CalTestBed voucher advances R&D efforts for Helicoid Industries leading edge protection technology
In partnership with the University of California, Irvine and New Energy Nexus’ CalTestBed Initiative, Helicoid Industries is to test and de-risk Helicoid leading edge protection technology solution for lighter, highly efficient and durable composite wind blades.
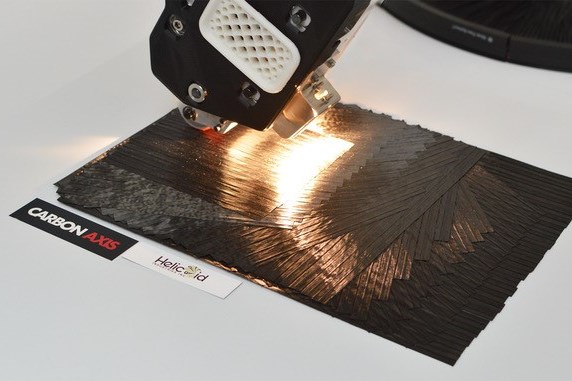
Photo Credit: Carbon Axis, Helicoid Industries
(Indio, Calif., U.S.) which is commercializing the Helicoid biomimetic fiber-reinforced composite technology, has been awarded a $294,000 voucher for the testing and commercialization of its leading-edge protection technology as part of the 2020 California Test Bed Initiative (CalTestBed) recommendation process, administered by New Energy Nexus.
The company’s Helicoid technology, which has been originally applied to protective helmet prototypes, is a bio-inspired fiber-reinforced composite which reportedly draws its features from a wide variety of microstructures found in nature which have evolved to protect against severe impacts and harsh environments.
“The Helicoid technology offers excellent impact resistance under various loading conditions, including low-velocity/large-mass impacts, high-velocity/small-mass impacts, up to ballistic impacts,” says Dr. Lorenzo Mencattelli, director of research and development at Helicoid Industries Inc. “A recent preliminary investigation on the performances of Helicoid to endure high-frequency, small-mass impacts, such as the ones generated by water droplets or sand/dust on the leading edge of composite wind blades has revealed the capability of Helicoid substrates to greatly increase the resistance to rain erosion.”
Mencattelli notes that the investigation on such complex impact fatigue phenomenon will be the focus of the CalTestBed voucher testing, to deliver an all-in-one solution for wind blades that are lighter, higher efficiency, lower maintenance and more durable, and that can hold up against a variety of threats, including bird strike, lightning strikes and rain/sand erosion. Ultimately, the voucher will also demonstrate the benefits of biomimetic composite innovation and technology in renewable energy products.
CalTestBed is a laboratory testing and commercialization development program for innovators and entrepreneurs working to bring clean energy concepts to market. It is made possible by an $11 million grant from the California Energy Commission. CalTestBed accelerates entrepreneurs by awarding vouchers to California-based companies to test and de-risk technologies at one of nearly 60 testbeds across the UC system and Lawrence Berkeley National Laboratory. CalTestBed recognizes entrepreneurs’ struggles in making the leap to commercialization and has formed a partnership with the UC Office of the President and University of California system to assist clean energy entrepreneurs in testing their technology at world-class testing facilities.
“California is recognized as a leader in progressive clean energy and climate policies, as well as in technology innovation,” says Tenley Dalstrom, New Energy Nexus’ CalTestBed program director. “As more wind turbines are installed to deliver on the commitment to increase clean energy generation, we are excited to work with Helicoid Industries on testing this innovative material that we hope will be refined and deployed to protect those investments.”
Helicoid Industries has partnered with the University of California, Irvine – Institute for Design and Manufacturing Innovation to test various configurations of laminates using Helicoid technology for protection of the wind blade including leading edge, structure and other parts. Several proofs of concept and demonstrators using the Helicoid technology will be manufactured and tested during the execution of the work plan. Furthermore, Helicoid Industries is closely collaborates with SAERTEX (Saerbeck, Germany) for the production of Helicoid multiaxial noncrimp fabrics (NCF) to be used for the CalTestBed project. Helicoid Industries notes that such a partnership is key to delivering an innovative Helicoid LEP solution that meets the challenging wind blade industry costs and quality standards.
“With Helicoid, we have a strong partner with whom we share a common goal: offering innovative solutions tailored to customer applications,” says Jan Hindahl, team leader technical service and innovation at SAERTEX.“By using the multiaxial technology we expect to promote the Helicoid technology in an efficient way.”
Related Content
Trends fueling the composites recycling movement
Various recycling methods are being considered for composites, from novel dismantling and processing, to building capacity and demonstrating secondary use applications.
Read MoreComposites end markets: Energy (2024)
Composites are used widely in oil/gas, wind and other renewable energy applications. Despite market challenges, growth potential and innovation for composites continue.
Read MoreInfinite Composites: Type V tanks for space, hydrogen, automotive and more
After a decade of proving its linerless, weight-saving composite tanks with NASA and more than 30 aerospace companies, this CryoSphere pioneer is scaling for growth in commercial space and sustainable transportation on Earth.
Read MoreAcciona to build wind blade recycling plant in Spain by 2025
Waste2Fiber facility will use a proprietary thermal method to separate wind blade materials for reuse and will have a processing capacity of 6,000 tons of material/year.
Read MoreRead Next
Developing bonded composite repair for ships, offshore units
Bureau Veritas and industry partners issue guidelines and pave the way for certification via StrengthBond Offshore project.
Read MorePlant tour: Daher Shap’in TechCenter and composites production plant, Saint-Aignan-de-Grandlieu, France
Co-located R&D and production advance OOA thermosets, thermoplastics, welding, recycling and digital technologies for faster processing and certification of lighter, more sustainable composites.
Read More“Structured air” TPS safeguards composite structures
Powered by an 85% air/15% pure polyimide aerogel, Blueshift’s novel material system protects structures during transient thermal events from -200°C to beyond 2400°C for rockets, battery boxes and more.
Read More