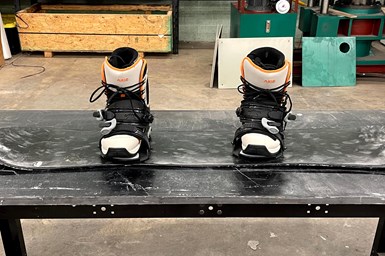
A snow board we made out of the upcycled glass fiber. Photo Credit: Carbon Rivers LLC
Carbon Rivers says recovered fiberglass can be upcycled into a variety of discontinuous composites such as nonwoven fabrics, compounded thermoplastics, injection molding pellets and 3D printer filaments. The company is also working to design materials for different composite-consuming industrials such as marine, automotive, sporting goods, etc.
Additionally, the company has already expanded its upcycling capacity at its Knoxville, Tenn., U.S. facility. This will include a new 2.5-acre laydown yard for accepting incoming wind blade and other composite waste material streams. A new 26,000-square-foot facility retains a 30 ton/month pilot recycling line and 40 ton/month thermoplastic pellet production capacity. Carbon Rivers is currently running a one ton/day process, but will scale up to a 20 ton/day process next year. By 2023, this will be 200 tons/day in multiple facilities located in the U.S., Europe and Asia.
Related Content
-
Otto Aviation launches Phantom 3500 business jet with all-composite airframe from Leonardo
Promising 60% less fuel burn and 90% less emissions using SAF, the super-laminar flow design with windowless fuselage will be built using RTM in Florida facility with certification slated for 2030.
-
Revisiting the OceanGate Titan disaster
A year has passed since the tragic loss of the Titan submersible that claimed the lives of five people. What lessons have been learned from the disaster?
-
The potential for thermoplastic composite nacelles
Collins Aerospace draws on global team, decades of experience to demonstrate large, curved AFP and welded structures for the next generation of aircraft.