BASF, L&L Products and Stellantis recognized for 2021 Jeep Grand Cherokee L lightweighting
Composite tunnel reinforcement comprised of pultruded continuous glass fiber reinforced with Elastocoat polyurethane system for 40% weight savings and improved overall performance.
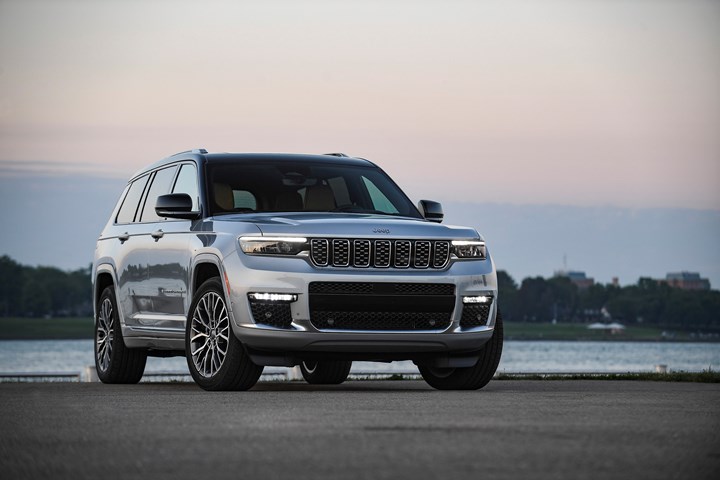
Jeep Grande Cherokee L. Photo Credit: BASF
BASF (Florham Park, N.J., U.S.), L&L Products (Romeo, Mich., U.S.) and (Amsterdam, Netherlands) have been recognized for achievements in vehicle lightweighting on the composite tunnel for the 2021 Jeep Grand Cherokee L — launched in May 2021 — at this year’s 9th annual Altair Enlighten Award.
While researching opportunities to reduce mass and improve durability without compromising safety performance, the transmission mounting system (TMS) was one area of focus. The composite tunnel reinforcement (CTR) is located on the underside of the vehicle and is part of the overall TMS. In the event a vehicle collides slightly with an opposing vehicle for example, the CTR transfers the energy load from the outer rail to the transmission mount crossmember, improving performance in the field and in the Insurance Institute for Highway Safety (IIHS) standards small offset rigid barrier test.
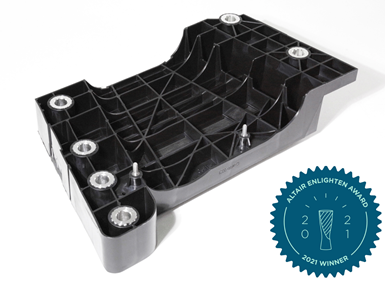
Composite tunnel. Photo Credit: BASF
The use of Continuous Composite Systems (CCS) pultrusion technology along with polyurethane chemistry from BASF were key factors in the success of the CTR. CCS combines a fiber-reinforced pultruded composite carrier with highly engineered sealants and adhesives in a 2D profile. This is a continuous process used to create straight or curved composite profiles reinforced with continuous fibers and mats. The system is designed to provide strength, stiffness and rigidity to a lightweight structure.
“CCS enabled L&L Products and Stellantis to realize a new design that reduces packaging along with mass and uses the surrounding environment on the vehicle to help transition loads to the CTR,” says Hank Richardson, product engineering manager, L&L Products. “We also made technology improvements to achieve an industry first in processing speeds as we doubled the typical profile pultrusion output.”
According to partners, this was also the first application for L&L Products using its CCS technology and BASF’s Elastocoat 74850 polyurethane pultrusion system.
“Our Elastocoat polyurethane chemistry coupled with continuous glass fiber has a superior strength-to-weight ratio in comparison to ultra-high strength steel when used in these kinds of applications,” says Chris Korson, chassis market segment manager, performance materials, BASF Corp. “We also developed a new computer simulation methodology using our proprietary CAE modeling software Ultrasim to capture the behavior of the pultruded structures to accurately capture the additional load after failure that a composite provides.” (See “BASF, Toyota collaborate for 2021 Sienna lightweighting” to learn more about BASF’s lightweight achievements.)
According to Stellantis Chassis Engineering Manager Brian Dwyer, the company is always looking to improve on the design, function and efficiency of its vehicles. “It’s not easy to find a weight reduction solution that improves overall performance but that’s exactly what we have done on the 2021 Jeep Grand Cherokee L composite tunnel,” Dwyer says.
The state-of-the-art 2021 Jeep Grand Cherokee L is said to be designed inside and out to deliver unmatched capability and composed driving dynamics. Its 4x4 systems instill Grand Cherokee L with the Jeep brand’s 4x4 capability. An all-new architecture and sculpted aerodynamic body style combine to reportedly improve vehicle performance, safety and reliability, while significantly reducing vehicle weight, noise, vibration and harshness. Designed to maximize overall passenger safety, comfort and convenience, Grand Cherokee L packs a powerful punch with next-generation features and technologies, partners say, that make it a standout in the full-size SUV segment.
Related Content
Combining multifunctional thermoplastic composites, additive manufacturing for next-gen airframe structures
The DOMMINIO project combines AFP with 3D printed gyroid cores, embedded SHM sensors and smart materials for induction-driven disassembly of parts at end of life.
Read MoreThe next evolution in AFP
Automated fiber placement develops into more compact, flexible, modular and digitized systems with multi-material and process capabilities.
Read MoreCarbon fiber, bionic design achieve peak performance in race-ready production vehicle
Porsche worked with Action Composites to design and manufacture an innovative carbon fiber safety cage option to lightweight one of its series race vehicles, built in a one-shot compression molding process.
Read MoreLow-cost, efficient CFRP anisogrid lattice structures
CIRA uses patented parallel winding, dry fiber, silicone tooling and resin infusion to cut labor for lightweight, heavily loaded space applications.
Read MoreRead Next
Composites feature in Altair’s 8th Annual Enlighten Awards
Recognized jointly with the Center for Automotive Research (CAR), winners represent the world’s best initiatives to reduce vehicle weight and meet emissions targets.
Read MoreAssembling the Multifunctional Fuselage Demonstrator: The final welds
Building the all-thermoplastic composite fuselage demonstrator comes to an end with continuous ultrasonic welding of the RH longitudinal fuselage joint and resistance welding for coupling of the fuselage frames across the upper and lower halves.
Read MoreVIDEO: High-volume processing for fiberglass components
Cannon Ergos, a company specializing in high-ton presses and equipment for composites fabrication and plastics processing, displayed automotive and industrial components at CAMX 2024.
Read More