Arevo introduces high-speed AM system, closes Series B financial round
The financing round and high-speed AM system for large continuous carbon fiber composite structures follow Arevo’s 3D-printed bicycle campaign.
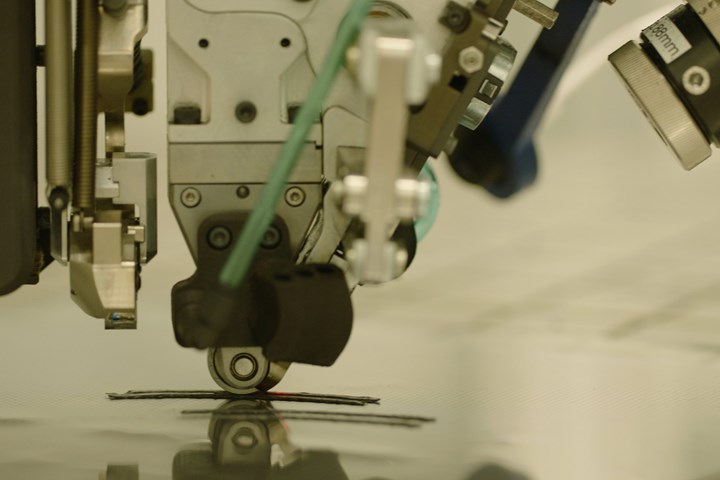
Aqua 2 printer head. Photo Credit: Arevo
Additive manufacturing specialist Arevo (Milpitas, Calif., U.S.) announced on August 11 the introduction of its newest system, the Aqua 2, what Arevo says is the world’s first high-speed additive manufacturing system for large continuous carbon fiber composite structures. In addition to higher quality, says Arevo, the Aqua 2 is able to print four times faster than its predecessor, enabling the rapid, on-demand production of large (up to one cubic meter) custom composite parts.
Additionally, the company closed its Series B financing round, led by Defy Partners and GGV Capital with participation from Khosla Ventures, Alabaster and others. This will bring the company’s total funding to $60 million. Defy appointed Brian Shin, a serial entrepreneur, investor and Defy Scout, to join Arevo's Board which includes Hemant Bheda (co-founder), Sonny Vu (CEO) and Bruce Armstrong (Khosla).
"Arevo's new platform enables fabrication of high-strength, low-weight carbon fiber parts, currently not possible with today's standard techniques," says Trae Vassallo, founding partner at Defy. "We are thrilled to be working with the team to help scale up this impactful technology."
These announcements come on the heels of Arevo's crowdfunding campaign to make its first direct-to-consumer products, the Superstrata bicycle and e-bicycle, said to be the world's first true unibody custom 3D-printed carbon fiber bikes.
Related Content
-
Hybrid process marries continuous, discontinuous composites design
9T Labs and Purdue applied Additive Fusion Technology to engineer a performance- and cost-competitive aircraft bin pin bracket made from compression-molded continuous and discontinuous CFRTP.
-
Welding is not bonding
Discussion of the issues in our understanding of thermoplastic composite welded structures and certification of the latest materials and welding technologies for future airframes.
-
Sulapac introduces Sulapac Flow 1.7 to replace PLA, ABS and PP in FDM, FGF
Available as filament and granules for extrusion, new wood composite matches properties yet is compostable, eliminates microplastics and reduces carbon footprint.