on display at JEC world 2022
The official theme of (Paris, France, May 3-5, 2022) was “sustainability,” and that was certainly evident in the many recycling and natural fiber based products on display.
Below are summaries of several new technologies and products I had the chance to see at the show. For more of CW’s JEC World coverage, see show recaps from CW editor-in-chief Jeff Sloan (coming soon) and senior editor Ginger Gardiner, and our on-site video recaps from the show floor.
Pressure vessel recycling research
National Composites Centre
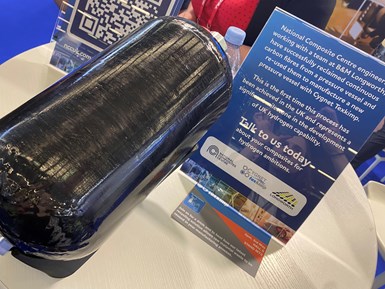
The National Composites Centre announced a new project to reclaim materials from carbon fiber composite storage vessels, for reuse again as new vessels.
Photo Credit: CW
During JEC World 2022, the National Composites Centre (NCC, Bristol, U.K.) announced success in a new project with partners Cygnet Texkimp (Northwich, U.K.) and (Edgworth, U.K.). Using Longworth’s DEECOM pressurized steam-based recycling process, launched at the show by the technology’s commercial distributor Cygnet Texkimp, NCC engineers reclaimed continuous carbon fibers from a recycled pressure vessel and demonstrated that these fibers remained intact enough to be remanufactured into a new pressure vessel. Next steps of the NCC’s research include analysis of the reclaimed material and recycled pressure vessel. The project is part of the NCC’s larger hydrogen program.
Rapid moldmaking with large-scale additive manufacturing
Massivit 3D
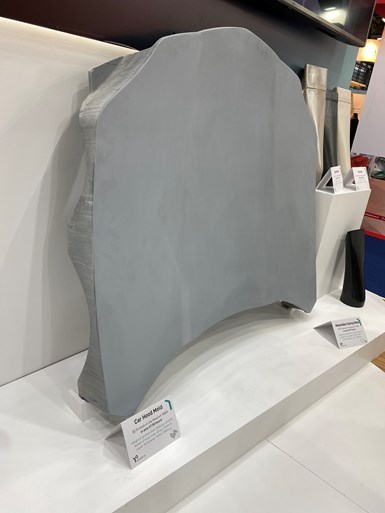
On display in Massivit 3D’s stand, this car hood mold was printed on the Massivit 10000 in 57.5 hours, weighing 64.06 pounds (28.60 kilograms).
Photo Credit: CW
Large-scale 3D printing systems provider Massivit 3D Printing Technologies Ltd. (Lod, Israel) held a press event and live demonstrations of its Massivit 10000 additive manufacturing (AM) system for rapid mold production. Using the company’s Cast In Motion (CIM) technology, the gel-dispensing printing head prints an outer sacrificial shell and casts an epoxy casting material inside that shell. The structure can be oven cured and is then submerged in plain water where the water-breakable shell crumbles away, leaving the epoxy mold for use in composite part manufacturing.
The machine on display at the company’s JEC World 2022 stand was sold to customer Lyons Industries, a U.S.-based luxury bath ware specialist. The system is said to reduce the toolmaking process time by up to 80%. Example tools on display at the show included a motorbike fairing mold built in less than 24 hours, a car hood mold built in 57.5 hours, a race car seat mold built in 42 hours and more.
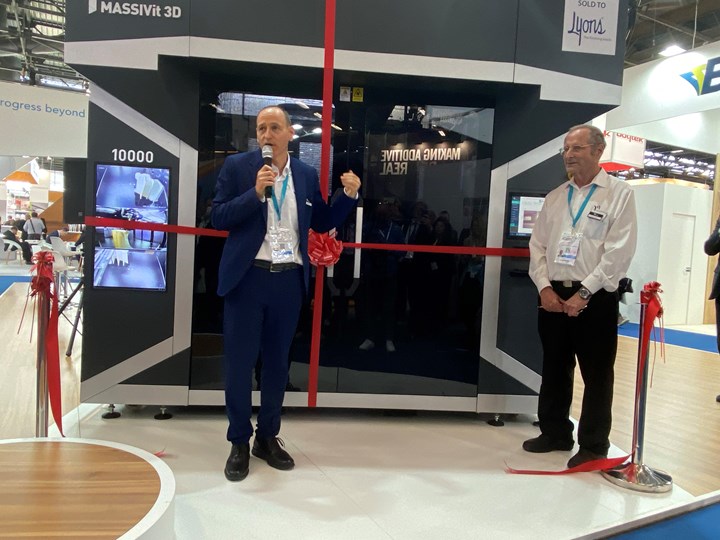
Massivit 3D demonstrated its Massivit 10000 machine at an on-site event during the show.
Photo Credit: CW
“Smart” recycling technology for carbon fiber scrap and EOL parts
Fairmat
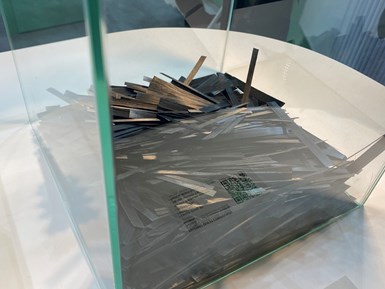
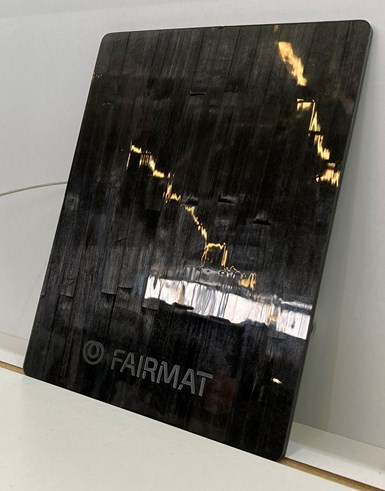
Fairmat displayed “bricks” made from its reprocessed carbon fiber composite scrap in a proprietary process (top photo), and panels made from the remolded materials (bottom photo). Photo Credit: CW
Recycling startup company (Paris, France) was one example of new recycling technology developments on display at the show. Fairmat, which has recently announced several partnerships with companies such as Hexcel for recycling prepregs, and Siemens Gamesa, Duqueine and Tarmac Aerosave for recycling of wind blades and aircraft, displayed the tape-like carbon fiber “bricks” that result from its proprietary recycling process, which can be reformed using new resin for new applications. Fairmat says it has developed an automation-based, dust-free cutting and fiber placement technology for processing composites manufacturing scrap or EOL parts into reusable materials at a constant quality. Key to its technology is an ability to use sensors and machine learning to better track and understand the properties of the materials being processed, which Fairmat calls “smart recycling.”
Emphasizing waste-free processing, recycled materials, natural fibers
Demgy
On display in the Natural Fibers village, plastics solutions provider (Saint-Aubin-sur-Gaillon, France) emphasized new R&D and commercial capabilities in zero-waste processes, use of natural fibers and recycled materials. On display included the Decathlon Traxium soccer shoes, made with recycled thermoplastic materials, a bicycle saddle and helmets made from natural fiber composites and a concept aerospace console built for Airbus Atlantic in partnership with Stelia Composite. The console was built from glass fiber/polyphenylene sulfide (PPS) organosheet in a combination of automated stampforming with injection overmolding.
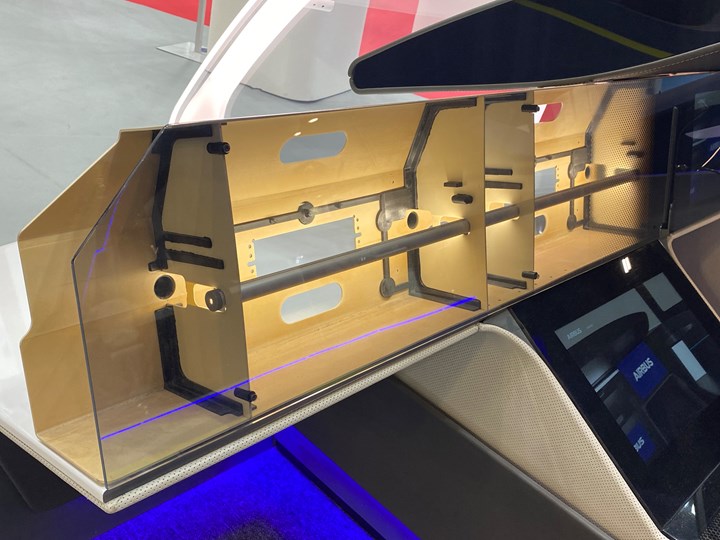
One of the products on display by Demgy at JEC World 2022 was this concept aerospace concept built using stampformed GF/PPS organosheet and injection overmolding. Photo Credit: CW
Recycled CF nonwovens for automotive structural components, other applications
Gen 2 Carbon
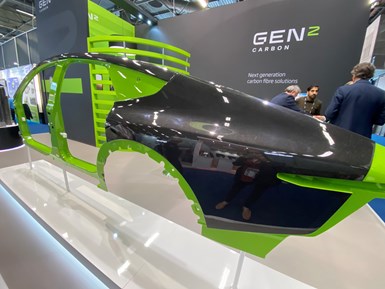
Gen 2 Carbon emphasized commercial applications of recycled carbon fiber nonwovens at its JEC World stand, including structural exterior components for the Lightyear One long-range solar car. Photo Credit: CW
Gen 2 Carbon (Coseley, U.K.), manufacturer of nonwovens from recycled carbon fiber scrap, demonstrated the growing uses and demand for its products in automotive, wind, batteries and other market areas. Gen 2 Carbon’s technology involves waterjet cutting and pyrolysis to reclaim long fibers from aerospace and automotive scrap materials for repurposing into nonwoven fabrics. The company plans to continue expanding its operations to meet growing demands.
On display at its JEC World stand, the company’s G-TEX M recycled nonwovens were used to build the structural body side and body exterior of the Lightyear One long-range solar car, built by partner Prodrive Composites (Milton Keynes, U.K.). According to Gen 2 Carbon, use of recycled materials in this application allows for lightweight and high performance while also reducing materials costs and environmental footprint compared to use of virgin carbon fiber.
Colored carbon fiber for sporting goods applications and more
Hypetex
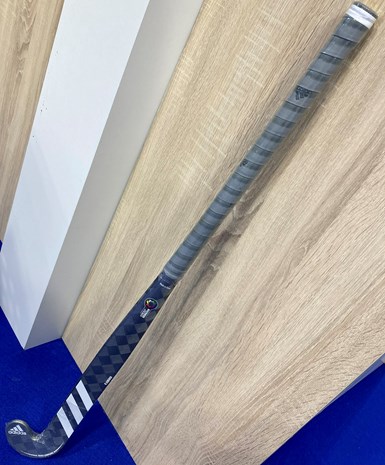
A finalist for a JEC Innovation Award, this Adidas field hockey stick was built in close design cooperation with Hypetex, using its carbon fiber fabrics and epoxy core.
Photo Credit: CW
(London, U.K.), manufacturer of colored carbon fiber and other fabrics, demonstrated growing use of its technologies as a lightweight, sustainable paint replacement for sporting goods and, soon, automotive applications. Hypetex materials currently are available in twill, plain weave, spread tow and unidirectional (UD) fabric formats, with new materials such as tapes and 3D printing filaments in development.
One application on display at the show was a field hockey stick developed with Adidas, that was a finalist for a JEC Composites Innovation Award. In this application, Hypetex worked with the manufacturing partner in the design and development of the part as well as providing the colored spread tow fabric and microcell epoxy core.
Natural fibers in new markets
Bcomp
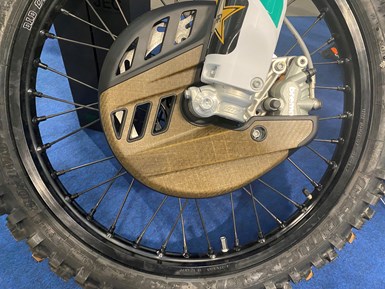
The award-winning brake cover on display by Bcomp demonstrates technology for combining natural fiber composites with other materials like PA6. Photo Credit: CW
Flax fiber materials specialist Bcomp (Fribourg, Switzerland) emphasized growing interest in and use of natural fiber composites for commercial applications, including a recent partnership with BMW Group working toward serial automotive components, and several flax fiber composite-intensive boats on display at the show.
Also on display in Bcomp’s stand was a motorbike brake cover that won a 2022 JEC Composites Innovation Award in the sports, leisure and recreation category. Developed with partner (Niederalm, Austria), the brake cover demonstrates use of KTM’s Conexus coupling technology to bond a flax fiber composite structure to a PA6 thermoplastic part.
Related Content
RTM, dry braided fabric enable faster, cost-effective manufacture for hydrokinetic turbine components
Switching from prepreg to RTM led to significant time and cost savings for the manufacture of fiberglass struts and complex carbon fiber composite foils that power ORPC’s RivGen systems.
Read MoreInfinite Composites: Type V tanks for space, hydrogen, automotive and more
After a decade of proving its linerless, weight-saving composite tanks with NASA and more than 30 aerospace companies, this CryoSphere pioneer is scaling for growth in commercial space and sustainable transportation on Earth.
Read MoreWe4Ce infused 2.5-3-MW rotor blade design passes validation test
Composite rotor blade structure design by We4Ce, mold and prototype production by InDutch Composites and fatigue testing by Suzlon Group has resulted in the novel blade’s IEC61400-5:2020 certification.
Read MoreSRI develops scalable, infiltration-free ceramic matrix composites
Work in two DOE projects is demonstrating C/C-SiC produced in 3-5 days with <5% shrinkage, <10% porosity and 50% the cost of conventional C/C and C/C-SiC.
Read MoreRead Next
JEC World 2022 day 1 recap
ÂÌñÏ×ÆÞ comes at you from Paris, France, as its editors navigate the landscape that is the first in-person JEC World trade show since 2019.
Read MoreAssembling the Multifunctional Fuselage Demonstrator: The final welds
Building the all-thermoplastic composite fuselage demonstrator comes to an end with continuous ultrasonic welding of the RH longitudinal fuselage joint and resistance welding for coupling of the fuselage frames across the upper and lower halves.
Read More“Structured air” TPS safeguards composite structures
Powered by an 85% air/15% pure polyimide aerogel, Blueshift’s novel material system protects structures during transient thermal events from -200°C to beyond 2400°C for rockets, battery boxes and more.
Read More