Is the market ready for another widebody aircraft?
This past week, the Airshow China 2016 event was held, from November 1 – 6 in Zhuhai, China. A notable outcome from the show, reported in several media outlets, was that Russia’s United Aircraft Corp. (UAC) and the Commercial Aircraft Corporation of China (COMAC) have advanced their plans for their collaborative twin-aisle widebody aircraft.
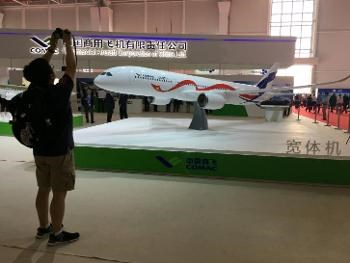
This photo from Ooyuz Web site shows the model of a UAC/COMAC joint venture widebody aircraft, at the Airshow China 2016 in Zhuhai.
This past week, the Airshow China 2016 event was held, from November 1 – 6 in Zhuhai, China. A notable outcome from the show, reported in several media outlets, was that Russia’s United Aircraft Corp. (UAC) and the Commercial Aircraft Corporation of China (COMAC) have advanced their plans for their collaborative twin-aisle widebody aircraft, so far referred to as Long-Range Wide-Body Commercial Aircraft (LRWBCA). A mockup of the new aircraft was on display at the show, showing 280 seats and 9-abreast economy seating.
An agreement was initially signed in 2012 between UAC and COMAC to study the feasibility of a widebody to compete with Boeing and Airbus. At the China air show event last week, COMAC released a document saying that it and UAC have progressed to a joint venture, to be based in Shanghai, which will start operations this year, presumably on initial designs and supplier agreements, says a Reuters market news story dated Nov. 1 by Brenda Goh and Kenneth Maxwell.
According to a Nov. 4 Aviation Week & Space Technology article by Bradley Perrett and Maxim Pyadushkin, UAC will build the aircraft’s composite wing, using the technology developed by AeroComposit (Moscow, Russia) for the Irkut MS-21 single-aisle commercial transport (see our story on that composite wing technology involving dry layup and infusion here: http://www.compositesworld.com/articles/resin-infused-ms-21-wings-and-wingbox). COMAC will make the fuselage, using both aluminum and composite, with final assembly to occur in Shanghai, according to the article. Power will be provided by Rolls-Royce or General Electric engines, with a possible Russian engine to be developed by 2030. Projected entry into service will be 2027, say the authors.
The joint venture is apparently focused on replacing the Airbus 330, as that aircraft ages over the next decade, and the Perrett and Pyadushkin article says that UAC and COMAC are claiming a 10% advantage in operating costs over competing models. Recent acquisitions of aircraft manufacturing technology and equipment companies by Chinese entities, including Brotje Automation (Rastede, Germany), Kuka Aerospace (Clinton Township, MI, US) and Aritex (Barcelona, Spain), indicate that COMAC will likely have access to experienced worldwide suppliers for high-tech assembly.
So will a new Chinese/Russian market entrant succeed, especially one with a composites-intensive design? Only time will tell as the new aircraft’s design progresses. Is the demand there for a new widebody aircraft in the current market? Another Aviation Week article dated Nov. 4 by Joe Anselmo cites a maintenance, repair and overhaul (MRO) market survey that shows weak demand for current wide-body aircraft (e.g., Boeing 777, 747, Airbus A380), with no sign of improvement. On the other hand, Airbus’ 2016 – 2035 Global Market Forecast report claims that China will need nearly 6,000 new passenger aircraft and freighters during that time period. The forecast projects 4,230 single aisle planes and 1,740 widebody planes for China, to meet what Airbus says will be the fastest-growing air passenger market, well above the rest of the world.
Related Content
Hybrid process marries continuous, discontinuous composites design
9T Labs and Purdue applied Additive Fusion Technology to engineer a performance- and cost-competitive aircraft bin pin bracket made from compression-molded continuous and discontinuous CFRTP.
Read MoreSulapac introduces Sulapac Flow 1.7 to replace PLA, ABS and PP in FDM, FGF
Available as filament and granules for extrusion, new wood composite matches properties yet is compostable, eliminates microplastics and reduces carbon footprint.
Read MoreWelding is not bonding
Discussion of the issues in our understanding of thermoplastic composite welded structures and certification of the latest materials and welding technologies for future airframes.
Read MoreCirculinQ: Glass fiber, recycled plastic turn paving into climate solutions
Durable, modular paving system from recycled composite filters, collects, infiltrates stormwater to reduce flooding and recharge local aquifers.
Read MoreRead Next
Developing bonded composite repair for ships, offshore units
Bureau Veritas and industry partners issue guidelines and pave the way for certification via StrengthBond Offshore project.
Read MoreAll-recycled, needle-punched nonwoven CFRP slashes carbon footprint of Formula 2 seat
Dallara and Tenowo collaborate to produce a race-ready Formula 2 seat using recycled carbon fiber, reducing CO2 emissions by 97.5% compared to virgin materials.
Read MoreComposites end markets: New space (2025)
Composite materials — with their unmatched strength-to-weight ratio, durability in extreme environments and design versatility — are at the heart of innovations in satellites, propulsion systems and lunar exploration vehicles, propelling the space economy toward a $1.8 trillion future.
Read More