Getting carbon fiber cost down
4M Carbon Fiber Corp. says its objective is to demonstrate that standard modulus carbon fiber can be made from textile grade PAN precursor using significantly less energy and in less than half the processing time, thus cutting carbon fiber manufacturing cost by about 50%. Plasma oxidation is the key.
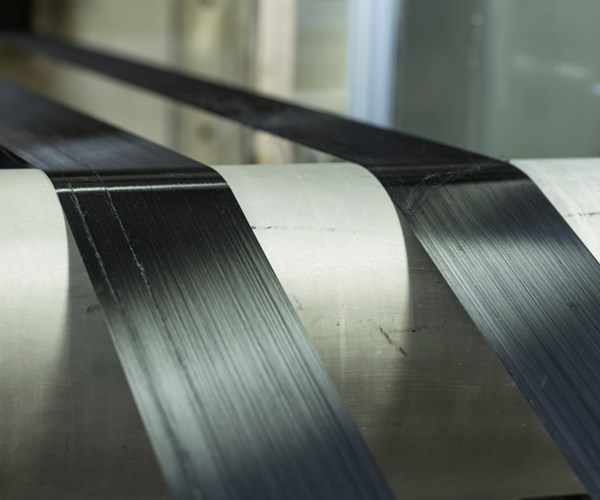
Plasma oxidation is playing a role in achieving low-cost carbon fiber from textile grade PAN precursor. Photo source: ORNL
If you’re reading this, you’ve probably seen the recent CW news story about 4M Carbon Fiber Corp. (Knoxville, TN, US) and its continuing efforts to produce standard modulus carbon fiber from textile grade PAN (polyacrylonitrile) precursor, in partnership with Oak Ridge National Laboratory (ORNL, Knoxville, TN, US), RMX Technologies, LLC (Knoxville, TN, US) and the University of Tennessee (here’s the link to the CW news story: /news/4m-oak-ridge-national-lab-and-rmx-technologies-to-manufacture-low-cost-carbon-fiber-from-textile-pan-).
The project got its start back in 2004, according to the Department of Energy’s Office of Energy Efficiency and Renewable Energy (EERE, Washington, DC, US) “Success Story” about plasma oxidation (here’s that link: ). RMX worked with ORNL to develop a plasma oxidation process to replace thermal ovens to oxidize or stabilize the PAN precursor, says the EERE story.
It’s well known that roughly half of the cost of producing carbon fiber is represented by the PAN precursor or starting material; the remaining half of the cost is in the conversion process from PAN to carbon fiber, says 4M Carbon Fiber Corp. Plasma oxidation technology has been demonstrated by numerous international carbon fiber makers to be much faster and use significantly less energy while making a better fiber.
EERE explains that conventional thermal ovens require a lot of energy and use molecular oxygen in the air to oxidize the PAN; this process is energy-inefficient and expensive, representing 18% of carbon fiber’s overall manufacturing cost, and takes as much as 120 minutes to complete.
RMX has developed, in partnership with ORNL, the process and hardware that generates a highly reactive gas from the air that reacts with PAN much faster than molecular oxygen, reducing processing time to less than 30 minutes and using 75% less energy. In addition, plasma oxidation ovens are one-third the length of thermal ovens with the same throughput, which could enable smaller production facilities. The EERE story says that plasma oxidation has the potential to significantly reduce the cost of carbon fiber manufacturing.
I was there in 2015 at the CW Carbon Fiber conference, held in Knoxville, TN, when RMX first presented this information, and announced the formation of 4M Industrial Oxidation to commercialize the process. At that time, C.A. Litzler (Cleveland, OH, US), a well-known maker of oxidation and carbonization equipment for carbon fiber, announced that it would offer plasma oxidation ovens to the market. The firms also announced their collaboration with Dralon GmbH, an acrylic fiber producer, to bring low-cost industrial carbon fiber to market.
4M Carbon Fiber Corp., the new name for 4M Industrial Oxidation, says its objective is to demonstrate that standard modulus carbon fiber can be made from textile grade PAN precursor using significantly less energy and in less than half the processing time, thus cutting carbon fiber manufacturing cost by about 50%. Litzler is working with RMX on development of the plasma oxidation equipment and says that its plasma process cuts the oxidation time by a factor of 2.5 to 3 times, to 25 to 35 minutes. Produced fiber has equal or better mechanical properties, compared to conventional equipment, says Litzler. Rodney G. Grubb, RMX board member and President of RMX’s subsidiary 4M Carbon Fiber Technologies has said that 4M has been working with Litzler for a year to develop the design and that progress is being made in scaling the plasma technology from pilot scale to production scale.
Combining the benefits of this technology with the low cost of textile fiber has the potential to cut carbon fiber manufacturing expense in half, says 4M Carbon Fiber Technologies. This would make carbon fiber more available for automotive lightweighting and open up more markets for carbon fiber that have been heretofor constrained by the high manufacturing cost.
Related Content
Combining multifunctional thermoplastic composites, additive manufacturing for next-gen airframe structures
The DOMMINIO project combines AFP with 3D printed gyroid cores, embedded SHM sensors and smart materials for induction-driven disassembly of parts at end of life.
Read MoreWelding is not bonding
Discussion of the issues in our understanding of thermoplastic composite welded structures and certification of the latest materials and welding technologies for future airframes.
Read More“Structured air” TPS safeguards composite structures
Powered by an 85% air/15% pure polyimide aerogel, Blueshift’s novel material system protects structures during transient thermal events from -200°C to beyond 2400°C for rockets, battery boxes and more.
Read MorePlant tour: Collins Aerospace, Riverside, Calif., U.S. and Almere, Netherlands
Composite Tier 1’s long history, acquisition of stamped parts pioneer Dutch Thermoplastic Components, advances roadmap for growth in thermoplastic composite parts.
Read MoreRead Next
Plant tour: Daher Shap’in TechCenter and composites production plant, Saint-Aignan-de-Grandlieu, France
Co-located R&D and production advance OOA thermosets, thermoplastics, welding, recycling and digital technologies for faster processing and certification of lighter, more sustainable composites.
Read More“Structured air” TPS safeguards composite structures
Powered by an 85% air/15% pure polyimide aerogel, Blueshift’s novel material system protects structures during transient thermal events from -200°C to beyond 2400°C for rockets, battery boxes and more.
Read MoreComposites end markets: New space (2025)
Composite materials — with their unmatched strength-to-weight ratio, durability in extreme environments and design versatility — are at the heart of innovations in satellites, propulsion systems and lunar exploration vehicles, propelling the space economy toward a $1.8 trillion future.
Read More