Vibration-canceling composite technology
Materials Sciences Corp.'s new product might be a solution for aircraft interiors noise and shock mitigating boat hulls?
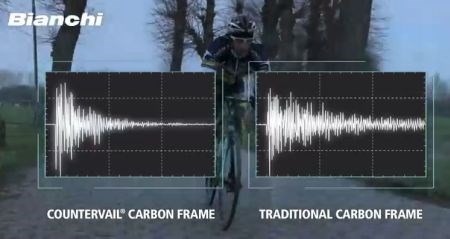
Materials Sciences Corp.'s COUNTERVAIL composite material helps cancel vibrations in the Infinito CV high-performance racing bicycle. SOURCE: Bianchi.
Materials Sciences Corp. (MSC, Horsham, Penn., USA) has provided design, analysis, engineering and testing services to the advanced composites industry since 1970. It has worked with the U.S. Army, Navy, Air Force, NASA, and DARPA as well as renowned industry leaders such as and McDonnell Douglas (now Boeing) Phantom Works. Its projects span a huge range of topics including multifunctional composites, damage tolerance, fire performance, armor systems, nanocomposites and design allowables methodologies, to name just a few.
One of its latest developments is a low acoustical insertion loss composite for sonar windows using MSC’s proprietary fiber commingling technology. The latter blends acoustical and structural fibers into a tailored fabric and multilayer composite which enables the high-strength, protective sonar dome to mimic the density and acoustical impedance of sea water through which the sonar waves travel. This then minimizes sonar wave scattering for a clearer, more accurate signal.
Now MSC — NOT to be confused with , supplier of MSC NASTRAN plus other FEA and simulation products — is expanding its corporate mission to include transitioning its proprietary, innovative technologies from R&D into commercial products. It has already released composite attachment nails for sandwich structures and dynamic simulator and database which provides accurate progressive failure modeling of composite structures.
MSC has commercialized MSC-CAN (left) and LS-DYNA (right) failure modeling tool.
SOURCE: Materials Sciences Corp.
But perhaps MSC’s most ingenious product is COUNTERVAIL (globally registered trademark), which combines traditional vibration damping layer concepts with a patented fiber preform to offer “unparalleled” vibration reduction in composite structures. The preform uses a fiber pattern that maximizes the vibrational energy dissipation achieved by an integrated viscoelastic damping layer. Damping performance has been shown to be at least 200 percent better than similar constructions using traditional methods. Lay-ups can be tailored to balance vibration curbing with stiffness and strength. COUNTERVAIL’s performance does indeed look impressive in this video by bicycle manufacturer Bianchi for its new Infinito CV model:
In fact, the Infinito CV was named “Bike of the Year” by and also was used by cyclist Lars Boom to win Stage 5 of the 2014 Tour de France race, a stage known for its bike-frame chattering cobblestones.
My thoughts fast forward to the potential solution this new technology may offer for two long-time challenges involving composites: (1) Composite interior panels which are thinner, lighter yet offer reduced transmission of noise into the aircraft cabin; (2) Mitigation of repeated and severe shock loads experienced by Navy SEALs and other occupants of special warfare marine vessels due to high-speed wave impacts.
The latter has caused chronic and acute injuries and risks mission performance. It has also seen huge amounts of money invested into solutions which may not yet offer the performance/price point combination that this new technology could provide. Shock mitigating designs have been proposed for the hulls, decks and seats used in these boats. CW reviewed one example in the 2011 article, “Re-inventing the RHIB: Shock Mitigation”.
Meanwhile, noise transmission from air rushing past an aircraft fuselage is tricky because noise is vibration, which traditionally has been most easily addressed by adding weight — hence, the use of lead around superyacht engine rooms. Viscoelastic materials are a more modern alternative, but they too tend to be heavier than desired in aircraft and must also pass fire, smoke and toxicity (FST) regulations.
COUNTERVAIL, however, may have opened a pathway that could yet be refined to offer a solution. There are so many materials innovations affording improved flame resistance, for example University of Texas’ development of nanoclay fillers used to drop the flammability of polyurethane foam and the latest thermoplastics which offer both FST performance and higher toughness.
I’ve been invited to visit MSC’s newest facility in Greenville, South Carolina. So keep watching for our next report on Materials Sciences Corporation, COUNTERVAIL and where both are headed next.
Related Content
Recycled carbon fiber composite panels power 40% lighter, durable semi-rigid solar panels
Designed for auxiliary power use while traveling via boat or RV, Italian startup Levante’s custom flexible or standardized semi-rigid solar panels combine the benefits of ReCarbon’s rCF and thermoplastics.
Read MoreAnemoi installs 35-meter-tall composite rotor sails on Sohar Max maritime vessel
Carbon fiber-reinforced epoxy composites are key to building these long-lasting wind propulsion technologies for energy-efficient watercraft.
Read MoreAl Seer Marine, Abu Dhabi Maritime unveil world’s largest 3D-printed boat
Holding the new Guinness World Record at 11.98 meters, the 3D-printed composite water taxi used a CEAD Flexbot to print two hulls in less than 12 days.
Read MoreLarge-format AM speeds plug production for manufacture of composite boat molds
Hungarian manufacturer Rapid Prototyping transitioned its conventional foam milling process to 3D printing to produce faster, higher quality, recyclable foam plugs and composite boat molds.
Read MoreRead Next
“Structured air” TPS safeguards composite structures
Powered by an 85% air/15% pure polyimide aerogel, Blueshift’s novel material system protects structures during transient thermal events from -200°C to beyond 2400°C for rockets, battery boxes and more.
Read MoreVIDEO: High-volume processing for fiberglass components
Cannon Ergos, a company specializing in high-ton presses and equipment for composites fabrication and plastics processing, displayed automotive and industrial components at CAMX 2024.
Read MoreAll-recycled, needle-punched nonwoven CFRP slashes carbon footprint of Formula 2 seat
Dallara and Tenowo collaborate to produce a race-ready Formula 2 seat using recycled carbon fiber, reducing CO2 emissions by 97.5% compared to virgin materials.
Read More