Cabin Management Systems leverages Markforged carbon fiber 3D printers for FAA-compliant end-use parts
Cabin Management Solutions (CMS) incorporates the Markforged X7 printer and Onyx FR material for high-quality, rapid parts production for cabin management maintenance, upgrades and replacements for luxury aircraft.
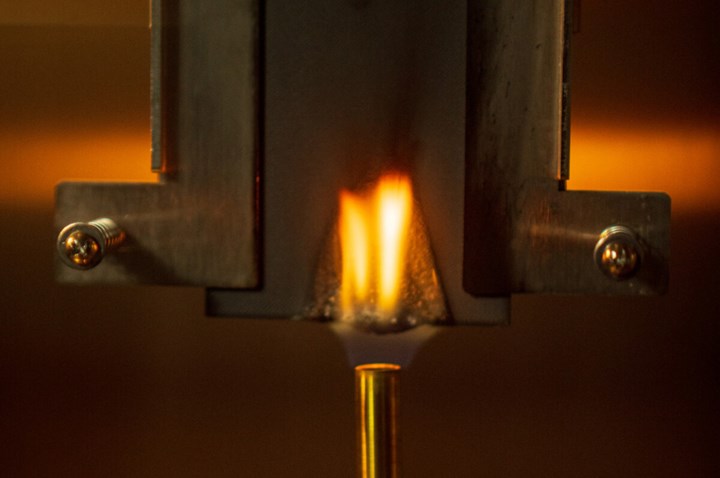
CMS uses Onyx FR to deliver custom parts that are high strength, low weight, and flame retardant. Photo Credit: Markforged, CMS
(Watertown, Mass., U.S.), creator of the integrated metal and carbon fiber additive manufacturing platform, , has announced that (CMS, Conroe, Texas, U.S.), a privately held in-flight cabin management and entertainment systems company, is using two to print high-quality, end-use parts for cabin management maintenance, upgrades and replacements for luxury aircraft.
CMS was founded in 2019 and works frequently with aircraft maintenance, repair and overhaul (MRO) companies and individual aircraft owners to design and develop cabin control and entertainment systems for luxury, private and business jets. CMS uses Onyx FR to fabricate custom parts that are high strength, low weight, flame retardant and FAA compliant. According to Markforged, the X7 printers retain improved the quality and speed of parts production, enabling CMS to complete a higher volume of jobs more quickly and earning it a reputation for fast time to market, high-quality deliverables and rigorous testing and certification process.
“In the aerospace industry, quality and on-the-fly adaptability are crucial to success,” says Jeff Pike, VP of engineering at CMS. “We often have to produce low-volume, high-value parts from scratch which can be time- and labor-intensive. Markforged’s X7 allows us to do this quickly and more efficiently, while ensuring functionality and retaining the upscale aesthetics expected in luxury aircraft.”
On one aircraft in particular, the CMS team printed at least 100 different parts, including approximately 20 light switch panels, a cabin climate controller, latches, release buttons, USB-C and drop-in USB-A chargers and adjustable touch screen brackets — all using the X7 printer. In order to meet the specific demands of its luxury-oriented customers, the CMS team then adds an extra level of customization via overlays that mimic upscale cabin surfaces including gold metal electroplating, wood veneer and more. CMS says its process ensures the end product is FAA compliant while going above and beyond customers’ expectations for aesthetics.
Moving forward, CMS plans to continue leveraging Markforged’s additive solutions, especially with Markforged’s recent release of Onyx FR-A and Carbon Fiber FR-A, aerospace-ready versions of its Onyx FR and Carbon Fiber FR materials. These two new materials come with full material traceability and are undergoing qualification on the Markforged X7 printer via a program conducted by the National Center for Advanced Materials Performance (NCAMP), one of two bodies authorized by the FAA to qualify materials for flight. Once this process is complete, CMS will be able to increase its overall production speed, which will result in adding even more jobs to its already expanding pipeline.
“CMS has incorporated Markforged technology into their business in a way that enables them to maintain their reputation for high-quality and give themselves competitive advantage,” says Markforged President and CEO Shai Terem. “Our technology is not only about printing parts faster and at the point of need, but also giving aerospace manufacturers the confidence that their parts meet the regulatory and functional requirements of their industry.”
To read more about CMS’s use of Markforged printers, visit the company’s .
Related Content
Otto Aviation launches Phantom 3500 business jet with all-composite airframe from Leonardo
Promising 60% less fuel burn and 90% less emissions using SAF, the super-laminar flow design with windowless fuselage will be built using RTM in Florida facility with certification slated for 2030.
Read MoreWelding is not bonding
Discussion of the issues in our understanding of thermoplastic composite welded structures and certification of the latest materials and welding technologies for future airframes.
Read MoreCombining multifunctional thermoplastic composites, additive manufacturing for next-gen airframe structures
The DOMMINIO project combines AFP with 3D printed gyroid cores, embedded SHM sensors and smart materials for induction-driven disassembly of parts at end of life.
Read MoreA new era for ceramic matrix composites
CMC is expanding, with new fiber production in Europe, faster processes and higher temperature materials enabling applications for industry, hypersonics and New Space.
Read MoreRead Next
Composites end markets: New space (2025)
Composite materials — with their unmatched strength-to-weight ratio, durability in extreme environments and design versatility — are at the heart of innovations in satellites, propulsion systems and lunar exploration vehicles, propelling the space economy toward a $1.8 trillion future.
Read MoreAll-recycled, needle-punched nonwoven CFRP slashes carbon footprint of Formula 2 seat
Dallara and Tenowo collaborate to produce a race-ready Formula 2 seat using recycled carbon fiber, reducing CO2 emissions by 97.5% compared to virgin materials.
Read MoreAssembling the Multifunctional Fuselage Demonstrator: The final welds
Building the all-thermoplastic composite fuselage demonstrator comes to an end with continuous ultrasonic welding of the RH longitudinal fuselage joint and resistance welding for coupling of the fuselage frames across the upper and lower halves.
Read More