Armacell passes two billion milestone in reuse of plastic bottles
Patented recycled PET (rPET) foam technology contributes to a circular economy in plastics in an effort to substitute competing materials such as PVC, PUR, balsa and honeycomb.
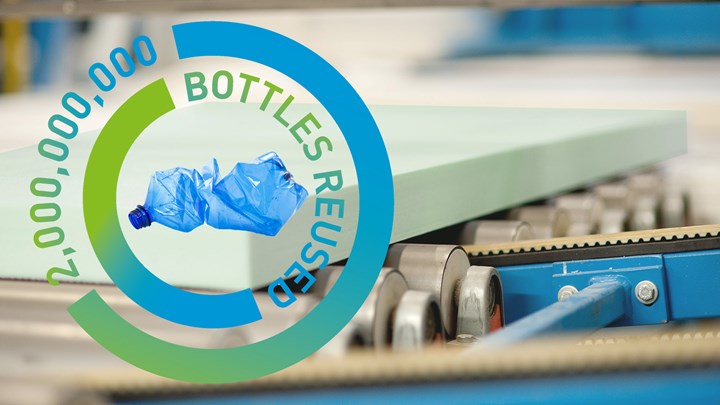
Photo Credit: Armacell
Armacell (Luxembourg/Thimister, Belgium), a global supplier of flexible foam for the equipment insulation market and engineered foams, has passed a significant recycling milestone, with two billion waste plastic bottles given a new life using the company’s recycled PET (rPET) foam technology.
“The start of rPET series production to the one billion recycled bottles’ milestone took nine years; for the second billion only two years,” Thomas Kessel, managing director, PET Foams, Armacell, says. ”In recent years, we have greatly expanded our production capacities and extended the geographical reach by opening additional production lines in Brampton, Canada. in 2017 and in Suzhou, China, in 2020. In 2021, two more production lines were commissioned at the Armacell PET headquarters in Thimister, Belgium.”
According to Henri Chapelle, global sales and marketing manager, PET Foams, Armacell, the growing demand for rPET foam core products has been driven, on the one hand, by the replacement of competing materials such as PVC, PUR, balsa, honeycomb materials and so on, and on the other hand by the increasing use of rPET foam core products in the wind energy, transport, construction and other industries.
“Another factor fueling this demand surge has been the desire for more sustainable sourcing in the material selection process,” Chapelle adds. “As a result, industrial designers, specifiers and composite manufacturers are increasingly replacing those traditional core materials with ArmaPET products, which are made from recycled plastic bottles and are fully recyclable themselves.”
Related Content
-
All-recycled, needle-punched nonwoven CFRP slashes carbon footprint of Formula 2 seat
Dallara and Tenowo collaborate to produce a race-ready Formula 2 seat using recycled carbon fiber, reducing CO2 emissions by 97.5% compared to virgin materials.
-
Partners recycle A350 composite production waste into adjustable-length rods for MFFD
Herone, Spiral RTC, Teijin Carbon Europe and Collins Aerospace Almere recycle A350 thermoplastic composite clips/cleats waste into rods for the all-thermoplastic composite Multifunctional Fuselage Demonstrator’s crown.
-
Plant tour: Hexagon Purus, Kassel, Germany
Fully automated, Industry 4.0 line for hydrogen pressure vessels advances efficiency and versatility in small footprint for next-gen, sustainable composites production.