Borealis Borcycle material grades enhance sustainability opportunities for automotive
Ready-made grades combine virgin polypropylene with high-quality reclaimed materials for interior, exterior and under-the-bonnet automotive applications.
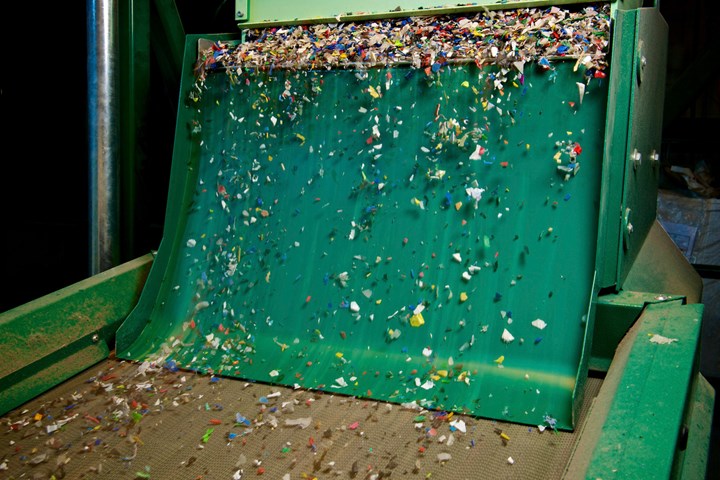
Photo Credit: Borealis
(Vienna, Austria and Taylorsville, N.C., U.S.), a supplier of innovative polyolefin plastic materials for engineering applications in the automotive industry, has announced the availability of , its innovative polyolefin-based solution composed of both virgin and post-consumer recyclate (PCR) for the North American automotive market. The Borcycle family of products have been conceived for interior, exterior and under-the-bonnet automotive applications and incorporate post-consumer recycled (PCR) content for a lower environmental impact.
Originally developed by Borealis in Europe, ready-made PCR Borcycle grades combine virgin polypropylene with high-quality reclaimed materials. They are safe to use and are said to provide a material performance and cost-efficiency equal to the performance and cost-efficiency of virgin materials.
Borealis notes that products in the Borcycle family are backed by a reliable supply chain and quality standards. The company believes it has conquered the challenges associated with sourcing and processing recycled content, ensuring automotive customers and partners that they can rely on a steady supply of resource-efficient Borcycle grades with consistent high quality.
Related Content
-
Toray, Elevated Materials repurpose carbon fiber prepreg waste
MOU advances efforts to reduce waste, conserve resources and decrease pollution through upcycling of Toray’s composite material scrap.
-
HRC, Airbus LSC launch aircraft dismantling, recycling project
The first project is underway to recover carbon fiber used in an A330-200 aircraft, which will then be regenerated for other end uses by HRC.
-
CIDER project highlights rCF automotive door using Elium resin
European consortium develops novel processes, sustainable designs through three demonstrators to increase recycled carbon fiber use in transportation applications.