Bye eFlyer 2 flight test data supports electric propulsion claims
Bye Aerospace estimates its eFlyer will eliminate 3 million metric tons of CO2 every year otherwise produced to train the needed new airline pilots.
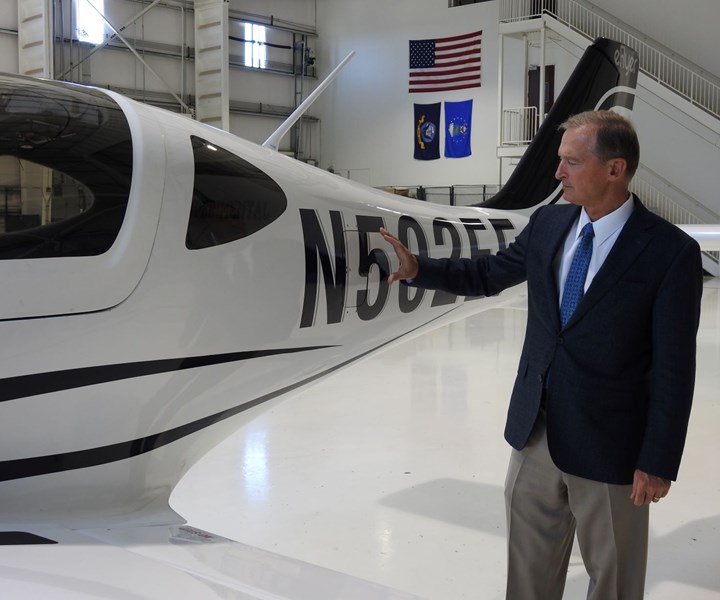
George E. Bye, CEO of Bye Aerospace with the eFlyer 2 prototype Source | Bye Aerospace
Bye Aerospace (Englewood, Colo., U.S.) has announced further progress with its eFlyer 2 developmental prototype flight test program, releasing new data that continues to confirm the benefits of electric aviation.
“In a series of flight tests, our team explored a broad range of power settings and speeds using the Rolls Royce SP70d motor,” says George E. Bye, CEO of Bye Aerospace. “Using a 60 kW power setting, rate of climb was 650 feet per minute and at 70 kW was 750 feet per minute at a relatively high 10,000 feet density altitude. Of particular note is that conventional general aviation aircraft achieve these climb rates only at sea level.” Bye added that at 36 kW cruise power setting, true airspeed of 100 knots was achieved.
Earlier this year, Boeing (Chicago, Ill., U.S.) announced that 804,000 new commercial airline pilots will be needed over the next 20 years — a five-fold increase in the current amount of airline pilots. The eFlyer 2 is designed to address the training requirements that this urgent professional pilot demand creates. Bye Aerospace is developing the FAA FAR 23-certified family of eFlyer general aviation aircraft, starting with the eFlyer 2, for the flight training mission.
“We continue to push forward on our FAA certification program with efficiency and urgency, remaining focused on safety as our highest priority,” Bye says.
All of Bye Aerospace’s current and future families of aircraft, including the eFlyer 2 and the eFlyer 4, are designed to answer market needs including five-fold lower operating costs, zero emissions and decreased noise. Bye Aerospace estimates the eFlyer will eliminate 3 million metric tons of CO2 every year otherwise produced to train the needed new airline pilots.
Related Content
-
AMRC Training Centre introduces composites apprenticeship opportunity
With partners McLaren and Teledyne CML Composites, the Training Center will train new composites technicians in South Yorkshire to build up the future industry workforce.
-
Daher inaugurates Learning Center for training aeronautical talent
Daher offers a concrete solution to the shortage of qualified professionals in aerospace, providing a range of technical programs that prepare workers for the sector’s rigorous demands.
-
FACC Academy begins training, onboarding operations
FACC’s newly launched training platform will address skilled aerospace worker shortages head on, offering more than 250 specialized training courses for its entire workforce.